Q&A事例(1)鉄
成分分析装置もなく温度計もなかった古い時代に,鋳物師達はどうやって鋳鉄鋳物の溶湯性状を判断したのでしょうか.
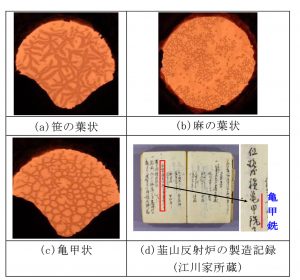
図1 ねずみ鋳鉄における湯面模様
昔の鋳鉄鋳物師達は,湯面模様によって溶湯性状を判断したと考えられます.キュポラ鋳鉄溶解では,溶湯性状が良くなるにつれて,湯面模様が笹の葉状から,麻の葉状,亀甲状へと変化していく事が知られています(図1の(a),(b),(c)).
湯面模様とは,SiO2+2C=Si+2COの反応式に基づいてSiO2被膜が発生した時に見られる現象です.SiO2膜と溶けている溶湯では輻射率に違いがあるために,人間の目に模様として可視できるようになったものです.Sが0.02%以上,Siが0.5%以上入ることによって,表面張力が変化し,その表面張力の差によってマランゴニ対流が発生し,湯面模様が生じることになります.
キュポラでしか湯面模様が現れないと言われてきたのは,コークスからSが入りマランゴニ対流が生じるためです.電気炉溶湯も,0.02%以上のS,0.5%以上のSi,SiO2被膜発生温度,適量のC量の4点が満たされれば,湯面模様が現れます.
1983年の鋳鉄溶解ハンドブックでは,キュポラ溶解の38社のうち湯面模様が出ないと回答したのは1社のみでした.低周波炉(電気炉操業)では47社のうち32社が出ないと回答し,15社は出ると回答しています.これは前述したS量の差によるものと思われます.また,約160年前に行われた韮山反射炉の製造記録においても,大砲を鋳造する時のみに亀甲銑が用いられたと書いており,いみじくも亀甲という名称が一致しています(図1の(d)).このように,昔の鋳物師達は,湯面模様の観察によって鋳鉄鋳物の溶湯性状を判断し,健全な鋳物を作ったと考えられます.
(『鋳造工学』90巻5号掲載)
FC(ねずみ鋳鉄)に,お酢などを使用して意図的に錆びさせてその錆を磨き,野菜クズなどを炒めて熱し,油を塗る(熱する・油を塗る工程は何度か行う)と,一度錆びさせたことで油の染込みが良くなって錆びにくくなるという効果は期待できるでしょうか?
「錆びにくくなるという効果」とありますので,最初に南部鉄瓶の防錆法について簡単に説明します.南部鉄瓶のお湯が入る内面の防錆は酸化皮膜で,模様のある外面は漆(うるし)の皮膜で防錆しています.内面の酸化皮膜(黒錆,Fe3O4)は鉄瓶を炭火中で800℃程度に加熱して生成させます.外面の皮膜は,炭火中で生成した酸化皮膜をいったん落とした後,黒色鉄瓶の場合は漆と鉄粉を混ぜたものを,茶色鉄瓶の場合は漆と弁柄(ベンガラ:酸化第二鉄)を混ぜたものを400℃程度に熱した鉄瓶に焼き付けて皮膜を生成させます。鉄瓶の表面は細かい凹凸がありますので,防錆膜はこの凹部に入り込み,なかなか落ちません.
お問い合わせのねずみ鋳鉄では油で防錆効果を期待しているようですが,この素材の表面に細かい凹凸があれば,凹部が油溜まりとなって防錆効果を発揮することが期待されます.錆を油溜まりとして使用する意図が見受けられますが,鉄の錆には鉄瓶などに施されている黒錆(Fe3O4)と湿度のある空気中に放置することで自然発生する赤錆(Fe2O3)があります.赤錆は隙間が多く,鉄そのものを腐食させ,ボロボロにしていく性質を持ちますが,黒錆は緻密で強いのが特徴です.どちらの錆が油溜まりとして効果があるかは試してみないと分かりませんが,黒錆は苛性ソーダなどのアルカリ溶液中に鉄を浸して煮沸するか,鉄瓶の場合ように高温に加熱することで生成されます.
(『鋳造工学』90巻5号掲載)
自動車部品では燃費向上のために部品軽量化,特に薄肉化を求められていますが, ダイカスト部品の軽量化を進めるにあたって気を付けることは何でしょうか?
地球環境問題の解決のために自動車の軽量化は大きな課題となっています.従来から適用されているアルミニウム合金ダイカスト部品を軽量化するためには,高強度化と薄肉化が重要となります.もともとダイカストという工法は薄肉製品を得意とする工法ですが,さらに薄肉化しようとすると,様々な問題が出てきます.
まず,溶湯充填時に溶湯が冷却されやすくなるために,湯回り不良を起こす可能性が高くなります.また,壁面などは製品強度が確保できれば薄肉化は可能ですが,ボス部などの薄肉化ができない部位が薄肉部の中に存在することによって,ひけ巣などの内部欠陥が集中することが考えられます.さらに,凝固時やイジェクト時の高温強度の低下により,割れを生じることが懸念されます.寸法精度の問題も出てきます.
湯回り不良を防止するためには,溶湯が凝固を始める前に充填させる必要があります.表に肉厚と充填時間の関係(日本ダイカスト協会編:「ダイカスト技能者ハンドブック」(2012))を示します.この時間内に充填させるためにできる限り充填距離の短い鋳造方案にしたり,射出速度を上げたりします.あまり射出速度を上げると金型との焼き付きが生じやすくなるので,注意が必要です.
厚肉部のひけ巣を防止するためには,凝固過程における溶湯補給性を確保することが重要になります.薄肉部と厚肉部が混在したような形状の場合は,薄肉部が先に凝固するために厚肉部への溶湯補給ができなくなります.薄肉部へのリブの追加などを行うことにより溶湯補給性を上げるといったことも有効な方策になります.リブの追加は湯流れ性の改善や高温時の強度向上にもつながります.
薄肉のダイカストを成立させるためには,鋳造方案や条件の検討だけではなく,製品形状の適正化も重要になりますので,設計者と生産者がよく検討することが必要です.
(『鋳造工学』88巻8号掲載)
球状黒鉛鋳鉄の黒鉛粒数や球状化率を測定する際に,15μm以下の小さい黒鉛は無視することになっています(JIS).15μmに決めた根拠は?
球状黒鉛鋳鉄について日本独自の黒鉛形状分類法と黒鉛球状化率の判定方法を定めた
記録が「鋳物40巻(1968)P296」に紹介されています.当時の日本鋳物協会特殊鋳鉄部会の10数回の委員会による審議の結果作成されたものです.球状化率算出法を前出の記録から引用して記述すると次のとおりです.“試料の任意の場所について手札版またはこれに順ずる大きさの倍率100の顕微鏡組織写真をつくり,写真面の両対角線をそれぞれ中心として巾3mmの直線を引く.これら両対角線帯の上に少しでも乗る黒鉛の全数が10個以上を対象として数を算出する.この場合2mm以下(実際20μm)の粒はかぞえない.本判定法では顕微鏡に現れる黒鉛粒の形態を6種類に分類し,それぞれに形状係数を与えており,各種の粒数に形状係数を乗じてその総和から球状化率を算出する.試料被検部における5視野について平均値で表す”と紹介されています.
特殊鋳鉄部会では各委員が多くの球状黒鉛鋳鉄の試料を作製し,その球状化率を求めると同時に機械的性質を実験しています.その結果,球状化率が50%以下においては球状化率と機械的性質の関係には多くのばらつきがみられたが,球状化率50%以上では引張強さ及び伸びのいずれも有意な関係がみられたと報告しています.
球状化率を求める作業の迅速性と球状化率の正確性の両面から合理的な方法として,微小黒鉛や介在物を除いて球状化率を算出しても球状化率と引張強さや伸びの関係が有意になることから,黒鉛の大きさの閾値として,当時は20μmを決めて作業したものと推定されます.
現在の球状黒鉛鋳鉄品JIS G 5502(2001)は対応国際規格ISO 1083と技術的な差異がなく整合されていますが,2001年版においては1.5mm(実際の寸法15μm)以下の黒鉛及び介在物は球状化率の判定の対象としないとされています.とくに薄肉品の場合,黒鉛も小さくなるため,企業によっては独自に小さい黒鉛まで測定の対象にしている場合があります.
最近では画像解析によって迅速に,また,向上した正確さで測定が可能になり,黒鉛の大きさの閾値も選択できるようになっています.球状黒鉛鋳鉄品によって生産者と使用者間での協定で取り決められることもあるのではないかと考えられます.
(『鋳造工学』90巻8号掲載)
最近の自動車のボディはマルチマテリアル化が進んでいると聞きます.しかし,電位差の異なる材料を用いると腐食が進むと思いますが,大丈夫ですか?
自動車の軽量化のために,軽量材料を適用していくことが検討され,高級車やスポーツカーを中心に,アルミニウム合金やマグネシウム合金が使われてきています.近年の傾向として,機械的性質やコストの観点から,種々の材料を適材適所に組み合わせて使うマルチマテリアルボディが増えてきています.ご指摘のように,いろいろな種類の金属材料を用いるとガルバニック腐食(異種金属接触腐食)が起きる可能性があります.ガルバニック腐食とは,電解質水溶液中において異種金属材料を接触させた時に生じる腐食現象であり,電位が卑な金属がアノードに,電位が貴な金属がカソードになり局部電池が形成されます.このため,電位が卑な金属の腐食速度が増大します.マグネシウム合金やアルミニウム合金は電位が卑であるために溶液中に溶け出し,腐食が進みます.
ガルバニック腐食を防止するためには,異種金属同士が接触しているところで局部電池を作らせないことが重要です.金属の表面に塗装や表面処理をすることにより,金属同士を絶縁したり,腐食電位差の小さい材料を間に挟んだり,水がかからないあるいは溜まらないような構造にしたりしています.マルチマテリアルボディの開発には,材料そのものの開発や接合技術に加えて,このような耐食性を向上させるための技術開発も重要になります.
(『鋳造工学』90巻8号掲載)
回転曲げ疲労試験により得たS-N曲線において,FCD700材で鋳放し材よりも熱処理材の方が傾きが立っているのは何故でしょうか
FCD700材を熱処理すると引張強さ,硬さが向上する様に静的機械的性質が上昇します.しかし,伸びや絞りといった延性特性は低下します.これはFCD700材の鋳放し材がフェライト組織とパーライト組織の二相組織であるのに対して,熱処理材はパーライト組織の単相になるからです.
球状黒鉛鋳鉄において基地組織中に存在する球状黒鉛はマトリクスとの接着強度はほとんど無いことから,試験片内部に球状の空孔を含んだ材料と見なせます.また,鋳鉄特有の引け巣なども疲労破壊の起点となることが知られております.そのため,応力を負荷すると,これら黒鉛の周囲や引け巣端部には応力集中が生じます.この応力集中箇所を起点として,疲労亀裂が発生し,その亀裂が進展した後,ある限界の亀裂長さに達すると疲労破壊を生じます.FCD700材の熱処理材はフェライト組織に比べて硬く,静的強度(特に0.2%耐力)が高いパーライト基地であるため,疲労亀裂の発生応力は高くなります.しかし,ひとたび疲労亀裂が発生すると,フェライト組織に比べ,亀裂に対する抵抗(じん性)が小さいため,亀裂進展速度は速く,疲労亀裂はほとんど応力振幅の繰返しを伴うことなく疲労破壊に至ります.一方,鋳放し材はフェライト組織を含むため,疲労亀裂の発生応力が低くても亀裂進展速度はパーライト基地に比べて遅く,亀裂が破断までに達する繰返し数は応力振幅の大きさに依存します.その応力振幅が小さいほど,繰返し数は長くなります.すなわち,両材のS-N線図の傾きは,疲労亀裂が発生してから破断までの繰返し数の差が影響していると言えます.
(『鋳造工学』88巻2号掲載)
Kモールド試験法とは何ですか?
溶湯の品質は 化学成分,ガス,介在物,温度で評価されます.Kモールド法は,溶湯中に含まれる介在物を調べる目的で,破断面観察法として一般に使用される方法です.図1に示すようなアルミニウム製の鋳型に溶湯を鋳込み,凝固させた後に得られた短冊状の試験片をハンマーなどで5~6片に割り,その破面に現れた介在物の数を求める方法です.
図2に介在物の少ない破面と多い破面を示します.評価方法としては,全ての破面に現れた介在物の総数を破面の総数(一片当たり2破面)で除した値を求めます.この値をK値と呼びます.その評価は,表1に示すようにK値によってランクA~Eに分類して行い,鋳造に用いてよい溶湯品質であるかを判定します.
(『鋳造工学』88巻2号掲載)
私の職場では無機中子を使用し低圧鋳造アルミ合金鋳物を製作していますが,原因不明の中子折れが多発しています.今一番怪しいのは中子のなりより性だと思うのですが,なりより性の測定方式などは何があるのでしょうか?
なりより性とは,鋳型に溶湯が注入されて,凝固すると同時に収縮しますが鋳型が鋳物の収縮に応じて,ともに収縮に応じてくれる性質をいう用語で可縮性とも言います.これは非常に重要なことで,もしこの性質がないと鋳造品は肉の薄い部分で割れたり,中子折れ不良が発生します.
試験機として,英国,米国ではBCIRA(英国鋳物研究所)が開発した熱間たわみ試験機(Hot Distortion Tester)を用いて測定していますが国内では各RCS・粘結剤メーカーが独自の方法で行っています.手順は決められた寸法の鋳型を造型後,熱間・冷間,酸化・還元雰囲気にて鋳型の変位量をレーザー変位計等で測定します.熱間の場合は,加熱器等で800℃まで加熱し,加熱による鋳型の変位量を測定します.
強度,破壊時のひずみはバインダーの種類,量及び,鋳物砂の熱膨張量によって変わりますが,一般的に常温でのなりより性は有機に比べ,無機中子は小さい傾向があります.
参考文献:鋳物第66巻(1994)第7号517-522
(『鋳造工学』91巻8号掲載)
鋳鉄材料の規格は引張強さや伸びで規定されていますが, 値を求めるときの有効数字はどこまでですか? 具体的に教えてください.
引張試験は特殊な場合(規程の試験片が採取できないなど)を除いて,基本的にはJIS Z 2241「金属材料引張試験方法」に則った方法で実施する必要があります.一般に引張試験結果は, 材料規格に規定のない場合は, 少なくとも次の精度で丸めなければならない(JIS Z 8401 数値の丸め方)と定義されています.
強度の値:MPaの整数に丸める
破断伸び(%):整数に丸める
また,各々の原断面積を求めるためには,規定寸法の少なくとも0.5%(JIS 4号試験片の場合,0.07mm)の数値まで測定し,標点距離は規定の寸法の0.4%(JIS 4号試験片の場合,0.2mm)の精度で測定するという規定があります.
応力を算出するための試験片断面積の測定には,ノギスやマイクロメータを使用します.一方,荷重については,最近はロードセルからデジタルデータで計測することが多いようです.つまり,試験片寸法の測定値と荷重の有効数字で強さ(応力)の精度が決まります.いずれも有効数字3桁は保証されていると思いますので,1MPaの精度で表記すれば十分かと思われます.一方,伸びや絞りを求めるには,破断後の破断面を突き合わせた状態で標点距離あるいは最小部の断面寸法を測定します.仮に精度の高い測定器具を使用したとしても,突き合わせた状態で測定していることから,厳密にその精度を持った正確な測定ができているとは言えません.そのため,伸び,絞りの表記としては,1%の精度で算出します.
したがって,強さや伸びを求める際は,まず測定される値の分解能が基準を満たしているかどうかを判断した上でそれぞれの値を測定することが必要となります.
(『鋳造工学』91巻8号掲載)
残留Mgが低いFCD溶湯を丸棒試験片(例えば、直径φ15,30mm)に鋳込んだとき、球状化率が高い部分と低い部分が図1のように何層ものリング状に分布するのは何故でしょうか?
丸棒試験片にリング状に破面の色が何層も見える現象は,その丸棒試験片を得る条件が関係し,例えば注湯温度や解枠後の冷却条件(基地組織への影響)がばらつくことも一因です.FCDのパーライトとフェライトが混在する組織を前提として考えてみると,破面の外径から白→黒→白(φ15mm)→黒(φ30mm)の破面色を示すのは,白と黒の破面(組織)粗さが異なっていると考えられます.フェライトが多い延性破面では,破面の凹凸が大きくなり,光の反射や屈折が多くなることから黒く見えます.逆にパーライトが多く破面の凹凸が小さいところは,光が反射するので白く見えます.
破面の色は基地組織(パーライト率等)以外に黒鉛球状化率とも関係があり,経験上丸棒破面の平均球状化率が25~50%程度と低い試料(残留Mg量0.020mass%程度)に,このようなリング状破面が現れます.一般的に冷却速度が大きいところは凝固速度も大きくなり1),そのため冷却速度が大きい外周部は,黒鉛粒数が多く,球状化率もよくなります.一方,丸棒径が細いφ15mmでは中心部に堤らの過冷却説2)に類似する過冷球状黒鉛が晶出されやすいため,球状状率も高くなると考えられます.以下の文献も参考にしてください.
1)中江:鋳物,67(1995)284
2)堤,松川:鋳物,51(1971)342
(『鋳造工学』88巻1号掲載)
鋳造」と言う言葉を使った人,または 「Casting」を「鋳造」と決めた人を教えて下さい.
鋳造は人類の歴史の中で最も古い時代に人々が身に着けた金属の熱間加工技術であり,既に約6000年の歴史を持っています.中国では紀元前1700~1000年に青銅鋳物の製造の最盛期を迎え,高度な鋳造プロセスを確立しています.中国の商朝(紀元前1600年~1046年)には重さ875kgの司母戊方鼎(青銅鋳物),紀元前513年には世界でもっとも古い鋳鉄鋳物―晋国鋳型鼎(重さ約270kg)を製造しています.
文字として最も古い記録を残したのは甲骨文(商朝時代の遺跡から大量出土)で,中には「鋳」と言う漢字を「」のように表現しています.「
」は両手で鬲鼎(れきてい)「
」中の溶湯を鋳型「
」に鋳込むことを意味し,「
」は中子を意味しています.
文字が出現する前,人々は既に「鋳造」という言葉を使っていたと思います.しかし誰がいつ頃作り出したか,残念なことにはっきりした記録は残されていません.
(『鋳造工学』91巻6号掲載)
鋳物の化学組成を蛍光X線分析やICP分析装置で簡易・短時間で分析していますが,どのような原理で行われているのでしょうか?
物質は,いくつもの元素の組合せで出来ています.物質にエネルギー(熱エネルギー,電気エネルギー,光エネルギーなど)を加えるとその強さに応じて相変態(固相→液相→気相そして発光)します.この光が何かというと,物質を構成している各元素のスペクトル線(光)が混合したものです.理科の時間に炎色反応の実験で,アルコールランプの炎に金属や金属塩などを付けた白金線をかざすといろいろな色の炎に変化すること,夏の夜空を彩る打ち上げ花火や線香花火の色も火薬の爆発エネルギーで花火に仕込まれた金属や金属化合物の発光なのです.これらの光の色は,各元素が有する固有の輝線スペクトル線(光)によるものです.
この原理を利用したのが固体発光分光分析,蛍光X線分析,ICP分析,原子吸光光度分析などの機器分析装置です.これらの装置は,分析する物質に高エネルギーを加え物質を構成する元素を発光させる部分,光を各元素のスペクトル線に分解(分光)する回折格子(一種のプリズム),分光された各元素のスペクトル線を受光して電気信号に変換するのが光電子増管やCCD素子,検量線そして結果を表示する部分から構成されています.強いスペクトル線(光)の光度は,含有量が多い程を強くなるので電気信号も強くなります.予め入力されている検量線(曲線)は,ある元素の含有量変化させた試料を化学分析によって測定しy軸に,それぞれの含有量の試料のスペクトル線の強度を機器分析装置で測定しx軸にプロットしたものです.
以上の様な原理で各元素の光の強度と含有量から成る検量線から瞬時に含有元素の含有量を算出・表示することが出来るようになっています.
※なぜ輝線スペクトル線が出るのかは,炎色反応,スペクトル線などをキーワードにWeb検索されると良いでしょう.スペクトル線は可視光線(赤の波長:760〜830nm〜紫の波長:360〜400nm)とは限りませんが,機器分析装置は殆どの元素のスペクトル線を分光,受光出来るようになっています.目に見えない電磁波の波長は紫外線→放射線と短くなっていくのですが,昆虫や放射線検出器は捉えることが出来ます.Li深赤色,Na黄色,K淡紫色,Cu緑色,Ca橙赤食,Sr紅,Ba黄緑色など
(『鋳造工学』89巻10号掲載)
鋳鉄を鋳肌のまま使用する場合と表面仕上げを施した場合では,強度にどれほどの差がありますか?
鋳鉄の鋳肌には砂との焼付きによる黒皮酸化層や表面での欠陥(巣や介在物,あるいは異常組織)などが存在します.さらに鋳肌の表面粗さは不均一であり,その凹凸が著しい場合には応力集中による影響を考える必要もあります.引張強さはそれらの要因があっても,粗さの凹凸が極端に大きくない限りはあまり影響しませんが,伸びは大きく低減します.つまり,ねずみ鋳鉄の強度には鋳肌はあまり影響しません.球状黒鉛鋳鉄では鋳肌付き試験片と機械加工試験片の応力-ひずみ線図を比較しますと,弾性域の範囲で両者は大きく相違しませんが,塑性域の範囲では鋳肌の影響を受けて塑性変形能が極端に低下します.たとえば,6号けい砂程度までの粗さ(Rz=250μm以下)では機械加工試験片に対して,鋳肌付き試験片の引張強さは90%以上を確保できますが,伸びは大きく減少して50%程度になることもあります.鋳肌がさらに粗くなれば,両者はさらに低下します.曲げ強さ,衝撃値及び疲労強さは鋳肌の影響がより明確に現れます.一般には後処理としショットブラストが施されますので,その効果もあって鋳鉄の引張強さは鋳肌の影響をあまり受けないと考えて良いです.
(『鋳造工学』87巻10号掲載)
Al-Si合金などは、ひけ巣を設計上ではどのように考え,現場ではどのような対応をしているのでしょうか? また,存在するひけ巣の検出方法とその評価方法はどうしているのでしょうか
アルミニウム合金は凝固収縮が大きいため,ひけ巣が生じやすくなります.ひけ巣があると機械的性質が低下したり,リーク不良を起こしたりします.このため,ひけ巣は無いに越したことはありません.製品を設計するときには,できる限りひけ巣の生じないような形状となるように設計します.なるべく肉厚一定に設計したり,厚肉部になりそうなときには,裏から肉を盗んだり,加圧ピンを設置したりします.しかし,どうしてもひけ巣が避けられない形状となる場合があります.そのような場合には,製品機能上問題が生じない部位にひけ巣が生じるような形状と鋳造条件を設定します.設計図面には「有害な巣無きこと」などといった注記がされることがありますが,製品機能上有害でないものはあってもやむを得ないということになります.
鋳物外部に生じるひけ巣は目視で確認できますが,内部のひけ巣を検出するためには,X線CTなどを使用するのが一般的です.最近の設備は性能が良くなっており,0.5mm以下の内部欠陥も検出できるようになってきています.しかし,量産する全ての鋳物を検査するわけにはいきませんから,製品開発時にどの程度のひけ巣まで許容できるのかを耐久試験などで確認しながら生産条件を決定し,条件管理を行うことで品質を保証します.製品機能にかかわる特性については,リークテストなどの検査を行い品質保証します.また,内部欠陥や強度については,定期的に抜き取り検査を行います.
(『鋳造工学』89巻10号掲載)
アルミダイカストの溶湯保持温度を極力低くしたいのですが,何度ぐらいまで低くすることができますか
ダイカストの溶湯温度は通常660℃~680℃の範囲で設定されています.溶湯温度を低くすると第1にスリーブ中で凝固が進み,湯回り不良や湯境などの充填不良が発生します.また第2に保持炉の中でスラッジが生成し,ハードスポットによる加工トラブルを起こすことがあります.
第1のスリーブ中での凝固は,充填量が少なく,注湯時のスリーブ充填率が20%を切るような場合は,溶湯温度の影響が大きく溶湯温度を下げることは難しいです.
比較的充填量があり,スリーブ充填率が30%以上ある場合は,第2のスラッジの生成を考慮する必要があります.
ADC12の場合は,スラッジの生成は主に溶湯中のFe,Mnの混入量に影響されます.ADC12のスラッジ発生限界温度Tが調べられており,次式が示されています.
%Fe+(3.34-((T-630)/714)%Mn=2.39+(T-630)/152
(%Feは,Feの含有量,%Mnは,Mnの含有量)
この式から求められる温度が溶湯温度を低くできる限界温度になります.つまりFeおよびMnの含有量を低く抑えることでスラッジの発生を防ぐことができます.Fe,Mnを管理することが前提ですが,国内で入手できるAD12.1地金の成分管理範囲で溶湯温度を下げるとした場合,現実的に低減可能な温度は640℃程度と考えます.なおCrは通常はインゴットに含有されない元素ですが,スラッジ生成への影響がさらに大きいので材料納入メーカに管理を要求する必要があります.
参考文献;納,豊田,津村,鈴木,古屋,永山:軽金属VOL36(1986)813
(『鋳造工学』87巻10号掲載)
銅合金溶湯の脱酸にCu-P合金が使われますが,なぜ脱酸が出来るのでしょうか?
銅合金の溶解は,通常弱酸化性雰囲気で行われるので,溶湯中に溶け込んだ酸素[O]が存在します.この状態で凝固が進行すると水素と結びついて鋳塊中に水蒸気ガス気泡を形成する場合や,易酸化性金属元素と結合してその金属酸化物となって鋳造品の品質を大幅に低下させます.そのため,溶解段階で溶湯中の酸素を取り除く処理が,品質向上のための重要な工程となります.
溶湯中の酸素を除去するには,合金元素より酸素との親和力の強い元素Al・Si・Be・等(各種便覧に酸化物生成自由エネルギー図として掲載されていますのでご参照ください)を加えて系外に除去してやることが有効です.しかし,酸素との親和力の強い元素P以外の元素では,溶け込んだ酸素がその元素の酸化物[MxOy] の形で溶湯中に残留するので,酸素を取り除いたことにはなりません.純銅系及び青銅系合金において,Pを添加した場合は,脱酸生成物のP2O5が350℃で昇華して溶湯から蒸発してくれるため,完全に酸素を取り除く事が出来ます.但し,過剰なPを添加した場合,凝固温度範囲が広くなるので,適度な量を加えることが重要です.
他の銅合金(銅-アルミニウム系,および銅-黄銅系)は,銅より酸素親和力の強い元素が合金元素として含有されているので脱酸の必要性はありませんが,溶湯中に懸濁して存在している酸化物を除去する為フラックス処理が必要です.
(『鋳造工学』92巻2号掲載)
欠陥の原因を簡単に判別する方法はないでしょうか?
【鉄の場合】
鋳造各工程のセンシングと,欠陥部の画像解析などにより欠陥名を判定し,ビックデータからAI知能が欠陥原因を判別することが近い将来であり,この時は簡単かつ瞬時に判別できる様になると思います.
現時点の方法としては,欠陥名を最初に判別すれば,原因は文献やデータベースなどから得ることが簡単な方法と言えます.対策事例も文献やデータベースに記されています.
具体的には,最初に欠陥名を発生位置,鋳造条件,不良率,外観,顕微鏡などから判定します.欠陥の発生原因が比較的単純な欠陥はこれで欠陥名が分かりますが,肉眼では欠陥発生機構の分からない場合は組織,SEM・EDS,ONH,化学成分などを追加して判定します.欠陥名が分かれば分類と原因を記した「学会創立75周年記念出版『鋳造欠陥とその対策』」,「国際鋳物欠陥分類図集 (1975年)」,「鋳鉄鋳物製造現場のQ&A(日本鋳造協会)」,「Web欠陥大百科(日本鋳造協会)」などの文献やデータベースから原因と対策事例を知ることができます.なお,これらには様々な事例から得られた対策が列挙されていますので,自社の鋳造工場に最適なものを判断して選ぶ必要があります.鋳造工場毎に製品,使用材料,工程などが限定されていることから発生する鋳造欠陥もパターン化されていることが多く,社内の経験を有する専門家の意見や時には社外の専門家の意見を参考にするのが良いと言えます.
鋳造の歴史は欠陥対策とも言え,欠陥名の判別方法,欠陥事例,対策事例は既に膨大なものとなっていますので,これらを利用することが質問の答えではないかと思います.
【非鉄の場合】
非鉄鋳物の欠陥は,大きく分けると外部欠陥と内部欠陥になります.
外部欠陥は,外ビケ,割れ,などが代表的なものです.外ビケは,アルミニウム合金など凝固収縮率の高い合金で起こりやすい現象で,方案や製品を見ることで押湯が不足しているのか,肉厚が厚いためかなど原因がわかります.割れは,割れ界面の中を観察し,デンドライトの突起があれば凝固割れ,ディンプル破面であれば,収縮割れと判断できます.どの外部欠陥においても,欠陥部を詳細に見ることで,およその原因を掴むことが出来ます.
内部欠陥は,加工で現れる場合と,X線などで観察する場合があります.加工部に現れる場合は,欠陥内部の状態を観察し,デンドライトの突起があれば引け巣,内部が平滑であればガスの巻込みであることが判別できます.X線等で観察される場合は,欠陥があるところを切断し,欠陥を直接観察することで原因を掴むことができます.判別方法は加工部と同様です.
代表的な欠陥について述べましたが,ここに出てこない欠陥も多くあります.まずは,欠陥を直接観察し,その原因を掴むことが大事であると思います.
(『鋳造工学』89巻7号掲載)
近年は生砂のCB値管理が主流になっていますが,同CB値でも水分が変わり不良への影響も変わることがあります.CB値,水分管理についてどう考えればよいでしょうか?
CB値(コンパクタビリティ)は,1970年にAFS掲載論文の中で提唱された生砂評価指標です.既存のサンドランマを使用して測定するという簡便性により日本でも広く採用されてきた経緯があります.
生砂評価指標としてのCB値への影響因子は多岐にわたると言われます.例えば,同一混練条件でのCB値と水分の比率は,微粉分(活性粘土分含む)の増減により変化します.しかし,ライン砂の組成管理をしっかりと行って,微粉分の変動を少なくするための管理が実現できていれば,CB値は水分の代用特性として単純化できるのではないでしょうか?
その場合の注意点は,CB値が混練砂粒子表面層の水分状態を現しているという点です.混練砂粒子表面の水分は非常に蒸発しやすく,混練砂粒子表面の状態は容易に変化(サラサラ化)してCB値に変化が現れます.例えば,ベルトコンベアの移し替えの際の大気との接触がそれに当たります.混練砂粒子表面の水分蒸発は混練砂水分としては0.05〜0.1%程度ですが,CB値は3〜5%変化してしまいます.
CB値測定用の混練砂サンプリングは,いつも同じ場所で,可能な限り混練機排出からの経過時間を一定にするという工夫で,このような変化は最小限にすることができます.そうすれば,CB値管理は,非常に厳密な水分管理を実施しているということに繋がります.
CB値は,摩訶不思議な指標ではありません,原理原則を常に念頭に活用してください.
(『鋳造工学』91巻6号掲載)
自硬性の砂評価はLOIが主流で,酸消費量やソーダ分等はあまり現場では使用されておりません.どのプロセスでもLOIで評価していればいいのでしょうか? 各プロセスでLOI以外の評価をした方が良い評価項目はありますか? また,プロセスによってはLOIよりもいい評価項目はあるのでしょうか?
LOI(Loss on Ignition,強熱減量)は1000℃の減量%で,有機自硬性の評価に主に用い,回収砂では残留樹脂相当です.回収砂の再生状態やガス欠陥予測ができます.加えて,粒度分布や通気度を評価すると予測精度が向上し,焼付き欠陥も予測できます.回収砂のLOIを一定にすると,鋳型強度などの特性が一定となるので,LOIは有機自硬性のどのプロセスでも重要な評価と言えます.
酸消費量はフラン鋳型の重要な評価で,硬化剤添加量を予測できます.ただし,新砂は種類により酸消費量が大きく異なりますが,回収砂は残留した樹脂や硬化剤により,酸消費量はほぼ一定となります.このため,酸消費量の現場測定が少ないと考えられます.現場での硬化剤の制御には,酸消費量よりも,砂温や湿度が影響します.
ソーダ分は水ガラス系無機自硬性で重要な評価です.しかし,pHで代用可能であり,試験が煩雑であり,あまり使用されません.
LOI,粒度分布,pH,砂温,通気度,鋳型強度,可使時間などが,現場の日常試験です.加えて,鋳物砂や粘結剤メーカに依頼し,酸消費量,化学成分,なりより性,強熱膨張量などを測定依頼することが多いと思います.
プロセスによって,例えばアルカリフェノール鋳型では,吸湿性があるのでLOIとは別に,水分を測定し,上記のメーカに依頼してのK量測定が必要となります.
(『鋳造工学』92巻2号掲載)
鋳鉄溶湯の熱分析で得られる冷却微分曲線で,凝固終了時の傾きがマイナスからプラスに転じる点の角度θが小さいほど引けにくい溶湯だという文献がありますが,この理屈が良く分かりません.どういった理由で角度θが小さいと引けにくい溶湯だと言えるのでしょうか?
θが小さいことは熱電対を挿入した部位の熱伝導率が小さいことを意味しており,熱伝導率が小さくなる原因は,ひけ巣(空洞)の存在と考えられています.なぜ冷却速度曲線(冷却微分曲線)にθが表れるのかという点からもう少し詳しく説明します.鋳物の冷却速度は主に発熱(凝固潜熱放出など)と抜熱(鋳物から鋳型への伝熱)の差で決まります.凝固や相変態が無いときの冷却速度は時間とともに遅くなります.すなわち,冷却速度曲線の傾きはプラスになります.一方,凝固中は発熱があるため発熱速度の影響を受けます.凝固末期によく見られるように発熱速度が急に小さくなると冷却速度は大きくなり,冷却速度曲線の傾きは小さくなります.共晶合金や純金属のように潜熱放出が狭い温度範囲で生じる場合はこの傾向が強く,冷却速度曲線の傾きはマイナスになるのが一般的です.以上のように凝固潜熱の放出が終わる時期に鋳物の冷却速度は大きく変化するのでθが表れます.そして,ひけ巣が発生した部位では熱伝導率が小さくなるので,冷却速度曲線の傾きは凝固末期の凝固前後で小さくなりθが大きくなると考えられています.
<参考文献> 菅野 利猛, 岩見 祐貴, 姜 一求: 鋳造工学 89 (2017) 332.
(『鋳造工学』91巻4号掲載)
よくアルミの値段はと聞くとLMEがうんぬんと話されることがありますが,LMEとはなんですか?
LMEというのは,London Metal Exchangeの略で,日本語ではロンドン金属取引所といいます.LMEはイギリスのロンドンにある世界最大規模の非鉄金属専門の取引所です.1877年に金属取引専用の施設を保有するMetal Market and Exchange Co. (MME)が設立されたのが始まりで,1882年から先物取引が開始され,1987年に設立されたLondon Metal Exchange LimitedがMMEをそのまま継承する形で所有しました.2012年には香港取引所(HKEX)に買収され,その傘下に入りました.
LMEは,銅や鉛,亜鉛,ニッケル,すず,アルミニウムなどの非鉄金属取引の世界的な中心地となっており,その取引価格を公表することにより,非鉄金属の国際価格をリードする役割を担っています.具体的には,世界のベースメタル生産者,在庫保有者,消費者,トレーダーなどを有機的に結び付けることで,ベースメタルの金属市場価格の提供だけではなく,ベースメタルの価格変動リスクに対するヘッジ機会の提供,ベースメタルの価格変動によるトレーディング機会の提供,LME公認ブランドのベースメタル保管施設の提供などの機能も担っています.LMEには「LME指定倉庫」というものがあり,現在世界の38か所に約700存在します.この倉庫の在庫変動は各地の需給を反映し,LME価格にも反映されるため,投機的な価格変動や在庫操作の動きが出てくることもあります.(iFinance 金融情報サイト HPより)
(『鋳造工学』91巻4号掲載)
凝固条件や熱処理条件がわからない場合,上部ベイナイトと下部ベイナイトの組織の違いを見分けるのに,どのような点に注意を払えばいいのですか.
鉄鋼に関する書物を読んでいると,層状(ラメラ状),羽毛状,針状,笹の葉状,ラス状,レンズ状といった言葉が飛び交う.しかし,初学者にしてみれば,本文中に掲載されているイラストや組織写真を見ても,どの部分について説明されているのか悩ましいことも多いだろう.筆者もそんな経験をした一人である.鉄鋼組織の見分け方に苦悩している人は,まずは,古書にはなるが参考文献1),2)に紹介するような金属組織写真集を芸術作品として鑑賞してみるとよい.さらにお勧めするのは,(株)山本科学工具研究社などから,鋼材の標準サンプルを入手し,実際に自分で観察してみることである.羽毛状,針状などと言ってはいるが,人によって捉え方は異なるものである.いずれにしても,優れた材料屋になるには,多くの金属を切断・研磨し,金属組織に触れ,目を肥やす努力が必要である.
さて,今回の質問にある上部ベイナイトと下部ベイナイトについてであるが,組織を見分ける上で注意を払う点の一つは観察倍率である.組織観察に用いられる顕微鏡には,光学顕微鏡(OM),走査型電子顕微鏡(SEM),透過型電子顕微鏡(TEM)などがあるが,鉄鋼材料の場合は,特にOMに属する金属顕微鏡を用いた顕鏡により組織を判別することが多い.判別に最適な観察倍率は,観察対象とする組織の大きさにもよるが,400~700倍程度が適当である.実際に,共析組成(0.8%C)の鋼材((株)山本科学工具研究社製)を用いて,上部ベイナイト(400℃保持)と下部ベイナイト(290~300℃保持)を顕鏡した結果を写真1に紹介する.
ベイナイトは,米国のEdgar Collins Bain(1891~1971)によって発見された組織である.フェライト(ベイニティックフェライト(BF)と呼ぶ)と微細な粒状セメンタイトからなる組織である(写真1(a),(b)の黒色部分.白色部分は基地(素地)のオーステナイト.等温保持後の急冷によりマルテンサイト化している).羽毛状組織のものを上部ベイナイトと呼び,針状組織のものを下部ベイナイトと呼んでいる.しかし,さらに高倍率でベイナイト組織内を観察し,BF-BF界面にセメンタイトが析出しているものを上部ベイナイト,BF粒内にセメンタイトが析出しているものを下部ベイナイトと呼ぶ別の分類方法もある3).ベイナイトについて議論する際には,どちらの分類方法を採用しているのか解釈に注意を要する.
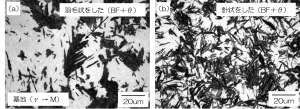
写真1 共析鋼の光学顕微鏡写真(3%ナイタールにて腐食). (a)上部ベイナイト(HRC硬さ 40~45),(b)下部ベイナイト(HRC硬さ 50~55), (BF:ベイニティックフェライト,θ:セメンタイト,γ:オーステナイト,M:マルテンサイト)
参考文献
1) 西沢泰二,佐久間健人編著,金属工学シリーズ9 金属組織写真集 鉄鋼材料編,日本金属学会
2) 佐藤知雄,鉄鋼の顕微鏡写真と解説,丸善株式会社
3) 牧正志,「鉄鋼の組織制御その原理と方法」,内田老鶴圃,ISBN:978-4-7536-5136-8,(2015)
(『鋳造工学』92巻9号掲載)
銅合金溶湯中の水素量を鋳込み前に知ることはできますか?
一般の銅合金鋳物の鋳造において,銅合金の中でも黄銅など亜鉛の多く含まれている合金では,溶解中の亜鉛の蒸発による脱ガス効果があり水素は問題になることは少ないです.また,青銅や純銅においてはフラックスやガスバブリングによる操業条件でガス欠陥をコントロールしているところが多いと思います.
炉前試験としてはチル試験を行い破面の水素ガス由来の気泡の観察,チル試験片上面の膨らみ具合からガスの量を推定する方法が行われてきました.機器分析としては,不活性ガス中で1g程度の試料を溶融させ,その再発生する酸素・窒素・水素ガスを分析する手法(LECO社)があり,0.1ppm程度の精度(下限値)で分析でき,電線などの伸銅品の溶解時に使用されています.近年では,溶湯中にセラミックスのセンサーを浸漬して起電力を測定することにより水素を分析する手法が開発実用化(TYK社)されています.
(『鋳造工学』92巻5号掲載)
電気炉には高周波,中周波,低周波誘導炉が存在しますが,それぞれの特徴やメリットデメリットは何でしょうか.
高周波・中周波・低周波の違いを考える時に最も基本となるのは,溶湯撹拌力(F)が周波数(f)に反比例するということです.したがって,低周波誘導炉(50/60Hz)は溶湯撹拌力が大きいという特徴を有しています.
低周波炉は設備費が低価であり,残湯を残しながら,同じ材質をくり返し作る連続操業の量産ラインに適しています.ただし,高周波誘導炉と比較して電流密度が低いため,溶解に時間を要し,溶解電力原単位も悪いという問題があります.一方で,低周波炉は撹拌力が大きいため,カーボンや合金の添加が容易なメリットや亜鉛や鉛などの不純物の除去が進みやすいメリットがあります.しかし反対に,溶湯が酸化しやすいというデメリットがあります.
一方,中・高周波誘導炉(300~3000 Hz以上)は,撹拌力は小さいですが,電流密度を大きくすることができるために,高速溶解が可能で,電力源単位も低周波炉よりは良くなります.また,低周波炉のような溶解スタート時のスターティングブロックなども必要なく,溶解材料も自由に選べるというメリットがあります.また,撹拌が無いことから,溶湯の酸化が少ないメリットや,全量出銑であるため成分の異なる各種材質の溶解が可能というメリットもあります.しかしながら,撹拌力がないためにカーボンや合金の添加が難しく,一度取鍋に出して各種元素を添加しなければならいことも多いです.最近では,不純物元素の除去の問題を解決するため,高さを低くして炉径を大きくした偏平炉なども用いられています.中高周波炉では小さな溶解材料が使えるメリットはありますが,材料がブリッジをつくる現象である棚吊りが起りやすく,冷却水が溶湯に触れることによる電気炉の爆発事故を起しやすいので注意を要します.
最近では,低周波炉と高周波炉のメリットを取り入れた中周波炉を用いる鋳物メーカーも増えてきています.
(『鋳造工学』93巻1号掲載)
アルミニウム合金を鋳造する際に,フラックス添加やアルゴンガスによる溶湯処理がよく行われていますが,どのような原理で介在物等が除去されているのでしょうか.
合金地金や返り材などの原料を溶解するとアルミニウム合金溶湯が得られ鋳物にすることができます.ただしこのまま流し込むと,アルミニウム合金成分だけではなく,地金や返り材の表面や内部にあった酸化皮膜やその他の異物も一緒に溶湯中に漂った状態で存在しているので,製品品質に悪影響を及ぼす介在物欠陥となってしまいます.また溶湯の中には,大気中の水分が溶湯と反応して入り込む水素や,溶解に使用した燃料の燃焼により発生した水分から入り込む水素が溶け込んでいますので,何もしないと鋳物が凝固するときにこの水素が気泡を形成してガス欠陥となります.品質の良い鋳物を製造するには,このような欠陥の発生を徹底的に防ぐ必要があり,ご質問のような溶湯処理が行われます.
鋳造する前に溶湯中にアルゴンガスや純度の高い窒素ガス等を微細分散させて吹き込むと,小さな泡の表面に介在物などの異物が吸着され溶湯表面に浮上分離します.また,この泡は水素を溶け込ませて大気中に放出してくれます.一方フラックスは,単独でも溶湯と介在物の間に入り分離を促進してくれますが,溶湯中を浮上するガス気泡がある場合にはその表面を活性化させて介在物をあつめ,介在物の分離・除去を促進してくれます.このようにフラックス処理,ガス吹込み処理のそれぞれ単独でも効果はありますが,両方を同時に行う作業が非常に有効です.
(『鋳造工学』92巻5号掲載)
フェライト基地を腐食すると結晶粒界がはっきり見えますが,パーライト基地では粒界が見えづらいのはなぜですか? パーライトは、隣接するセルが融合しているのですか?
片状黒鉛鋳鉄の凝固過程では,共晶凝固が完了するとオーステナイトと黒鉛の混在組織となり,やがて共析変態温度に達するとオーステナイトはパーライトに変態し,常温では片状黒鉛とパーライト基地で構成された組織になります.初晶オーステナイトと共晶セル中のオーステナイトは,どちらも共析変態温度に達するとパーライトに変態するので,結晶粒界がはっきり見えなくなります.
参考文献:中江秀雄監修:鋳物技術者と機械設計技術者のための新版鋳鉄の材質,日本鋳造工学会(2014)P15
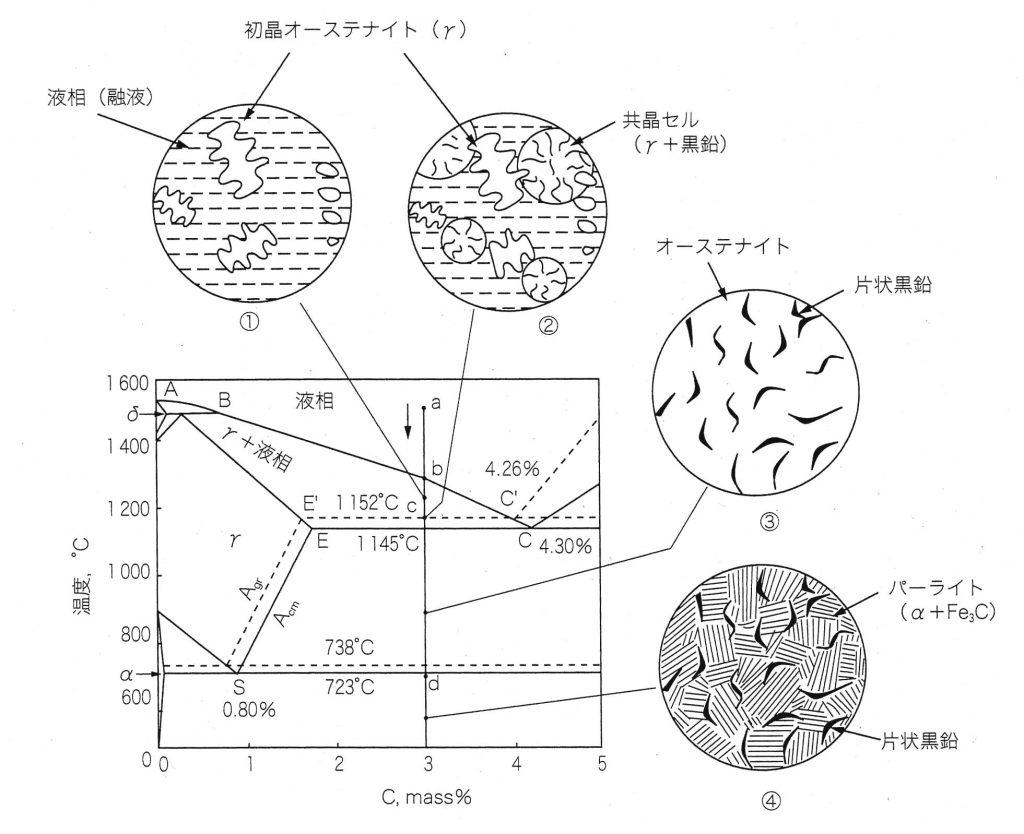
Fe-C系平衡状態図と片状黒鉛鋳鉄の凝固過程(模式図)
(『鋳造工学』93巻1号掲載)
FCD材の疲労試験において,回転曲げと平面曲げの疲労限度はほぼ同じ値でしょうか?もし,異なるのであればどちらの値が高く示し,それはなぜでしょうか?
回転曲げ疲労試験とは,一定の曲げモーメントを作用させた丸棒を回転させ,試験片平行部の表面に繰返し,曲げ応力を負荷させる疲労試験です.また,平面曲げ疲労試験とは,平板試験片に繰返し曲げ応力を負荷する疲労試験のことです.どちらの疲労試験も一般的によく行われますが,試験機の特性から試験片の形状が異なります.回転曲げ疲労試験は平行部を有するもしくは砂時計型の丸棒形状であるのに対して,平面曲げ疲労試験は板材です.
いずれの試験も引張−圧縮による応力比-1の両振りの疲労試験ですので,平均応力は0であり,負荷応力が応力振幅となり,理論上,疲労限度は等しくなります.しかし,FCDなどの鋳造材では,疲労限度に及ぼす影響因子は,以下の様な要因が考えられますので,実際の試験結果では,疲労限度に違いが見られる場合もあります.
(1)試験片の危険体積の影響
危険体積とは,試験片中の繰り返し最大荷重,最小荷重が負荷される部分のことです.疲労き裂は危険体積中に存在する最大の欠陥(引け巣など)から発生すると言われております.すなわち,危険体積が大きくなれば,寸法の大きい欠陥の存在する確率は高くなり,疲労限度は小さくなることが予想されます.
(2)表面粗さの影響
疲労試験は試験片の表面粗さ,すなわち表面の凹凸が,応力集中により,破壊起点となります.鏡面仕上げにすると疲労限度は向上します.
(3)残留応力の影響
疲労き裂進展のメカニズムは,引張・圧縮応力によるき裂開閉口の繰返しであり,外力以外の残留応力にも影響します.一般にショットピーニングの様な試験片表面に圧縮残留応力を付与して,疲労限度を大幅に向上させる方法が知られていますが,このような表面改質処理をしなくても,試験片加工や熱処理によって残留応力が発生し,それらが疲労限度に影響を及ぼすことがあります.
(『鋳造工学』88巻6号)
アルミニウム合金シリンダブロックでは,FCライナーを使うのが通常の設計ですが,アルミニウム合金だけで造れないでしょうか.
シリンダブロックでは,シリンダの中をピストンが動くため,その表面(ボア表面)には耐摩耗性が必要となります.そのために,アルミニウム合金シリンダブロックでは耐摩耗性の高い鋳鉄のライナー(FCライナー)を用いるのが一般的です.
しかし,軽量化と冷却能の向上のため,ライナーを用いないブロックが開発されてきました.アルミニウム合金を使ったものでは,ADC14合金のような過共晶Al-Si合金を用いるものがあります.硬い初晶Siの晶出により耐摩耗性を持たせたものです.
この合金は,初晶Siの大きさと分布のコントロールが難しいこと,機械加工性が悪くコストアップとなることなどがあり,現在では使われていません.また,過共晶Al-Si合金ライナーを用いたり,Ni系のめっきをしたりする方法もありますが,いろいろな課題があり適用例は多くありません.
最近では,従来のアルミニウム合金シリンダブロックのボア表面にライナーの代わりに鉄系の材料を溶射する技術が適用されてきています.溶射層の厚さは,0.2mm程度であり,ほとんどオールアルミニウム合金製といってもいいくらいの機能になっています.
(『鋳造工学』88巻6号)
アルミニウム合金ダイカストで溶湯が金型と接触するとすぐに凝固すると思いますが,そのあとはどうなるのでしょうか?
金型内の溶湯の動きを直接見ることは簡単ではないので,お答えするのは難しいと思いますが,これまで様々な実験や見解が出されていますのでそれに沿って簡単にご説明したいと思います.
まず,溶湯が金型キャビティに射出されて金型と接触した時点で当然ながら溶湯の熱は急速に金型に伝達され,温度が低下します.その場に溶湯が留まり,十分に冷却されればご指摘のようにそのまま凝固すると思います.しかし,金型とある程度の角度を持って高速で衝突すると溶湯は慣性力によって金型から離れることが考えられます.日産自動車の神戸氏が直接観察をした結果((一社)日本ダイカスト協会編:「ダイカストにおける溶湯射出挙動」(1999))を詳細に観察すると,図1のように溶湯が跳ね返っているのがわかります.これは,ゲートから流出した溶湯が約40°の角度で可動金型に衝突して,金型キャビティが広い(肉厚で考えると厚い)ために(c),(d)に見られるようにその一部が跳ね返る現象であると考えられます.
また,トヨタ自動車の古川氏(古川:型技術29,3(2014)24)は,金型表面にカーボンナノファイバーとフラーレンC60の被膜を形成することで,金型キャビティに流入した溶湯が金型に付着しにくくする(凝固しにくくする)ことで,剥離(あるいはめくれ)などの不良を低減できることを報告しています.
もし,その場に留まって凝固するとチル層を形成することになります.しかし,その一部は後続の溶湯が接触した時点で,その熱で再溶解してしまうことも考えられます.鈴木氏ら(鈴木,古本,坂本:軽金属,21(1971)379)は,チル層の形成について検討し,肉厚が薄くてゲート速度がやや遅いときに,溶湯は金型に接した部分で凝固するが一部が再溶解される可能性を示しています.
このように,金型キャビティの中ではいろいろな現象が起きていると考えられます.
図1 ゲートからの溶湯の流出挙動
(『鋳造工学』89巻3号)
ダイカスト金型を設計する上で考慮しなければならない重要なことはなんで しょうか
ダイカストにおける設計工程には,大きく分けて製品設計と金型設計の二つがあります.
製品設計は,客先の製品形状をダイカストで生産できるような形状に図面化することが目的です.型分割・スライド中子・入子(埋子)・鋳抜きピンなどの設置,ゲート・押しピンなどの位置・大きさなどの型構成に関する項目と,肉厚・角部R(フィレット)・抜き勾配・鋳抜き穴・リブ・フィンなどの大きさの設定,鋳肌・塗装・メッキなどの製品表面処理などの製品形状に関する項目とを客先と相談しながら決定・図面化する工程です.
金型設計は製品設計で決定した型構成,製品形状を基にダイカスト生産する金型を製作するために必要な金型の構造・機構などを図面化することが目的です.潜在的なダイカスト内部欠陥を抑制するためのCAE解析,製品の取出しから常温に冷える間での縮み代(熱収縮量)の設定,ゲート・ランナー・オーバーフロー・エアベント(ガス抜き)などの湯口方案の設定,鋳造圧力での金型変形を防止する型剛性,金型温度管理する内部冷却穴の配置,金型表面処理方法などを具体的に決定・図面化する工程です.品質,生産性,コストへの影響が大きく,製品要求機能,品質安定維持性,鋳造条件,耐久性,金型製作コスト・作りやすさ,メンテナンス性なども十分に考慮した設計にする必要があります.
金型の機能は,形状・寸法付与機能と熱交換機能の二つであるので,1)製品の寸法精度とその維持のための金型故障の防止や型寿命延長,2)内部冷却設計による品質(焼付き,ひけ巣,割れなど)の安定と維持に関係するものが,金型を設計する上で特に重要です.
(『鋳造工学』89巻4号掲載)
Fe-C系状態図で黒鉛の晶出量を求めると数%ですが,顕微鏡組織から判定すると10~15%に見え,文献にもそう書かれています.この違いはなんですか?
Fe-C系状態図における黒鉛晶出量は,重量%で表示されています.一方,顕微鏡組織における黒鉛晶出量は体積%もしくは面積%で表示されています.よって,状態図の重量と顕微鏡組織での黒鉛体積%の間には,近似式で計算すると,式(1)~式(3)の関係が成り立ちます.すなわち,顕微鏡組織で見られる黒鉛の体積率%は,状態図での黒鉛晶出量の3.5倍の値になります.
黒鉛の密度(g/cm3)=黒鉛の重量(g)/黒鉛の体積(cm3) 式(1)
(黒鉛の体積/鉄の体積) =(鉄の密度/黒鉛の密度)×(黒鉛の重量/鉄の重量) 式(2)
黒鉛体積率% ≒ (7.87/2.25)×黒鉛の重量比%
≒ 3.5×黒鉛の重量比% 式(3)
参考のために,図1と表1に,温度低下に伴う黒鉛晶出量の変化を示します.共晶温度付近での黒鉛晶出量は2%程度で,常温になると4%程度になります.これを3.5倍した値を,表の下に示しております.黒鉛面積率は10~15%になっており,質問通りになっています.
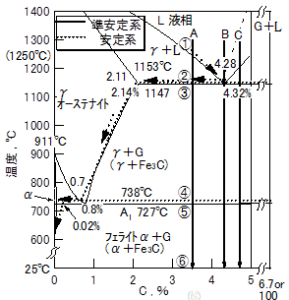
図1 温度低下に伴う相成の変化
参考文献:菅野利猛:鋳造工学,Vol.85(2013)P708-718
(『鋳造工学』91巻9号掲載)
減圧凝固試料の見方は?
包晶のイメージについて教えてください
包晶は,高融点と低融点の金属を組み合わせた合金でよく現れます.Fe-C系のδ相とγ相の反応,銅合金のCu-Sn系,Cu-Zn系で見られます.図1に示すような状態図を包晶系状態図といいます.EーFの線の包晶温度T2では,液相はα相,β相と平衡であり,L+α→βという包晶反応が起こることを示しています.固相内での溶質拡散が速く,平衡状態図に従う場合には,xの組成の合金でこの反応が進めば,図2(a)の状態から,液相の減少とともに,β相がα相に変換して(図2(b))包晶温度以下ではβ相の単相になります.(図2(c))
実際にはこの反応が進むには固相内の拡散が必要ですので,反応は遅く,通常の凝固速度では,x組成の場合でも,α相が晶出した後(図2(a)),β相が晶出し(図2(d)),α相の廻りをβ相が包み込むような2相の凝固組織(図2(e))になることも多いです.
図2 包晶系合金の凝固組織形成
(『鋳造工学』89巻4号掲載)
現場的にBa-Ca-Si系二次(注湯流用)接種剤を多めに使用すると,チャンキー黒鉛が生じやすくなるのは何故でしょうか? また,同一鋳物部位においてチャンキー黒鉛が出やすくなるとその部位には引けが小さくなる傾向があるが,それはなぜでしょうか?
ご質問の内容には,鋳物のサイズ,化学組成など具体性が無いので一概に言えませんが,チャンキー黒鉛と言ってよいかどうか分かりません.Ba-Ca-Si系接種剤は、その化学組成からするとFe70Siに比べて溶湯に融け込みづらいものです。更に「多めに使用」しているのでその傾向は助長されます。したがってこの黒鉛は、接種剤が完全に融け込めずに,溶湯中に高Si(高CE)域が出来、その部分に発生した黒鉛とも考えられます.右図に注湯流接種剤の融け込み不良で生じた顕微鏡組織(FCD400相当の15kg程度の鋳物の加工面)を示しました。取鍋接種用接種剤に比べて注湯流接種には、融け込み、添加量など多くの注意点が必要です.取鍋接種で効果のある接種剤が,注湯流接種でも良いとは限りません.
次に、同じ鋳物部品で、チャンキー黒鉛が発生したものの引けが小さくなっているとのことなのですね。これらの関係についての文献は見つかりませんが、接種剤添加量を増やしているのでSi分と黒鉛粒増加により凝固形態が変化したためと考えられます.球状化処理や接種などの炉前での溶湯処理でSi分が増えるとチャンキー黒鉛が発生しやすくなり、内引け巣は,鋳型壁の移動が無ければ晶出黒鉛の量が多くなると小さくなる傾向があります。さらに,鋳造条件(肉厚,化学成分,鋳型など),溶解材料,溶解方法,溶湯処理などによっても発生状況が変わります.
「鋳造工学」第76巻2月号(2004)掲載の「球状黒鉛鋳鉄の異常黒鉛とその対策」を参考にしてください.日本鋳造工学会ホームページ:https://www.jstage.jst.go.jp、巻,号,「チャンキー黒鉛」で文献検索できます.(『鋳造工学』第88巻第3号掲載)
生型砂の混練機は,マラーホイール式とアジテーター式がありますが,どのような観点から選定を行えばよいでしょうか?
生砂の混錬工程のポイントは,ライン内を循環している生砂粒子表面に活性ベントナイトを均一に引き延ばしながらコーティングすること,そして活性ベントナイトの結晶層間に水を十分浸透させ,ベントナイトの粘結力を最大限引き出すことにあると考えられます.マラーホイール式は,一対の垂直保持されたローラーで混錬砂を踏みつけながら混錬を行います.ローラーで単純に踏みつけているのではなく,内輪差でローラー面は砂に対して滑り運動しています.へら押しのイメージで大きな剪断力を混錬砂に与えているといえます.一方,アジテーター式では,回転主軸に角状の撹拌子が多数取り付けられたアジテーターが混錬砂の中で高速回転して非常に強い攪拌をします.活性ベントナイトを細かく砕きながら砂粒子表面に均一に付着させると同時に,ミクロ的に大きな剪断力を与えてベントナイトの膨潤を促進していると考えられます.ベントナイトの特性を活かすという面では,マラーホイール式に優位性があると考えられますが,短時間で大エネルギーを混錬砂に与えるアジテーター式は,単位装置当たりの処理量が多く確保できるというメリットがあります.混錬機構には差があるということを理解した上で,工場毎の設備事情を勘案して選定することが大切だと言えます.
(『鋳造工学』92巻7号掲載)
ダイカストについて初心者なのですが,ダイカストのオーバーフローについて,役割は理解したのですが仕組みがよく分かりません.なぜ金型に空間を設けることで,ガスや酸化物,介在物を排出できるようになるのでしょうか.そのメカニズムを教えて頂きたいです.
オーバフローの役割にガスや酸化物,介在物を排出すると教科書等に記載されていますが,実際のところは,①ガス抜きや溶湯合流部にオーバフローを設置してガスのトラップによる湯じわを無くすこと,②金型温度が冷えることで起きる離型剤の乾燥不足による水残りや充填不良を無くすこと,③製品部に押出座が設置できない場合の押し出し座として使われています.小さい製品では,湯先の酸化物などを排出する効果も期待できます.
この場合は,溶湯が最後に充填される位置にオーバフローを設置することが大切で,最後に流れてきた汚れた溶湯をオーバフローに排出することで実現できます.
いずれの場合もオーバフローの設置位置が重要です.
日本鋳造工学会HPのQ&A事例サイトも参考にしてください.
Q&A事例(2)非鉄 https://jfs.or.jp/q_a/qa_hitetsu/
・HPDCにてオーバーフローを設計する際の考え方はありますか?
・「アルミニウム合金ダイカストで,ゲート断面積やオーバーフロー断面積の厚みと幅で理想的な比率はあるのでしょうか?
(『鋳造工学』91巻2号掲載)
3Dプリンター積層造形法に用いられるアルミニウム合金にはどのような種類がありますか.また,一般の鋳造合金と異なる点はありますか.
積層造形法では, 2次元スライスデータに基づいて金属粉末にビームが照射されます.局部溶解・瞬間凝固と粉末供給が繰り返されることで,3次元の複雑な製品が形成されます.積層造形法では1000℃/s以上の冷却速度を示すので,微細な化合物や過飽和固溶体が生成されるという組織の特徴があります.
現状は,チタン系合金やニッケル系合金では既存材料と同等の合金粉末材料が使用されています. アルミニウム合金も同様で,ダイカスト合金と類似したAl-10%Si-0.4Mg合金が多く使用されています.ただこの合金の場合,積層中の残留応力を低減するために,基盤プレートを200℃に加熱しながら造形することで,過時効になって約300MPaの引張強さになります.これに対して,T5処理によって約500MPaの高強度を示すScalmalloy合金(Al-4.5%Mg-0.7%Sc系)が最近欧米において報告されています. 日本国内においては, 約450MPの高強度を示すAl-7%Si-0.7%Mg-1.5%Mn系合金や実用合金の1.5倍の高温強度を示すAC8A+2%Fe合金が注目されています1).
【参考文献】
1)安達充,小岩井修二:鋳造工学91(2019)60
(『鋳造工学』92巻7号掲載)
鋳物砂の再生に寿命はありますか? 不純物(生型であればオーリティック,自硬性であれば樹脂)が再生されていれば新砂と同等と考えてよいですか?
「再生の寿命」の質問:鋳物砂(天然けい砂や人工砂など)に粘結剤などを加えて,造型可能な生型砂や自硬性鋳型砂とし,これらの鋳造後の回収砂を再生します.再生工程では,回収砂に対しての歩留りがあり,これが寿命に相当すると言えます.歩留りに対応した減少量に対して,鋳物砂を加えて繰り返し使用します.一般に,歩留りは,生型砂の再生(流動焙焼と機械再生)では70%~85%です.自硬性鋳型砂では機械再生のみで80%~98%です.どの様な純度の天然けい砂を使用しているか,破砕されにくい人工砂を使用しているかなどにより歩留りが変わります.また,自硬性鋳型砂では,アルカリフェノール鋳型砂は歩留りが悪くなります.
「不純物除去の再生」の質問:強熱減量,粒度構成,微粉量,粒形,耐火度,強度阻害物質量などが,再生の管理項目です.生型のオーリティックは除去が望ましく,自硬性では管理値の強熱減量までに樹脂を除去することが望ましく.ただし,アルカリフェノール鋳型は,回収砂中のアルカリ金属を硬化が阻害されないレベルとするために,フラン鋳型などと異なり,強熱減量を0.8%以下に強力に再生する必要があります.正しく再生された再生砂は,低膨張で鋳型強度が発現しやすいなど,新砂相当あるいはそれ以上の品質の鋳物砂となります.
(『鋳造工学』91巻2号掲載)
凝固条件や熱処理条件がわからない場合,マルテンサイトとソルバイトの組織の違いを見分けるのに,どのような点に注意を払えばいいのですか.
前号に続き,組織の違いについての質問である。マルテンサイトとソルバイトについても,金属顕微鏡を用いて400~700倍程度の倍率で観察するとよい。実際に,共析組成(0.8%C)の鋼材((株)山本科学工具研究社製)を用いて,マルテンサイト(850℃からの水焼入れ)とソルバイト(マルテンサイトの580℃焼戻し組織)を顕鏡した結果を写真1に紹介する.
マルテンサイトは,1891年にドイツの冶金学者Adolf Martens(1850~1914)によって発見された組織である.体心立方格子(bcc)であるオーステナイト(γ)が,焼入れにより体心正方格子(bct)に無拡散変態したもので,侵入型の炭素原子が過飽和に固溶している.共析鋼のマルテンサイトは,写真1(a)のように微細な笹の葉状(針状ともいう)のものがランダムな向きにある組織であり,内部には多量の転位または双晶を生じている.マルテンサイトについては,この他にも種々の様相のものがあり,代表的なものとしてラス状やレンズ状の組織がある.ラスとは,木摺り(きずり)という意味であり,簀の子(すのこ)をイメージするとわかりやすい.ラス状の組織は,低炭素鋼(<0.5%C)やFe-Ni合金(<20%Ni)の鋼で観察される.レンズ状の組織は,粗大な笹の葉状を有しており,高炭素鋼(>1.0%C)やFe-Ni合金(>28%Ni)などの鋼で観察される.なお,マルテンサイトについては,ベイナイトやソルバイトに比べて腐食しにくく,顕鏡のためのエッチング処理に時間を要する(腐食液の鮮度にもよるが,3%ナイタールで14~16秒程度).
ソルバイトは,マルテンサイトを約500~600℃で焼戻して得られるフェライトと粒状セメンタイトの混合組織である.写真1(b)中において,黒色部分がマルテンサイトの分解によりフェライトに変わった基地(素地)であり,無数の白い粒状の点がセメンタイトである.ソルバイトは,マルテンサイトと組織がよく似ており,写真のみから違いを判別するのは難しい.ソルバイトよりもさらに低温の約400℃でマルテンサイトを焼戻して得られるトルースタイト組織は,セメンタイトの凝集がソルバイト程に顕著ではなく,さらに違いの判別に困難を極める.これらの組織については,硬さや腐食性などの他の物性と併せた総合的な判断が必要である.XRDやTEMを用いて,c軸方向の格子定数を測定・比較するのもよい。
質問に対して頓珍漢な回答かもしれないが,材料を作製した人と連絡が取れるのであれば,組成に加えて,凝固・熱処理条件をしっかりと聞くに越したことはない.いいものが完成し組織と組成がわかっても,凝固・熱処理条件などの作り方がわからないと,ダマスカス鋼の製法ように失われた技術になってしまうのだ.
写真1 共析鋼の光学顕微鏡写真(3%ナイタールにて腐食).
(a)マルテンサイト(HRC硬さ 64),(b)ソルバイト(HRC硬さ 30~40).
(M:マルテンサイト,θ:セメンタイト,α:フェライト)
(『鋳造工学』92巻10号掲載)
薄肉のダイカスト品を作ろうと思います。薄肉品の湯道設計で何に注意して設計すればよろしいのでしょうか?
ダイカストの肉厚は,合金種や製品の大きさにもよりますがADC12の大物では2~6mm,小物では0.8~3mmといわれています.さらに薄肉化をすると湯じわ,湯境,未充填などの湯流れ欠陥を発生しやすくなります.これらの欠陥は,流動過程中の溶湯温度の低下による固相率の増加,キャビティ内の空気の圧縮による背圧などによって発生します.これらを防止するためには,(1)溶湯温度が凝固開始する前に充填を完了させる,(2)キャビティ内の空気をできる限り排気する,ことが大切です.
(1)に関しては,許容充填時間以内に充填を完了させる必要があります.許容充填時間は様々な計算式が提案されていますが,最も簡単な式はG.Ulmerの式でt=0.033x2(t:充填時間,x:肉厚)を用いて計算します.充填時間を短くするためには,プランジャーチップ径を大きくしたり,射出速度を速く設定したりしますが,ゲートを変更せずに速度を上げるとゲート速度も速くなり,金型損傷を招くので,ゲート断面積はできる限り大きく設定し,ゲート速度を抑えます.また,ファンゲートやオーストラリアンゲートなどを採用するとスムーズに溶湯を充填できます.ランナーは急激な流れ方向の変化は避けてスムーズに溶湯が流れるようにし,さらにゲートに向かって徐々に断面積を減少する増速型にするとよいでしょう.また,ランナーの厚さと幅の比は1:4以上がよいといわれています.
(2)に関してはチルベントなどを用いてエアベントの断面積を広くとります.また,真空吸引すると効果的です.
その他,オーバーフローは金型の保温のため,小さなものを多くつけます.しかし,トータルの体積が大きすぎると充填完了後の昇圧が遅れるので注意しなければなりません.
部品を設計する時に直接使われない破断応力の引張強さや破断伸びの用途は何か教えてください
設計者あるいはメーカーによって鋳造部品の設計に関する考え方が違うので,これが正解ということは言えないと思いますが,一般的には下記のように考えられます.
一般に構造部品は,通常の使用において耐力以上の応力が入らないように設計します.耐力以上の応力が入ると塑性変形を起こして,部品として成立しなくなるためです.さらに,適用部位により,疲労強度S-N線図,マイナー則,疲労限度線図などを用いて構造設計します.
では何故,破断応力の引張強さや破断伸びのデータが必要なことがあるのかというと,設計思想が異なるので一概には言えません.例えば,部品によっては過大入力が入った時に,その部品にエネルギーを吸収させたいのか,曲げたいのか,折れてほしいのかといったいろいろな要求が出てきます.これらの要求に答えるために,破断応力の引張強さや破断伸びの値が設計時の参考値として使われます.自動車のサスペンション部品やボディ部品などでは,いろいろな入力が入る可能性があるので,このような材料特性も考慮しながら設計することになります.
鋳造シミュレーションの精度はどの程度でしょうか? 特に生産前はなかなかシミュレーションで予測することが難しいのですが,世の中のレベルはどの程度なのですか?
鋳造シミュレーションでは,予測すべき現象が,湯流れ,伝熱,凝固にまたがり,欠陥予測に関しても湯流れ,伝熱・凝固,溶湯成分,不純物,介在物などに起因するもの,またその位置や大きさなど様々あり,一概に精度を論ずるのは困難です.
少し古いデータですが,鋳造CAE研究部会報告書「研報105 鋳造CAEの活用と品質向上に関する研究」のアンケート結果によれば,2006年頃の鋳造CAEに対する不満は,1位「予測精度」29%,2位「欠陥判定基準値」26%です.その前の2001年と比較してその割合は変化がありませんでした.10年ほど経過した2018年現在でも,この割合はほとんど変わっていないでしょう.しかし,鋳造CAEが進化していないのではありません.コンピュータ能力の向上に伴い,欠陥予測手法の追加や改善,自由表面移動解析の精度向上,背圧や表面張力の考慮など,性能&精度は数値計算的には飛躍的に向上しました.一方で,鋳物の薄肉化に伴い最小肉厚が数mmと薄くなり,またCTスキャンで内部欠陥を定量的に直接観察できるようになるなど,CAEソフトに対する要求も厳しくなっています.
では,生産準備段階でのシミュレーションはどうでしょうか.こちらも正確なデータは見つかりませんが,生産準備段階ではユーザによって使用方法が大きく異なります.鋳物姿勢(天地)の確認,湯口位置の決定といった,限定した分野に使用しているユーザは,それなりに活用できているようです.一方で,最終性状(ひけ巣,巻き込み,変形など)の位置や大きさの予測などを検討しているユーザは,従来知見(材料データや方案データなど)が準用できるところはまだしも,少し離れると難しいようです.現時点では使い方次第といったところではないかと考えます.
(『鋳造工学』90巻2号掲載)
ダイカストの破断チル層は重大な欠陥となりますが,合金系によりできやすかったりできにくかったりするようです.どうしてなのですか?
破断チル層は,射出スリーブ壁で冷やされた溶湯が凝固し,晶出した凝固層が射出により金型内に巻き込まれ製品内に入ったものです.射出スリーブ壁に沿った凝固層であるため,製品内で直線状または曲線状の界面を有す組織になります.
ダイカストで使用されるADC12合金は,けい素量が9.6~12.0%とほぼAl-Si2元系合金の共晶点である12.6%に近く,凝固形態が表皮形成型になります.この場合,射出スリーブ内で凝固前線の界面がほぼ完全凝固して進行するため,強固な凝固層が出来,射出によって塊状の破断チル層になります.
けい素量7.5~9.5%のADC10合金やさらにけい素量を低くした合金では凝固温度範囲が広がり,デンドライトが成長した組織になります.一般的にこのような凝固形態をかゆ状凝固と言います.この場合,射出スリーブ内で冷やされた溶湯は射出スリーブ中心に向かって固相率が小さくなるように凝固し,凝固前線界面は液相も含んだ凝固領域の少ない状態になります.この状態で射出した場合,比較的容易にばらばらになるため,線状や曲線状の界面を有さない組織が多数を占めることになります.それゆえ,製品内での破断チル層が少なくなります.
(『鋳造工学』90巻2号掲載)
接種は本当に黒鉛化を促進するのでしょうか?
Fe-G系凝固(共晶Fe3C:チルが無い)した鋳鉄の黒鉛量は,おおよそ凝固時の晶出量(Fe-C二元複平衡状態図のE´点)とその後の共析変態完了時までの析出量の和になります.接種は,基地組織(フェライト/パーライト率)にも影響を与えるので,鋳放しでの基地組織がフェライトならば黒鉛量が多く,パーライトなら少なくなります.従って,同じ化学組成ならば,パーライトが多い程,高い密度になるでしょう.残念ながら接種と鋳鉄の密度変化をテーマにした研究論文は見つけられませんでした.岩淵らの鋳鉄の成長に関する研究報告1)に鋳鉄の密度の測定方法や理論的考察などを参考されては如何でしょう.
質問は,画像解析結果から接種による黒鉛化を黒鉛面積率・体積率で評価し,密度の算出,それに伴う機械的性質(引張強さ)に関する疑問となっています.結果は結果として画像解析では,試料の研磨状態,顕微鏡(倍率や照度性能),画像解析装置(画素数,二値化条件,n数の検討など)などが結果に影響を及ぼすと考えて下さい.黒鉛形態の他に腐食して基地組織のフェライト/パーライト率についても確かめられると良いでしょう.ところで,硬さと強度との関係が書かれた文献はあるが,密度と強度との関係についての文献・論文などあればお知らせください.
次に接種本来の目的は,Fe-Fe3C系凝固をする一般的な鋳鉄をFe-G系凝固させ,共晶セメンタイト(チル)の発生を防止することです.このチル(共晶Fe3C)防止機構について黒鉛化,黒鉛形態,微細化,肉厚感度の低減などのミクロ組織変化とそれに伴う機械的性質への影響については多くの文献がありますのでWeb上のJ-Stageで検索されると良いでしょう.一例として,なぜ「チルが消えるのか?」,「黒鉛形態が変化するのか?」,「微細化するのか?」などについてかかれた解説2)がありますので参考にして下さい.
1)岩淵義孝、小林勲:鋳造工学70(1998)806
2)井川克也;日本金属学会会報,3(1964)477 https://doi.org/10.2320/materia1962.3.477
(『鋳造工学』91巻7号掲載)
海外の高級車では,アルミボディ部品が使われているとよく聞きます.どんな工法でどんな材料が使われていますか?
オールアルミニウム合金のボディ構造を持つ乗用車を世界で初めて量産したのは,ドイツのアウディ社で,1994年に発売されたAudi A8です.このボディ構造は,アルミニウム合金の板材や押出材の部品をアルミニウム合金鋳物やダイカストの継手を用いてつなぐ構造でした.その後,アルミニウム合金ダイカスト部品が大型化してきて,日本のメーカーも含めていろいろな会社が採用し始めました.最近では,ボディ構造がマルチマテリアルとなってきましたが,ダイカスト部品が適用されています.
ボディに適用される部品には,適度な耐力と伸びが必要になります.また,元々鋼板で作られている部品ですから,薄肉であることが要求されます.このような要求特性を満足するため,Al-10%Si-0.3%Mg合金を代表とする合金を高真空ダイカスト法を用いて鋳造し,熱処理することにより機械的性質を調整して適用しています.この材料と工法の組み合わせは,サスペンションメンバーなどの部品にも適用されています.近年,製造コストを低減するため,熱処理をしない材料の開発が進められ,Al-Mg-Si系の材料が適用されてきています.今後,このような新しい材料が数多く出てくることが期待されます.
(『鋳造工学』91巻7号掲載)
鋳鉄とAl-Si合金ともに共晶凝固しますが,凝固速度が大きな時,共晶凝固するのでしょうか.また,その時の常温での顕微鏡組織はどのようになっているのか教えてください.
鋳鉄については,球状黒鉛鋳鉄として晶出する場合を除いて回答いたします.教科書では,共晶合金の凝固は,液体から二つ以上の固相が同時に晶出すると習っていると思います.片状黒鉛鋳鉄の共晶凝固の場合,過冷却が小さく,ゆっくり凝固するような条件では,オーステナイトと黒鉛が晶出します.この時,液相からオーステナイトと黒鉛が晶出する速度はほとんど同じで同時に晶出すると考えて良いでしょう.A型黒鉛と称している組織は,この状態で形成されます.また,黒鉛凝固では黒鉛の粗さ,すなわち黒鉛相の間隔は,溶湯中のCの拡散距離(局部凝固時間)に支配されると考えられています.一般に,凝固速度が大きくなる(またはその場所での凝固時間が短くなる,あるいは凝固時の過冷が大になる)と,黒鉛間隔は狭くならざるを得ず,黒鉛が微細化します.凝固速度が増大すると黒鉛はA型の形態を取り得なくなり,枝分れを繰り返していわゆるD型(過冷黒鉛とも呼ばれている)になります.さらに凝固速度が大きくなると,別の凝固形態(セメンタイト化)を取らざるを得なくなります.これは溶湯中のC原子が黒鉛まで拡散する時間が無く,黒鉛化が凝固の進行に間に合わなくなるためです.つまり,黒鉛化が不可能になり,C原子がFe3C(セメンタイト)の形態を取ことになります.凝固速度が大きくなると,準安定系のFe-Fe3C共晶が起こり,レデブライト組織(オーステナイトとセメンタイトの共晶組織)となります.
Al-Si共晶合金の場合,αアルミニウム固溶体は金属相,シリコン相は非金属相です.共晶組成の合金がゆっくり凝固するときには,α固溶体とシリコン相は同じ速度で成長して,どこにもα固溶体のデンドライトが見られないような共晶組織を形成します.けれども急冷等で過冷度が大きくなるほど,α固溶体の成長速度は,シリコン相よりも速くなります.そうすると共晶組成であるにもかかわらず,α固溶体のデンドライトがみられることがあります.このことは,少し専門的にはカップルドゾーンという概念で,鋳鉄,Al-Si合金の区別なく,統一的に説明されています.結果としては,金属相と非金属相からなる共晶合金は,冷却速度が増すほど,金属相のデンドライトが組織中に現れる傾向にあります.Al-Si合金の場合,冷却速度が速いときに,デンドライトが晶出した後,デンドライト間隙の液相の濃度が過共晶領域に達し,初晶シリコンとしか解釈のしようがないシリコン相が晶出することもあります.ブレージングシート材を製造する過程ではしばしば問題になります.こうした現象もカップルドゾーンの概念を学ぶと特殊現象とせずに説明できます.
(『鋳造工学』89巻6号掲載)
アルミニウム合金溶湯の温度と粘性の関係はどうなっているのですか?
一般的にアルミニウム合金溶湯の動粘度は水とほぼ同じで流れ挙動ではレイノルズ相似則を容易に適用することが出来ます.一方で粘度(見かけ粘度)は,溶湯温度が液相線温度よりも高い領域では,温度による粘度の変化はさほど大きくありませんが,液相線温度よりも低下すると粘度は上昇します.これは固相率の増加が原因であり,固相率が約0.3~0.5より増加すると粘度は急激に上昇すると言われています.したがいまして,液相線温度と固相線温度間の固相率と温度との関係を調べる必要があります.この関係は単純な直線関係ではありませんが,これが既知であれば,溶湯の粘度が急上昇する固相率から温度が推定できることになりますので,湯流れ凝固過程で溶湯流動停止を推定するときに役立つ情報となると思われます.
(『鋳造工学』89巻6号掲載)
厚肉鋳造品では内部と外部で冷却速度が異なりますが,機械的性質にはどのような影響を及ぼしますか?
機械的性質を論ずる前に肉厚部では押し湯からの溶湯補給が不足して巣ができることが第一義的に心配です.合金によりますが,内部の凝固が表層よりも遅延するため,表層部の凝固シェルが内部へ引っ張られることがあります.表層部の凝固完了前にこのことが発生すると外引けになります.外引けすると内部の凝固はますます遅延することになります.鋳型とのエアギャップの発生を考慮しないと凝固解析及び巣の発生位置の予測精度に問題を起こすことがあります.凝固割れの予測についても同様です.デンドライトが発達しやすい合金では特に注意が必要です.溶湯補給性が悪い,すなわち溶湯移動の際の圧力損失が大きくなりやすいためです.
表層部の方が内部よりも凝固速度が速いため,鋳鉄の場合は表層部で客先要求の黒鉛形状にならない場合は問題になることがあります.アルミニウム合金の場合は凝固速度が速いほど組織が細かくなり強度も良好になります.特に高圧ダイカストでは顕著です.切削除去すると急冷組織の良さが活用されないことになります.また,均一な肉厚の部品の鋳造ではなく部分的に薄肉部を含む場合は残留応力や変形が生ずることがあり,部品に対する要求事項によっては問題になります.(『鋳造工学』87巻9号掲載)
片状黒鉛の形状はA型が良い,と言われる理由は?
片状黒鉛鋳鉄の機械的性質は黒鉛形状と基地組織に大きく影響されており,「A型黒鉛が良い」と言われています.昔は,A型の方が黒鉛の先端が丸いので,応力集中が少なくなるため機械的性質が良くなるといわれた時期もありました.しかし,黒鉛を3次元的に考えれば,この説は正しくないと考えられます.
まず,パーライトの多い鋳放しの片状黒鉛鋳鉄においては,D型黒鉛の割合が少なくA型黒鉛の割合が多くなるほど,引張強度と伸びがともに高くなります.D型黒鉛の周辺には柔らかいフェライトが生じやすい事と,伸びの低いD型黒鉛から破壊がスタートする事が,その原因と考えられます.
一方,フェライト化焼鈍をしてフェライト基地にした片状黒鉛鋳鉄においては,A型黒鉛が増すにつれて伸びは増すものの,パーライトの時ほど引張強さには大きな変化はありません.詳細は『鋳造工学』第77巻(2005年)12号P836を参考にして下さい.
いずれにしても,A型黒鉛になるほど伸びが高くなることは間違いないことのようです.材料が壊れるか否かは,伸びが0.5~2%程度しかない片状黒鉛鋳鉄においても,伸びが重要な要素となります.また,A型黒鉛になるということは,接種が十分に効いていることを示しており,このことは共晶セルが小さく,共晶セル数が多いことも意味しています.これも,A型黒鉛が良い別の理由と考えられます.
(『鋳造工学』88巻9号掲載)
シェルモールドやコールドボックスの砂の充填シミュレーションにはどんな手順,手法が用いられますか?
シェルモールドやコールドボックスの砂の充填ではブロー造型が多く使用されます.ブロー造型の場合,鋳枠あるいはコアボックスへ砂を運ぶ工程と,砂の配列が変化して粗から密になる砂の圧密化工程とに分けて考えると良いでしょう.
まず砂を運ぶ工程ですが,ある速度と圧力をもって砂と空気が移動するため,流体の方程式を解くことが一般的で,砂と空気が存在するため固気混相流で解く必要があります.固気混相流の解き方には,砂も空気も流体として取り扱うモデルとして,(1)砂と空気が混ざり合った状態で1つの流体とみなす1流体モデル,(2)砂と空気それぞれの流体として解く2流体モデル,(3)砂は固体として,空気のみを流体とする1流体+砂粒子モデルがあります.流体の運動を解くときは,ナビエストークス方程式を支配方程式とすることが多く,また固体の流動を計算するときには流体から受ける抗力を計算して運動方程式を解く手法が多く使われています.
次ぎに,砂を圧密化する工程ですが,これも(1)砂と空気が混ざり合って1つの物体(連続体)であるとして,応力-ひずみ関係を有限要素法などで解く手法と,(2)砂を素直に球形の固体(粒子)とみなして離散要素法(個別要素法)で解く方法があります.
計算機能力(主に計算速度とメモリ容量)から,また流体力学や構造力学の既存ソフトを転用できるメリットを活かし,オイラー系連続体解析が主流となっています.一方,最近はコンピュータ能力向上(GPGPUやクラウド並列化)からラグランジュ系離散化手法が注目され開発が進んでいます.
なおソフトウェアのポスト処理では砂粒子を見せたり隠したりすることが容易なので,グラフィックを見ただけで解法は判断できませんので注意が必要です.
(『鋳造工学』92巻3号掲載)
パーライトはどうしてラメラ組織になるのですか.また冷却速度や強度との関係を教えてください.
オーステナイトからフェライトとセメンタイトが同時に析出するときに,ラメラ構造をとることが多く,この組織をパーライトと呼びます.どのような形態になるかは,相の体積率と界面エネルギー,拡散時間との兼ね合いで決まります.金属の組織はできるだけエネルギー的に安定になろうとするので,球状の形態をとろうとします.しかしながらセメンタイトの体積率がある程度多い場合は,球状でたくさんのセメンタイトが出ると逆に界面が多くなり,全体としてのエネルギーが大きく不安定になります.またパーライトにおけるフェライトとセメンタイトは特定の方位関係を持っており,お互いの結晶構造の関係から界面が平らであるほうが比較的安定になるようです.そのためセメンタイトは球状よりも板状の形態をとるようになります.もちろん条件によっては,棒状や球状のセメンタイトも見られます.
フェライトとセメンタイトは炭素濃度が異なりますので,成長する時は拡散が必要になります.拡散する時間が十分あれば層間隔は広くなりますし,時間があまりなければ層間隔は狭くなります.すなわち冷却速度が早いほど層間隔は狭くなります.純粋な共析鋼すなわちパーライト100%の材料では,引張強さや降伏応力は層間隔をλとすると.σ=σ0+k/λと表されるようです.すなわち強度特性は層間隔の逆数と直線的な関係にあります.ただし,実際の材料はパーライトだけでできているわけではないので単純には整理できないと思ってください.何れにせよ層間隔が狭いほど強度は大きくなります.従いまして,冷却速度が大きければ強度も大きくなることになります.
(『鋳造工学』92巻8号掲載)
球状黒鉛鋳鉄は構造材として何℃まで使用可能でしょうか?球状黒鉛鋳鉄の温度変化に伴う強度について教えて下さい.
球状黒鉛鋳鉄の温度変化に伴う強度の変化ですが,室温以下の低温では脆化現象を引き起こす事により,引張強さ及び耐力は増加し,伸びは低下します.一方,高温側では約200℃付近までは引張強さは概ね室温と同定度の強度を示しますが,300℃以上になると強度は急激に低下し,500℃以上では室温での引張強さに比べ,半分程度となることが報告されています.
また,一般に構造材料として用いられている球状黒鉛鋳鉄は,基地組織がフェライトとパーライトの混合組織もしくは単相のものですが,特にパーライトを基地組織とするものは高温になるにつれて,強度低下が顕著に見られます.また伸びは基地組織によらず温度上昇とともに低下していきます.特に400℃付近では室温での伸びに比べ,半分程度となりますが,その後は回復傾向を示します.これは基地組織中のパーライト量が多いほど増加していき,基地組織がパーライト単相のものでは室温での伸び以上になることが報告されています.
これらのデータから判断すると,球状黒鉛鋳鉄を構造材料として使用するには200℃までと言えるでしょう.(『鋳造工学』87巻9号掲載)
ADC12合金のダイカスト品のゲートを折ると製品まで欠けこんで不良が出来てしまいます.破面が平らになっている部分が見受けられます.原因と対策は?
欠け込み不良の原因として,破面が平らになっている部位があるという事から,初期凝固片(破断チル層)や溶湯酸化膜等の噛み込みが,主因として推察されます.特に,初期凝固片(破断チル層)は,スリーブ内に溶湯を給湯したときに,スリーブ壁との接触面で形成された凝固層が,射出と共にプランジャーチップにより破壊されて断片化したもので,それが溶湯に運ばれてゲート付近に残留すると,その部位の強度が低下するため,ゲートを除去する時に,製品まで欠け込む原因となるものです.発生を抑制するには,スリーブを保温したり,断熱性の高いスリーブを使用したり,スリーブ内の溶湯充填率を上げるような発生防止策が考えられます.又,混入を抑制するために,湯道や,ゲート形状を工夫する対策も考えられます.一方で,発生源対策ではなく,ノッチをつけてゲートの折り位置を誘導したり,折り位置の拘束を確実にしてから折るなどの工夫により,欠け込み不良を抑制する事例も存在します.適切な対策を試みてください.
(『鋳造工学』88巻9号掲載)
ADC14合金を初めて使用しようと思いますが,特に気を付けるべきことはなんでしょうか.通常はADC12合金を使用しています.
ADC14合金はSiを約17%含有する過共晶Al-Si合金で,Siの凝固潜熱がAlに比べ20%多いため,鋳造性が良好で,ADC12合金と同じ方法で鋳造できます.但し,液相線温度が650℃とADC12合金に比べ,約70℃高いので,溶湯温度を高くする必要があります.またダイカスト品に晶出する初晶Siの結晶が加工性を阻害したり,機械的性質を低下させる問題があり,初晶Siの粗大化を防止する必要があります.P化合物などの微細化材の添加とスリーブ中で初晶の成長を防止するため注湯温度を高くする工夫などが必要です.なお鋳肌部に初晶Siが晶出しないフリーゾーンが存在するので,耐摩耗機能が鋳肌部に要求される場合は,注意が必要です.
(『鋳造工学』92巻3号)
鋳物のひけ巣の部分にデンドライトが観察される理由はなんでしょうか?
一部の金属(SiやBi)を除き純金属や合金は,凝固の際4~6%程度凝固収縮します.よって型鋳造では,体積収縮をまかなうだけの溶湯の補給が
なければ,凝固収縮分がひけ巣となって,鋳物の内部あるいは表面に現れることになります.なお,凝固の仕方によって,ひけ巣は様々な形態を呈します.
さて,多くの合金はデンドライト凝固します.デンドライトは,まずジャングルジムのように幹や枝が線成長し,その後枝の間の液体が固体と変化する,すなわち枝が太っていくことによって完全な固体となります.この際,凝固収縮分の体積の溶湯が補給されるならば,元々液体で占められていた空間は完全に固体で充填されますので,凝固後には元のデンドライトの形は観察されなくなります.
しかし,最終凝固部では残留している溶湯が少なくなり,十分な溶湯補給が困難となり,そこでの凝固収縮分を補充することができなくなります.よって,デンドライトの先端部の枝はそれ以上太ることができず,元の枝状の形態のまま最終凝固部に残ることになります.これが,鋳物のひけ巣の部分にデンドライトが観察される理由です.
(『鋳造工学』92巻8号)
球状黒鉛鋳鉄の共晶凝固時,黒鉛はオーステナイトに囲まれて球状に成長すると聞きました.オーステナイト(γ,固体)と黒鉛の界面で黒鉛がγから析出してより大きな球状になるのでしょうか?
鋳鉄の根幹に関わる重要な質問ですネ.球状黒鉛鋳鉄の生成と成長には賛否両論いろいろな説があります.生成に関しては,雪の結晶と同じでどんなものでも核の元にはなるのですが,最近では硫化物の核がより効果的であるとする説が多くなってきました.冷却速度の大きい発光分光分析用のチルした球状黒鉛鋳鉄の試料などを観察すると,最初の黒鉛はどうも溶湯から直接発生しているように見えます.また,瞬時にオーステナイトに囲まれることもわかります.共晶凝固なのでオーステナイトトと黒鉛が同時に出るのは当たり前ですネ.その後の成長ですが,過去には液体と通じている部分がありこの部分を通して拡散が進み,黒鉛が成長するといった説もありました.細かな計算は省きますが,片状黒鉛の共晶セルの直径を4mm,球状黒鉛鋳鉄の黒鉛の直径を0.06mm,凝固に要する時間を20分,製品肉厚を60mmとすると,片状黒鉛鋳鉄の共晶セルの成長速度は6mm/h,球状黒鉛鋳鉄のセルの成長速度は0.2mm/hとなり,球状黒鉛の成長速度は片状黒鉛の1/30と言う事になるそうです.固体であるオーステナイトを通してのカーボンの拡散がいかに遅いかが分かります.質問に答えると,球状黒鉛鋳鉄はカーボンを固体のオーステナイト層を通して液体部から拡散により吸収し成長することにより,より大きな球状黒鉛となっています.
日本,中国,インドなどの生砂の違いは何でしょうか?
生砂に求められる条件は,適切な化学組成及び物理的性質を有し,かつ砂粒は適度な粒度分布を有し,粒形は丸形に近いものです.
日本で使用されている生砂は,国産が半分弱でその他はオーストラリアやベトナムからの輸入です.国産砂のSiO2の含有量は産地により異なっています.国産砂は粒形がやや角張っている傾向にあるのに対して輸入砂は丸味を帯びているものが多いのが特徴です.
中国で得られる国産砂は,産地によって特性が大きく異なります.内モンゴル産は形状が丸味を帯びているがSiO2の含有量が低いのに対して,福建省産は角張っている傾向にあるがSiO2の含有量は高いです.両砂とも粗い砂が多く含まれていることから焼付きが発生し易いです.
インドで得られる国産砂は,角張っていて粒度分布がシャープになる傾向にありますが,SiO2の含有量は非常に高いです.なお,粘土分の少ない細かい砂が得難いといわれています.
韓国では,国産が少なくベトナムやオーストラリア等から輸入した鋳物砂を使用しており,大きな問題がないといわれています.
なお,中国やインドでも造型機の高度化に伴い,国産砂では問題発生が多いことから,海外からの輸入が増加しています.
(『鋳造工学』91巻12号掲載)
チャンキー黒鉛は,凝固時間が長い厚肉鋳物の最終凝固部に生成されることが一般的に知られている.更に溶湯処理剤(球状化剤や接種剤)を構成するCa,Si,Ce,Niなどの元素がチャンキー黒鉛の生成に影響を与えると報告されている. 一方,数kg~十数kgの小物鋳造現場での経験では、チャンキー黒鉛が出やすい製品において,注湯温度が高いより低い時の方が発生しやすい.これは,厚肉大物球状黒鉛品と真逆になると思われますが何故でしょうか?
注湯温度の影響に関しては,一般的に高温注湯の方がチャンキー黒鉛出やすいことが知られています1).厚肉大物品に於いて低い注湯温度の方が出やすいとの知見は殆どありません.だからと言って,貴殿の質問を否定することも出来ません.
チャンキー黒鉛についてイレギュラーな一例をあげると,自動車用一般肉厚が5~10数mm程度の薄肉筒状小物品だが,高Si組成(3.5%Si以上)のエキゾーストマニホールドでは,悪い条件が重なってくるとチャンキー黒鉛が発生することがあります.その原因の一つに低温注湯が挙げられています.
ここで、なぜ高Si組成の薄肉鋳物でもチャンキー黒鉛が発生し,かつ低温注湯の方が出やすいのか,その理由について以下に考えてみます.
チャンキー黒鉛の生成は球状化剤,接種剤及び配合地金中の微量元素を含めた化学組成的な主要因が存在するほかに厚肉鋳物であること,すなわち凝固速度が遅いことが共通点であると言われています2,3).凝固速度が遅いとは,最終凝固部で黒鉛粒数が減少し,球状黒鉛を囲むオーステナイト層の厚さが増大するので,炭素の拡散速度が低下し,黒鉛化が困難になるため球状黒鉛からチャンキー黒鉛に連続成長すると解説されています2).一方,薄肉鋳物で低温注湯の場合,凝固速度は早いため,黒鉛化すなわち球状黒鉛としての成長が困難になり,鉄セメンタイト共晶凝固してレデブライト組織になるのが普通ですが,高Si組成が故にチル化にならずに球状黒鉛でなくチャンキー黒鉛に成長し得ると考えます.また,低温注湯でチャンキー黒鉛が出た実例にはFe-Si系接種剤による注湯流接種の不均一,すなわちSiの局部的に濃化4)にも影響される一因と考えられます.詳しくはそれらの解説にご参照いただければ幸いに思います.
1) 菅野利猛:鋳造工学,76(2004)130
2)例えば,中江,辛ら:鋳造工学,75(2003)337
3) 津村 治:鋳造工学,76(2004)125
4)木口昭二:鋳造工学,76(2004)114
(『鋳造工学』第88巻第4号掲載)
鋳造の始まりは,いつ,どこ?
紀元前3,000年ごろにメソポタミアの南部に国家都市を建設したシュメール人が残した人類最古の粘土板の中に,鍛冶工や銅を意味する絵文字が書かれています.また,この地方を流れるチグリス・ユーフラテス川の上流は古代の銅鉱石の産地であり,青銅製の武器や装飾品がシュメール国王たちの墓から出土していることからも,この地域が鋳物づくりのはじまりと考えられています.きっかけは,たき火をするうちに偶然始まったと言われています.日本には紀元前300年ごろに中国大陸から朝鮮半島を経て北九州の海岸地帯に鋳造技術が伝わりました.日本で鋳物づくりが始まったのは,出土した鋳型の年代などから推定して弥生時代中期(紀元前100~紀元100年)であろうと考えれています.
(『鋳造工学』90巻9号掲載)
純銅系の鋳物では,黄銅や青銅に比べガス気泡欠陥ができやすいのは何故ですか.
銅合金鋳物に発生するガス気泡には,水蒸気ガス気泡と水素ガス気泡の2種類があります.どちらが発生するかは,溶銅に溶け込んだ酸素量と水素量のバランスによって決まり,同じ水蒸気分圧下では酸素量と水素量は逆相関の関係にあります.酸素と水素が共存する溶湯を鋳造すると非連続の水蒸気ガス気泡が発生し,酸素が少ない溶湯では連続した水素ガス気泡が形成されます.溶湯中のガス量は,雰囲気中の水蒸気分圧(湿度のようなもの)の増加と溶湯温度の上昇に従って増加しますので,最近鋳物工場で多く使用されている電気炉溶解では大気中の水蒸気分圧が燃焼炉に比べて低いためガス気泡の発生は少なくなります.
黄銅溶解では含有されるZnによって酸素はZnOとなり,水素はZnの蒸気圧で溶湯中から排出されるため,溶湯中の酸素および水素は少なくなり,鋳塊にはガス気泡欠陥が殆ど発生しません.青銅では,溶湯中に水素と酸素が存在するため水蒸気ガス気泡ができやすいのですが,凝固形態がマッシー型ですので,デンドライト間の微細収縮巣内にガス気泡が形成され,見た目には区別がつきにくいです.リン青銅の場合は,溶湯中の酸素はP2O5となって系外に出ますので水素ガス気泡の発生を防止するため脱ガスを行うべきです.
純銅の分類には,リン脱酸銅・タフピッチ銅・無酸素銅があります.リン脱酸銅では溶湯中の酸素はリンにより無くなりますので水素ガス気泡の発生に気を付ける必要があります.タフピッチ銅は,酸素を含有するため水蒸気ガス気泡が発生しますので凝固速度を早めて微細水蒸気ガス気泡にして細かく分散させるか脱水素処理を行うことが重要です.無酸素銅では酸素ならびに含有元素がありませんので,特に水素の影響を受けやすく鋳塊には連続した水素ガス気泡を発生しやすく,十分な脱水素処理を行うことが必要となります.
(『鋳造工学』91巻12号)
ダイカスト製品でイヌキ穴の中が引けております.何が原因で何を対策したらよいのでしょうか?
ダイカストでは鋳抜き穴を形成するために鋳抜きピンを使用します.鋳抜きピンが細い場合や,湯口から流入する溶湯が直接当たる場合,ピンが溶湯で加熱され,ピン回りが最終凝固部になります.そして製品の肉厚が厚い場合に鋳抜き穴に引けが発生します.対策は,ピンが加熱されないように冷却を入れることです.冷却が入らない場合は,溶湯が直接ピンに当たらないように方案変更することが有効です,その他にピンの回りの金型温度を上げピン回りが最終凝固部にならないようにすることや,高速速度を速くし巻き込まれるガスを製品中に細かく分散させ最終凝固部に引け巣が集中しないようにする対策も使われます.
なお熱容量が少ないピンに冷却を入れるとピンが冷えすぎて塗布した離型剤が乾かず水分が残り,これによって巣ができることがあります.JECSSのような装置を用いて溶湯充填後,冷却水をエアーパージするなどして,ピンが冷えすぎない対策をとる必要があります.
(『鋳造工学』第90巻6号掲載)
球状黒鉛鋳鉄製自動車部品の図面でFCD700代替試験片の引張強さ,伸び,耐力,硬さを報告しますが,設計時にこれらの値をどう使っていますか?
JIS G 5502の球状黒鉛鋳鉄品では,FCD700の引張強さ,耐力及び伸びの値は,別鋳込み供試材(代替試験片)での評価で規定されています.設計時にはこれらの値を基に,安全率を加味した値を用いて強度計算を行い,部品形状を決定します.別鋳込み供試材と実部品から切り出した試験片の機械的性質は異なり,実部品の試験片の方が低い値となります.従って,設計時に用いる安全率にはそれらの差も考慮されています.部品の評価は,それぞれの部品に応じた評価法で評価をしますが,材料の機械的性質の評価は,実部品から切り出した試験片を用いてチェックします.
(『鋳造工学』90巻5号掲載)
生型造型において,よく月曜日の朝の砂は暴れると呼ばれるといわれますが,砂自体に何か起こっているのでしょうか?
生砂造型ラインで『週末から週明けにかけて砂があばれる』と呼ばれることがあります.
週末など稼働時間終了間際ぎりぎりまで注湯した後解枠せずそのままにして操業を終了した場合,週明けのライン稼働開始時に生砂の湿態性質が不安定で管理値内におさまりにくくなる場合があります.特に冬季や雨季にはその傾向が高くなります.
生砂の湿態性質は水分の制御に依存しています.注湯後長時間枠内で製品とともに放置されていた鋳型の生砂は,徐々に周囲環境の気温まで下がっていきます.製品を取り囲む鋳型の水分は水分凝縮層を形成し,製品に接する生砂の水分は非常に低くなり,一方水分凝縮層付近では過飽和状態にまで水分が高くなった過剰水分層が出来てしまいます.湿度が高かったり,外気温が低く結露しやすくなる環境では尚更です・寒冷地では冬季長時間放置しておくとこの過剰水分層が凍結し,解枠が出来なくなってしまうといった現象に見舞われてしまうことさえあり,冬季には必ずラインの稼働を続けて解枠までを済ませてしまわなければならいといったことも起こります.長時間枠内に放置された生砂には,製品に接して高温に曝(さら)され水分がほとんどないまたベントナイトなどの粘結材は焼成された状態の箇所,水分凝縮層が発達した過剰水分層ここでは粘結材はほとんど加熱されていない箇所,そして全く熱の影響を受けていない箇所が形成されます.通常に解枠された状態ですとごく短い時間で形成された過剰水分層の箇所は全体的には僅かな割合です,搬送されていくうちに混じりあって大きな偏りが出にくいのですが,長時間枠内放置されて形成された過剰水分層が塊となって搬送されると混じり合わなくなります.造型ラインの設備構成にもよりますが,解枠後の砂が冷却され,この塊が崩れたときにも残っている水分量のバラツキが大きくなり,調砂工程で添加すべき水分の調整が難しくなってきます.結果として管理値内を大きく暴れることになります.調砂工程では解枠後搬送されてきた砂には塊などのないようにほぐされ,充分に熟成されたことを前提に砂の温度と残った水分をはかりながら水を添加し,粘結材を添加して混練が行われていきますので,水分の過剰な塊によって全体が乱されることになり,暴れていると表現されています.
対策としては,長時間放置した後の解枠時には,(ブロッキング)塊が起きていないか,過剰な水分の塊が搬送されていないかを監視する必要があります.
(『鋳造工学』第90巻6号掲載)
ダイカスト工場でIoTを進めなさいと上司に言われているのですが,何をすれば良いかわかりません.まずは,鋳造の計測だと思うのですが,鋳造機に使えるセンサーは何があるのでしょうか? また参考になる論文などあるのでしょうか?
質問者様の目的が不明ですし,また現在の鋳造計測状況が不明ですので,どこから進めればいいのか説明するのは簡単ではないのですが,一般にIOTのために新たにセンサーを設置して計測を始めても期待する効果が得られず失敗に終わるでしょう.まず,今まで品質管理上計測してきたデータや条件チェック等のデータを製品個々の良品不良品の情報と紐づけることが,1歩だと思います(.そして記録したデータの見える化を進めます.
1.良品条件として設定した鋳造条件の設定が守られているか記録する.
2.計測しているデータやチェック効果を見える化し,大きく変動しているものがあるか,相関のあるパラメータがあるか確認する.
この段階で鋳造機,保持炉などからのデータをどのように加工し記録するか,どの時点でクラウド(サーバーや記録装置などのインフラ機能をネットワーク経由で提供するサービス)に上げるか,データを見える化するためのソフトの選定を進めます.これらのIoTのインフラが整った段階で設定した条件で製造しても不良が出てしまうのであれば,新たな計測の追加を検討するのがいいと思います.
3.次の段階で製品に番号を付け後加工工程での鋳巣不良や漏れ不良と計測データとの紐付けをします.
このような流れで鋳造条件のデータと後加工不良とが結び付けられれば良いと思います.論文関係では,鋳造関係では甲南大学の長坂教授の解説記事(SOKEIZAI Vol.59(2018)No.7)などが参考になるかと思います.
(『鋳造工学』91巻3号掲載)
私の職場私の職場では低圧鋳造法を用いてアルミ合金鋳物を製作しています.製作する過程で無機中子を用いていますが,中子に使用する砂の粒度を毎日測定しています.この粒度が粗すぎたり,細かすぎたら中子にどういう影響を与えるのでしょうか?では低圧鋳造法を用いてアルミ合金鋳物を製作しています.製作する過程で無機中子を用いていますが,中子を使用する粒度を毎日測定しています.この粒度が粗すぎたり,細かすぎたら中子にどういう影響を与えるのでしょうか?
中子砂の粒度の管理はふるい分け法を用います.JISでは3メッシュ~270メッシュまでの間の14種のふるいと270メッシュ以下のパン分をあわせて15種類の粒度にわけ,この粒度分布を数字で表示したのが粒度指数です(JIS Z2601-1993).この粒度指数は細粒ほど値が大きくなる特徴を有しています.一般には粒度指数が大きくなると砂型の通気度は悪化します.この為,中子砂の場合,粒度指数が大きいと,通気度悪化による吹かれ,種々のガス欠陥及び,粉塵増加により中子造型時にベントが詰まり中子充填性の悪化,比表面積の増大による強度低下が起こると考えられます.この対策としてバインダー量を増加した場合,製品のガス欠陥,中子崩壊性の悪化が起こります.逆に粒度指数が小さくなると中子の充填性が悪化することによる造型不良,製品面粗度の悪化等が発生します.この為,鋳物砂の管理では粒度指数の測定が重要な管理項目となります.
(『鋳造工学』92巻11号掲載)
「圧力容器(FC300)穴加工後の水圧検査で鋳肌面に微小な漏れが発生しました.原因としまして,どのようなことなどが考えられるでしょうか.また、黒鉛や粒界を介して圧漏れすることはあるのでしょうか.
漏れるということは内側と外側がつながった不良ということなので,考えられるのは割れや湯境、表面から見えにくい異物かみ(砂、ノロ)等の不良が考えられます.これらの不良は目視でよく見れば分かると思いますが,微小なものはわかりにくいと思います.このほかに引け巣が考えられます.これが加工によって目で見えないような微小な引け巣(場合によってはマイクロシュリンケージと呼ばれる顕微鏡で見ないとわからないような引け)が表に出て,外に通じてしまっていることも考えられます.(ご質問にある黒鉛の粒界から漏れることは、熱処理品でない限り,ないでしょう.)
漏れたところの浸透探傷検査(カラーチェック)をされたでしょうか?この検査によって表に現れた欠陥の形で何かわかるかもしれません.また,欠陥が出るように欠陥部を切断しSEMで観察すればさらに原因が分かると思います.
(『鋳造工学』91巻3号掲載)
亜鉛合金のホットチャンバーダイカストマシンに取り付けられているノズルに関して質問です.連続稼働時間が長くなるにつれて,ノズル先端が詰まってしまい(流路を塞いでしまい)最終的には射出不良になってしまいます.ホットチャンバーダイカストマシンにおけるノズル詰まりのメカニズム及び対策(ノズルの形状,表面処理など)をご教示頂きたいです.
ホットチャンバーマシンのノズル詰まりは,大変難しい問題です.必ずしも明確になっていないようです.
ノズル詰まりには,次の3種類があると考えられます.
1つ目は,ノズル先端の凝固による詰まりです.これは,ノズル温度が様々な理由で低下したことによります.例えば,メルティングポットの湯面が低下して,ノズル温度が低下してノズル内の溶湯が凝固する場合があります.また,ダイカストマシンの構造にもよりますが,スプルーブッシュの冷却が強すぎて,ノズル先端が凝固する場合があります.湯面高さの維持や,スプルーブッシュの冷却の適正化などを行うことで改善できると思います.
2つ目は,リターン材が多い場合やインゴットの清浄度が低い場合などに,ノズル内で酸化物などが堆積してノズル詰まりを起こす場合があります.リターン材を40%以下にしたり,清浄度の高いインゴットを使用したりすることで,回避できると思います.
3つ目は,亜鉛合金中に含まれる4%程度のアルミニウム成分と,ノズル(SKD61)の鉄が反応して,Al-Feの金属間化合物が,ノズル内に層状に形成されて,それが繰り返しの鋳造により成長して,ノズル詰まりになるものです.この場合は,定期的にリーマなどでノズルの清掃を行ったり,ノズルに窒化などの表面処理を行ったりすることで改善できると思います.さらに,ノズル径を適正化します.ノズル径は,溶湯の流量を考慮して選定しますが,径が小さいと詰まりやすくなります.
ご質問の場合のノズル詰まりは,恐らく3つ目ではないかと思われます.金属間化合物層が形成される前に,清掃を行うことが大切かと思います.いずれにしても,ノズルとスプルーブッシュの構造にも依存するので,ダイカストマシンメーカー及び金型メーカーに相談することをおすすめします.
(『鋳造工学』92巻11号掲載)
亜共晶組成の方がチル化しやすいのですか?
まず,鋳鉄の溶湯は,塩水(水と塩)や砂糖水(水と砂糖)と同じような溶液である.鋳鉄の場合は高温の鉄(液体)と含有成分(C,Si,Mnなど)になる.ここでは炭素が液体の鉄の中に溶け込んでいる1500℃の溶液が凝固するまでの過程で話そう.
凝固温度は,鉄-黒鉛共晶凝固(Fe-G)で1,152℃,鉄-セメンタイト共晶凝固(Fe-Fe3C)で1,145℃である(Fe-C系状態図,M.Hansen and K.Anderks).鋳型に鋳込まれた溶湯の温度は低下し続け,ある温度(初晶温度)から溶湯中に固体(初晶)が出始め,増加していく,同時進行で液体は減少し続け,共晶凝固温度域に達して全てが固体となるが,チル無しの鋳物になるかどうかは分らない.チル無しにするには,Fe-G共晶凝固温度で残湯が共晶組成(CE=4.3%)になり,かつFe-Fe3C共晶凝固温度に達する前に凝固が完了しなければならない.もしもFe-Fe3C共晶凝固温度以下で凝固する残湯があれば,そこにはチル(レデブライト)が発生する.
さて,亜共晶組成の溶湯はCE<4.3%,従って溶湯中に発生する固体は,溶湯より炭素含有量(固溶度)の低い初晶オーステナイト(初晶γ)で,共晶凝固温度に達するまで溶湯中に増え続け,そこから吐き出された炭素分は,残湯のCEを上昇させ続ける.平衡状態凝固ではFe-G共晶凝固温度での残湯は共晶組成のCE=4.3%になっているが,通常の鋳物は非平衡状態で凝固するので,残湯の一部は共晶組成になる前にFe-Fe3C共晶凝固温度以下になり鉄-セメンタイトの共晶凝固することになる.
ここからが本題で,CE以外の全てが同じ条件で溶湯が鋳込まれたとしよう.CEが4.3%より低い溶湯を,チル無しで凝固させるには,Fe-Fe3C共晶凝固温度に達するまでに初晶γ(固体)から吐き出された炭素で残湯のCEをFe-G共晶凝固ができる4.3%にしなければならない.凝固までの限られた時間で,CEの低い溶湯と高い溶湯を比べると高いほうが始めから残湯中のCE%が高く,初晶γからの炭素供給が少なくて済み共晶組成(CE=4.3%)に達しやすいことがわかる.即ち,亜共晶組成においては,同じ凝固までの時間で残湯が共晶組成(CE=4.3%)に達するかどうかで,残湯が鉄と黒鉛の共晶凝固をするか,鉄とセメンタイトの共晶凝固するのかが決まる.従って,CEが低い溶湯の方がチル(Fe3C)化しやすい傾向がある.今回は鉄-炭素二元状態図で「亜共晶組成でのCE%変化とチルの関係」を説明したが,他に過共晶組成でのチル,含有元素,接種処理との関係なども分りやすく説明されている図書を下記に紹介します.勉強して下さい.
①素形材センター発行(平成24年10月),
鋳造技術シリーズ3「新版 鋳鉄の生産技術」,第2章「鋳鉄の状態図(P3~)」
②産業出版発行,中江秀雄著,新版「鋳造技術」
(『鋳造工学』86巻8号掲載)
ダクタイルはFCにくらべて,なぜ,ひけやすいのでしょうか
鋳鋼やアルミニウムなどは,凝固収縮を補うために大きな押湯を必要とします.しかし,鋳鉄では黒鉛晶出による体積の増加があるので,基地(鉄)が凝固時に収縮しても,それを上回る程度の膨張があって,そのためにひけがない,あるいは発生しにくい,ということは比較的納得しやすいと思います.この欄でも86巻3号(2014年3月号),4号などでこれに関することが述べられています.
この考え方によれば,ダクタイル溶湯とFC溶湯で,炭素量(より詳しく言えば,晶出する黒鉛量)が異なるのであれば,両者でひけ傾向が異なる,ということになりそうです.
しかし,一般的な炭素量は,鋳物の大きさや強度によって多少の違いはあるにしても両者で数%以上も違うことはないでしょう.FCでは高強度材で炭素量を少なくすることもあるし,ダクタイルの小物品では共晶付近の炭素量とすることが多いでしょうから,そういうときはむしろ逆になるか,せいぜい,ひけ傾向は同じ,ということになりそうです.
そこで,もう少し考えると,たとえ同じ晶出黒鉛量であっても凝固過程が異なるとひけ発生状況が変化する,という説明が必要になりそうです.
「凝固過程が異なる」というのは,漠然とした表現ですが,ダクタイルとFCでは黒鉛の成長速度が異なるので,基地のオーステナイトの凝固状態(固相率の増加の状況)との関係から,全体としてマッシー状態が長く続く(粥状凝固),このためにひけが出やすい,というような説明が一般的にされています.このようなことを調べるために,黒鉛の晶出過程の調査,凝固時の膨張収縮の測定,冷却曲線の測定などの結果が多数発表されています.しかし,実際の鋳物では,これらに加えて鋳型の強度,製品の形状,鋳造方案,溶湯成分や原材料,接種,注湯温度など,さまざまな要因が複雑に絡み合うので,なかなか結論が出にくいらしく,「この指標でひけの傾向を表せば,ダクタイルとFCでこう異なる」とはっきりさせたよい例はあまり見られません.
このような状況なので,製造現場の感覚では「FCではひけが発生するときは押湯を大きくする程度の対策でよいが,ダクタイルでは単純に押湯を大きくしても,それでひけが止まるとは限らない」ということになるのでしょう.
(『鋳造工学』86巻6号掲載)
鋳鉄の溶湯は,金属なのに固まると非金属の黒鉛が出てきます.どうしてなのか教えてください.
鋳鉄は,鉄(Fe)と炭素(C)の合金であることはご了解のことと思います.このような合金は,溶媒(鋳鉄の場合は鉄)中に溶質(この場合炭素)が溶け込んでいると,溶媒の凝固温度が低下することがあります.さらに鉄の原子の結合(金属結合)と,炭素(黒鉛とすると共有結合)の特性が大きく異なりますので,似たような結合同士の合金より凝固温度の低下は大きいのです.また,珪素(Si)も鉄の凝固点を下げる元素です.鋳鉄はまさにこの炭素と珪素が含まれる合金であることになります.溶けた鉄の温度が下がると,溶湯中に溶け込める限界の炭素の量も下がるので,余分な炭素は黒鉛(非金属)として晶出します(安定系の場合).そして次には鉄と黒鉛が同時に晶出する共晶という凝固をとります.
さて,鉄と黒鉛の組み合わせで晶出する組織は,金属-金属の一般の組織と比べて不規則な組織となります.Crokerによれば,共晶組織は図1のように分類できます1).縦軸は2つの組織の体積率,横軸は溶融エントロピー(鉄と黒鉛は異質なので溶融エントロピーが大きくなる)で整理すると共晶組織は以下のようになって,
1:規則的な層状(normal lamellar) 例 Pb-AuPb2
2:規則的な棒状 (normal lod) 例 Cd-Pb
3:不規則で不連続な層状(anormalous broken lamellar) 例 Fe-C
4:不規則で複雑な形状(anormalous Complex regular) 例 Bi-Pb2Bi
鉄と炭素(黒鉛)の組み合わせは,黒鉛の体積率が小さく(7%くらい),2つの相が異質なので,領域3に分類されます.これが片状黒鉛鋳鉄の組織となり,まさに鋳鉄の特徴となります.
M.N.Croker: Proc. Roy. Soc.A.335(1973)15-37
(『鋳造工学』85巻9号掲載)
引け巣の出ない鋳物合金の開発は可能でしょうか?
なぜ,溶湯は凝固すると引けるのでしょうか?溶湯(液相)から固体(固相)に凝固(変態)する際に,実用合金のほとんどは密度が大きくなりますから,質量が一定ならば収縮しなければなりません.よって,「引け巣の出ない鋳造合金」とは,「液相よりも固相の密度が小さい合金」と言い換えられます.これは物理現象なので,逆転は有り得ません.
鋳鉄の場合,密度が7.0から7.3g/cm3の溶湯から約2.0g/cm3の黒鉛が晶出するので,生成する黒鉛の量が多くなるほど,体積膨張をおこし,凝固収縮量は減少する性質があります.そして,炭素当量(CE)が4.3のねずみ鋳鉄の場合,計算上は凝固収縮率ゼロになりますので,「引け巣の出ない合金」に成り得ます.Al-Si系合金の場合は,鋳鉄ほどではないけれども,約2.4g/cm3の溶湯から約2.3g/cm3のSiが晶出するので,他の合金系よりは凝固収縮率が小さくなり,Al-25%Siでほぼ収縮率ゼロになります.
ちなみに純Siは,融点における液相の密度が2.5g/cm3に対して,固相は2.3g/cm3という,少々変わった物質です.この様な例として他には,Bi,Geなどがあり,水もこの類です.
ところで,液相に溶けていたガス成分を凝固時に気泡で発現させると,見かけの引けがなくなる,という裏技?があります.例えばAl合金溶湯にわざと水素を溶け込ませて鋳造すると,製品中に気泡が発生し,「膨らます」ことで,有害な外引けや内引けを回避することができます.ただし,これはあくまでも「見かけの引け」防止対策なので,鋳物中に気泡が認められなければ使えません.また,強固な金枠内に薄い強固な鋳型を造型すると(例えば,メタルバックシェルモールド),鋳型の膨張で鋳物空間の体積が減少し,見掛け上,引けが減少することも報告されています.これは,鋳型の方に仕掛けがあるので,引け巣の出ない合金ではないですが.
以上,結論として,工業製品としての鋳物は,強度など要求される特性とコストから合金が選択されるのだから,ここで示してきた理屈を駆使しても,世の中のニーズを満たして「引け巣なし」を達成する合金の開発は極めて困難と考えます.
(『鋳造工学』83巻9号掲載)
『鋳造工学』を見て疲労について調べていたのですが,疲労試験と疲労き裂進展試験が行われていました.2つの試験の違いについて教えて下さい.
疲労とは,繰返し応力または繰返しひずみによって金属材料の性質が変化することを意味していますが,通常は1回の引張では破壊を生じない応力でも,これを繰返し負荷することにより材料にき裂が発生し,進展して破壊に至る現象を指して疲労と呼んでいます.疲労寿命は,き裂が発生するまでに要した繰返し数と,き裂が進展して材料が破壊するか,あるいは任意のき裂長さにまで進展するのに要した繰返し数の総和を表しています.
疲労特性を評価するために,次の2種類の試験法が用いられています.ひとつめは,き裂(あるいはき裂状の切欠き)を含まない平滑試験片に,応力あるいはひずみ振幅を制御した条件で繰返し変形を与え,試験片が破断するのに要する繰返し数を求めるもので,一般に疲労試験と呼ばれています.これによりS-N曲線(S:応力振幅,N:破断までの繰返し数)が得られます.疲労試験によって得られる寿命は疲労き裂の発生と進展の両方の過程を含みます.通常,き裂発生までの繰返し数は全寿命の90%近くを占めますので,この試験は疲労き裂発生に重きを置いた見方であると言えます.なお,ひずみ制御で行う比較的破断までの繰返し数が少ない試験を低サイクル疲労試験,応力制御で行う破断までの繰り返し数が多い試験を高サイクル疲労試験と呼んで区別することもあります.
ふたつめは,材料は不可避的にき裂(欠陥)を含んでいるものとし,その進展を破壊力学的に解析することによって材料の寿命を取り扱う試験で,これを疲労き裂進展試験と呼んでいます.ここでは,非破壊検査等で検出可能な欠陥寸法を基準として初期き裂長さを規定し,このき裂が破壊靱性値等を基準として決まるある臨界長さまで進展するのに必要な繰返し数を疲労寿命として定義します.疲労き裂進展試験で得られる経験的なき裂進展則(パリス則:da/dN=ADKm,da/dN:1サイクル毎のき裂進展量(き裂進展速度),DK:応力拡大係数範囲,A, mは材質によって決まる定数であり,mは金属材料では,一般に2〜7の範囲となることが知られています)を利用すれば余寿命予測をすることができます.このような方法は損傷許容設計として知られており,航空機や原子力発電設備の設計基準に利用されています.
凝固シミュレーションで最適な鋳造方案(早く,静かになど)を提案できても,溶湯の物性から考えると引け巣は無くならないと考えますが,如何でしょうか?
溶融金属が液相から固相に相変態するとき,ビスマスなど一部の金属を除いて,5%程度の体積収縮が起こります.凝固時に発生しますので凝固収縮と呼んでいます.実は,液相状態でも,固相状態でも,凝固収縮ほどではありませんが温度変化によって金属は伸縮しています.これら収縮分を補うことができなければ空隙ができ,内引け巣,外引け巣,面引けができることになります.体積収縮すること自体は材料物性ですので避けることはできませんが,製品部に巣をつくらない,巣を製品の外側,例えば,湯道,湯口,あるいは押湯にもっていくことは可能です.これが鋳造方案における引け巣対策の基本的な考え方になります.指向性凝固は,その一例になるかと思います.
(『鋳造工学』89巻11号掲載)
球状化率80%以上が球状黒鉛鋳鉄と規定されますが、その範囲内で機械的,物理的性質に差があるのでしょうか.
一般に同じ基地組織を有する鋳鉄において黒鉛粒の形状は,引張強さ,伸び,ヤング率等の機械的性質に影響を及ぼすといわれており,球状化率の低下と共に機械的性質も低下する傾向が見られます.鋳鉄では最大荷重近傍において,基地部の最大応力が黒鉛粒の端部ではなく,黒鉛と黒鉛の間の基地部に生じます.黒鉛球状化率が著しく低下した場合,片状黒鉛や粒状の黒鉛が多く存在することで黒鉛と黒鉛の間の基地部の連続性の低下,すなわち有効断面積が低下して,引張強さや伸びが低下します.しかし,球状黒鉛鋳鉄と定義される球状化率80%以上では,この有効断面積の低下の影響は小さく,引張強さや伸びの大きな変化はみられません.ヤング率も同様に球状黒鉛鋳鉄と定義される球状化率80%以上では変化は小さいのですが,球状化率70%以下になると低下の傾向が現れてきます.これは,黒鉛の片状化による弾性応力集中の増大,ひずみの増加の結果と考えられています.回答者の経験では,疲労限度や衝撃値も球状化率が80%以上では,ほとんど変化は見られませんでした.
また,基地組織が延性特性を有するフェライトの鋳鉄に比べて,パーライト基地の場合には,基地部の塑性変形が少ない状態で破断するので,黒鉛の形状の影響が大きくなると言われています.しかし,前述した様に球状化率が80%以上では,機械的性質の変化はあまり現れてこないようです.それ以下の球状化率になると,機械的性質に及ぼす球状化率の影響は基地組織の違いによって低下の程度が異なる結果も報告されていますので注意して下さい.
ダイカスト金型の焼き付きのメカニズムはなんですか?
ダイカストの焼付きは,金型にアルミが付着して製品の一部が削れる現象をいいます.
金型にアルミが付着する原因には次の2つがあります.第1の原因はアルミと金型が反応しAl-Si-Feの化合物層を形成することです.第2の原因はアルミと金型間の摩擦力がアルミの強度より大きるなりアルミが破壊することです.前者のアルミ付着は反応する臨界温度に支配され,これは主に金型の材質や表面処理の種類,Al合金の種類,離型剤の付着状況によって変化します.後者のアルミ付着は,離型剤の付着状況に主に支配され,離型剤の付着で防止していますが,抱き付き力が大きいところで離型剤が付着しないと発生する可能性が高くなります.離型剤の付着因子以外に,離型時の製品温度,金型の抜け勾配,表面粗さなどが影響します.いずれも,金型の温度管理が重要であり,前者は溶湯充填時の金型温度であり,後者は離型剤塗布時の金型温度の管理が重要です.金型の冷却による制御をきめ細かく実施することが要といえるでしょう.
(『鋳造工学』89巻11号掲載)
塗型の塗り方が作業者によって異なるようですが,大丈夫なのでしょうか?【フルモールド】
フルモールド鋳造法において,塗型工程の管理は品質を左右する重要な管理項目になります.作業者によって塗り方が異なる場合は,厚みのバラつきが懸念されます.
厚みが薄い場合,「浸透型の物理的焼着きの発生」を招く恐れがあります.また,厚く塗りすぎると「残渣の発生を助長する」ことがあります.厚く塗った場合は塗型剤が自重に耐えられず,液ダレによって局所的に厚みが薄くなってしまったり,過度に厚い部分では乾燥収縮による「塗型層の乾燥割れ」を引き起こしたりします.そうすると厚く塗布しているつもりでも,焼着きの発生が増加する危険性があります.
塗型剤の厚みをコントロールするには,以下の3点を抑える必要があります.1点目は「チキソトロピー」という性質です.この性質は簡単に言うと攪拌によって粘度が低下し,攪拌をやめると粘度が高くなる現象です.このような性質を持っているので,塗布するときは緩く塗りやすく,塗布された後は垂れずに膜厚みを保つことが出来ます.2点目は「温度変化による粘性変化」です.一般的には温度が高くなるほど粘度が低下します.まれに逆の挙動を示す塗型剤もあるので注意が必要です.温度によって粘度が変化しますので,塗型層の厚みを一定にしたい場合は,温度管理も重要です.3点目は「腐敗による性能劣化」です.水性塗型剤の場合は,菌が増殖し腐敗することによって,性状の悪化,強度低下などが発生します.
大事なことは,塗型剤自体の性状を管理し,一定の厚みが確保できるように粘度管理,濃度管理やボーメ管理を行うことです.次に塗布方法を統一し,製品の塗型層が一定の厚みになるように管理することで品質の安定につながると思われます.
(『鋳造工学』89巻12号掲載)
鉄材の湯流れ性がCE値の違いで変化することを現場で経験しました.なぜでしょうか? また,湯流れ性は一般にどのように測定して判断するのでしょうか.
湯流れ性(流動性)は,鋳込温度が高くなれば凝固時間(流動寿命)が長くなり,その間に流れる距離も長くなります.過熱温度(=鋳込温度-液相温度)と流動性との間にほぼ直線関係が成り立つことが,実験的に確かめられています.鋳鉄の場合,CE値の違いによって液相温度が低下すれば,鋳込温度を一定に保っても実質的な過熱温度が高くなり,流動性が増加することになります.流動性試験では,一般的に薄肉の試験鋳型に溶湯を鋳込んで自由に流れさせ,凝固によって停止した時の長さをもって流動性を表します.渦巻流動性試験鋳型が流動性を調べるためによく用いられていますが,これは流動溝が鋳枠の中に小さくまとめられていることや鋳型の水平度の影響が小さいためです.こうして得られた値は溶湯と鋳型の性質だけでなく,鋳型の形状,湯口方案などにも依存するので相対的な値ですが,流動性とは本来そういうものなのです.なお,流動性試験を行う時の注意事項として,1)鋳型条件,特に試験片部の肉厚と表面状態を一定にする.2)流入状況を安定にする.3)鋳込温度を正確に測定する,など細心の注意によってばらつきを小さくし精度をあげることが可能となります.
(『鋳造工学』90巻11号掲載)
塗型の塗り方が作業者によって異なるようですが,大丈夫なのでしょうか?【アルミニウムの重力鋳造や低圧鋳造の金型】
アルミニウム合金の重力鋳造や低圧鋳造では,金型の製品形状部表面に塗型を施します.塗型は,金型保護,溶湯保温,流動性確保,凝固制御,離型性確保,面粗度制御などに影響を及ぼし,鋳物の品質確保のために重要な役割を担っています.また,何度も繰り返して使用するため,塗型品質が変化して鋳物の品質に影響を及ぼすとともに,塗型寿命がばらつくと生産性にも影響を及ぼします.塗型は,一般的には手作業でスプレーして施工されることが多いですが,熟練者が施工してもばらつくことがあり,その技術伝承は最も困難なものの一つになっています.そこで,塗型施工時のいろいろな条件を洗い出して,塗型に影響を及ぼす因子を明らかにし,最適な条件を決めたりするような活動を行い,施工方法を作業標準などで規定したりして,ばらつきを少なくしています.将来は,作業者に頼るだけでなく,ロボットなどを使って施工して塗型品質を確保することや,ダイカストのように塗型ではなく離型剤をショット毎に吹き付けることで,塗型に頼らない鋳造技術を開発することが望まれます.
(『鋳造工学』89巻12号掲載)
K値の算出方法について,文献等には「K値=全介在物数/観察試片数」「2破面をもつ試片を1片と数える」と載っています.では,短冊状平板を5~6片に割った両端の試片は、片側1破面しかないので評価対象外となるのでしょうか? 片側のみの破面でも使用しても良いのでしょうか?
Kモールド法における試料採取では、短冊状試料を2本以上採取し、各試料から両側に破面を持つ観察用試片を5片以上採取し、合計10片以上としてK値を計算します.
ただし、片側のみの破面でも使用して結構です.湯口部、先端部等を使用する場合はどうしても片側しか破面が出ていないので、この場合は必ず0.5片として計算してください.
したがいまして、お答えとしては“片側のみの破面でも使用してよい.ただし、0.5片としての扱いにする.”ということになります.
実作業においては、上記のような,片側だけにしか破面が得られない短冊状試料の両端部を使用しなくても良いように、両側に破面を持つ試片が5片得られるような破断作業をおこない、各短冊状試料からの試片5片ずつを束ね、これを2試料分、2束での介在物数合計を求めた結果から、1試片あたりの介在物数“K値”を算出する方法が一般的です.
ただし、粘性が高い合金や溶湯温度が低い合金溶湯の場合など、流動性が悪い溶湯から試料を採取せざるを得ない場合では、健全な短冊状試料が得られず短くなる場合が多いので、上記のような片側のみに破面がある試験片を使用せざるを得ないでしょう.
(『鋳造工学』90巻11号掲載)
CV鋳鉄はFC(片状黒鉛鋳鉄)とFCD(球状黒鉛鋳鉄)の両方の特性を持っていますが,あまり普及されていません.どうしてでしょうか?
FCVは,コンパクティッド・バーミキュラ鋳鉄(芋虫鋳鉄)と呼ばれ,高強度のFCD(ダクタイル鋳鉄)と被切削性に優れたFC(片状黒鉛鋳鉄)のイイトコ取りとして注目され,現在量産品では油圧バルブ,ディーゼルエンジンブロック,フライホイール,エキゾーストマニホールド,高級鍋にも使われていますが,生産量が伸び悩んでいます.その理由は下記4項目にあると思われます.
1.材質の正しい理解とそれにあった設計ができていない
部品の要求品質を設計者が高強度と被切削性の両方を過度に期待すると,強度イマイチなのに切削性が悪いという事になります.つまり材料の特性を十分知ったうえで適材適所設計しないと結果的に不満が残ります.
2.製造条件の難易度が高い
注湯前にS wt.%を把握し,それに応じた球状化剤を毎回調整する必要があり,このさじ加減を誤ると,グラファイト形状が球になりすぎたり,片状になり過ぎたりする.つまり,フィード・フォワード管理が必要となり,この管理が面倒です.
3.品質保証が難しい
工程内検査では,通常行っているφ20テストピースでの全鍋ロット毎チェックが必要となります.さらにフェーディング時間が短く注湯時間制限があるので,出荷検査では量産品のエンジンなど重要部品の出荷品は,全数超音波測定による保証を行っている会社も有るが,費用対効果的には売価の高いものしか成立しません.
4.意外に知名度が低い
設計者が材料を選定する際,FCVの存在を知らずにいることが多い.薄肉にしてアルミ部品からの呼び戻しも可能です.このため鋳物屋から積極的に開発提案型で顧客に積極的に売り込むことも必要です.
(『鋳造工学』90巻3号掲載)
実際の鋳物では指向性が取れていてもひけ巣が発生することがあります. ちょうどいい指向性というものはあるのでしょうか?
凝固時のひけ巣発生の主要因として、溶湯の体積収縮と溶湯に溶け込んだガスが挙げられます。熱は鋳型の内部から外側へと流れることから、鋳型に流入した溶湯は外面が早く凝固し、内側の凝固は遅れることになります。金属は凝固時に数%程度の体積収縮が発生するため,凝固に伴う体積収縮分は、溶湯補給がない限り、ひけ巣として空洞が発生してしまいます。また、溶湯には雰囲気などのガスが溶け込みやすく,温度が下がると固溶限が低下するため、溶け込んだガスは固溶できなくなり、気体として放出されることから、ひけ巣とともに空洞を形成する場合もあります。
これらの対策として鋳造方案を工夫し、押湯の設置や鋳型の温度制御などで指向性凝固を確保した場合には、温度が高い方向から低い方向へと溶湯の補給を確保することにより、特定範囲でのひけ巣を防止することができます。しかし、中心線ひけ巣のように指向性が弱い場合、あるいは発生したガスの逃げ場がない場合には、空洞が製品内に残ってしまう場合もあります。
したがって、凝固パターンと発生したガスの逃げを考慮した鋳造方案の立案、そして溶湯自体のガス量を抑制する、これら両面から対策を施すことが必要となります。
(『鋳造工学』90巻3号掲載)
チクソキャストのメリットとデメリットは?
チクソキャストは固液共存温度範囲の広い合金を使って,固相率を温度により制御したスラリーを鋳造する半凝固鋳造法です.あらかじめミクロ組織をチクソトロピーが強い状態にしておくと,静かな状態では固態ですがせん断力がかかると大きな流動性が現れます.チクソトロピーというのはせん断速度が上がると流動性がどんどん現れるという性質です.この流動性を利用して半凝固でも鋳型への充塡が可能な鋳造法です.工業的にこのチクソキャストを行う場合,チクソトロピー性が高くなるビレットを予め作製しておき,このビレットを一度半溶融状態まで温度を上昇させた後,このスラリーを鋳造機で金型に射出成形します.
チクソキャストには急速加熱かつ正確な温度管理をする設備と圧力鋳造の設備が必要です.また,合金を選ぶというのもデメリットです.固相率が高すぎると圧入できないし,低すぎるとメリットはありません.合金を選ぶというのはこの固相率の管理が温度で簡単に行えないと品質の安定が難しいということです.また,構内での材料リサイクルが難しい点もデメリットになります.一度凝固してしまうとチクソトロピーの強い状態ではなくなります。
品質的なメリットは鋳造用の鋳型で鍛造に近い品質が得られるということです.すでに固相がある分だけ凝固収縮は少なく巣の発生が少ないのです.さらにスラリーは液相よりも粘性が高いため乱流になりにくく,射出成型時に空気の巻込み欠陥が減少します.同時にプロセス温度の低さはそのまま寸法精度の高さに結びつきますし,それはそのままサイクルタイムの短縮につながります。従来のような溶解設備をなくすことも可能ですし、熱衝撃の低下により金型寿命も延びるというメリットの多い鋳造法です.
(『鋳造工学』88巻12号)
「炭素当量」の出自は?同じCE値でもC%が高い時とSi%が高い時の溶湯の特性を共晶凝固と共析変態過程及びひけ傾向について教えてください.
炭素当量(Carbon Equivalent:CE )とは鋳鉄中のSi,P量の影響の度合を⊿関数1)で示すC %として表し,これと実際の鋳鉄中のC%との和の値で,次の(1)式で表すことが多くあります.
CE=C%+(Si%+P%)/3.2 (1)
ここでの⊿関数は,溶融Fe-C合金に添加される第3元素が炭素の溶解度に与える影響,さらには炭素の活量の増加又は減少,つまり炭素を黒鉛あるいはセメンタイトとしての晶出のしやすさを関数化したものです.その詳細は最近出版された図書2)にわかりやすく解説されています.共晶凝固,共析変態過程及びひけ傾向に関して,同じCE値でもC%又はSi%が高い時の影響を考えてみましょう.まず,共晶凝固及びひけ傾向の場合,C% が高ければ高いほど,Cの活量が高くなり黒鉛として晶出しやすく,黒鉛晶出量も多くなると考えられます.よって,ひけが小さくなる傾向になります.
一方, Si%が高くなればなるほど, Cの活量が増加しますが溶湯への溶解度は減ります.そのため,黒鉛の晶出量は減少します.Si%が高すぎる溶湯は,ひけやすくなるという鋳造現場の経験は少なくありません.
共析変態過程の場合,同じCE値でもSi%が高い時,共析変態点は高温側に移動し,かつ変態温度が一定温度ではなく,ある温度範囲にわたって進行します.この共析温度範囲内ではオーステナイト,フェライト及び黒鉛の3相共存になることが特徴です.鋳鉄を熱処理するとき,この点に留意する必要があります.
1) F.Neumann, H.Schenck, W.Patterson:Giesserei Tech.-Wiss.Beih.,23(1958)1
2)例えば,日本鋳造工学会編:新版 鋳鉄の材質(日本鋳造工学会)(2012)10
(『鋳造工学』88巻12号)
マグネシウム合金は自動車の軽量化では優れていますが,精錬で大量のCO2を排出するそうです.どんな精錬方法でどれだけCO2を排出しますか?
現在マグネシウム精錬方法としては2種類の方法が主流で,熱還元法と電解法があります.
熱還元法の原材料は主にドロマイト(MgCO3*CaCO3)Mg含有量13%が使われています.
電解法では前記ドロマイトの他にカーナライト(MgCl2*KCl*6H2O)8.8%等が使われており,前処理方法により途中で発生するCOやCO2量の違いがあります.技術の進歩により前処理や精錬で発生するCO2量は削減されていますが,熱還元法では凡そ42 ㎏CO2/㎏ Mg ingot 電解処理では21 ㎏CO2/㎏ Mg ingot程度と言われています.電解法で電力に水力発電や原子力発電を使うと更に排出するCO2量は削減されます.現在,マグネシウムの主な生産国は中国で,その主流の精錬方法は,熱還元法の一つであるピジョン法が用いられています.そのため,今後,マグネシウム精錬の一層のCO2削減技術が望まれます.
(『鋳造工学』91巻5号掲載)
青銅よりも黄銅の方が湯が回りやすいのはなぜですか?
黄銅系の合金は凝固温度範囲が狭く,表皮形成型の凝固形態となり,青銅系の合金は凝固温度範囲が広く,粥状の凝固形態となることが知られています.表皮形成型の凝固形態となる合金では,流動中に鋳壁から凝固層が成長し,流路を閉塞することで流動が停止します.一方,粥状の凝固形態となる合金では,流動中に溶湯先端が冷却され固相が晶出し,その固相が流動限界固相率(おおよそ20~50 %と言われています)に到達すると流動を停止します.
これらの合金の流動性を半定量的に検討しましょう.表皮形成型の合金において,凝固層が流路を閉塞するまでの凝固時間をtfと表わしますと,粥状凝固形態を示す合金において溶湯先端が限界固相率になるまでの時間は0.2tf~0.5tfと表されます.溶湯の流速を一定値vとしますと,表皮形成型の合金の流動長はLf=vtf,粥状凝固型の合金の流動長はLf=0.2vtf~0.5vtfとなります.このことから表皮形成型の合金は,粥状凝固の合金と比較して2~5倍の流動長となることが分かります.このため,粥状の凝固形態を示す青銅合金よりも,表皮形成型の凝固形態となる黄銅合金の方が湯が回りやすいのです.
(『鋳造工学』91巻5号掲載)
アルミ合金鋳物を熱処理するとなぜ硬くなるの?
凝固点直下の高温で合金を保持すると,Alの結晶構造の中にCu,Mg,Si等のような他の合金元素の原子が均一に溶け込んだ“固溶体”状態になっています.このような状態にすることを“溶体化処理”と呼びます.この状態からゆっくり冷却すると,溶けきれなくなった合金元素が,CuAl2,Mg2Siなどのような安定した,光学顕微鏡でも観察できる程度の若干大きな結晶を形成し,Alの結晶構造の一部にこれらの結晶が分散した状態(“析出”状態)になります.この状態では析出物が大きいため合金はあまり強化されません.
ゆっくり冷却せずに,高温の固溶状態を水中への急冷処理(焼入れ)等の手段により室温まで同様の固溶状態を持越す処理を行います.この状態にされた材料を過飽和固溶体といいます.この後,図1に示すように,常温~200℃程度の温度に数時間~数日間(工業的には数時間)保持することにより,アルミニウム合金中に溶けている元素が微細に析出し,この析出物が転位の動きを止めるため,強度を高めます.このように合金が硬化する現象を“時効硬化”現象といい,このような処理を“人工時効処理”と呼びます.この現象を利用して,熱処理による強化を行っています.更に処理時間を長くすると安定した析出状態になり,軟化します.最高硬さ以前を“亜時効状態”,以降を“過時効状態”と呼びます.
アルミニウム合金鋳物で利用される代表的な熱処理とその記号,概要を以下に記します.
F :鋳造のまま
T4:溶体化処理後焼入れし,室温で自然時効処理を行う処理.
T5:人工時効処理だけを行い,若干強度を向上させたり寸法を安定化したりする処理.
T6:溶体化処理後焼入れし,人工時効処理をして最高強度の状態を得る上記説明の処理.
T7:T6と同様な処理を施すが,内部ひずみの減少,寸法安定化,高温特性の安定化等を目的とし,人工時効処理を若干高温あるいは長時間行い,過時効状態とする処理.
(『鋳造工学』第88巻第5号掲載)
黄銅は金型鋳造ができるのに青銅では難しいのはなぜですか.
生産性の向上,作業環境の改善といった観点から青銅の金型鋳造は昔から望まれてきましたが,多くの問題があり,実用化は進んでいません.
青銅系の合金は黄銅系の合金と比較して凝固温度範囲が広く,粥状凝固する合金です.凝固温度範囲が狭く,表皮形成型の合金である黄銅系の合金と比較して,固液共存の状態が長く続きます.そのため固液共存中に熱収縮が金型に拘束されると,引張荷重を受け,凝固割れを生じやすいという問題があります.
凝固中,デンドライトが発達するためひけ巣に対する押し湯からの溶湯補給も難しく,湯流れ性も黄銅系の合金と比較して良くありません.金型鋳造の場合,冷却速度も早いため,押し湯が効かずミクロポロシティや湯回り不良が問題となります.また溶解温度についても,黄銅系の合金と比較して,青銅系の合金は高く,金型寿命の問題もあります.
これらの問題に対して,金型材質の検討や,CAEによる熱流動凝固解析を利用した青銅合金の金型鋳造用の方案の検討等,更なる研究,技術開発の進展が待たれます.
(『鋳造工学』91巻10号掲載)
鋳造現場では,熱分析曲線を用いてC%,Si%を判断していますが,どのような原理でこれらの含有量を出しているのでしょうか?
図1に示すように,溶湯の熱分析を行うCEメーターのカップには,チルさせてセメンタイト共晶温度を測るテルル(Te)入りカップと,カップ内に何も入っていないタイプのカップの2種類があります.また,黒鉛共晶温度を測るための接種剤入りカップなどもまれに使われます.Si値を測定する目的のテルル入りカップでは全チルになるため,初晶温度とセメンタイト共晶温度は測られますが,溶湯性状を判定することはできません.それに対して,何もなしカップを使って,溶湯性状を判定することが行われています.
図1 カップの種類と共晶温度の関係
図2に示すように,Si量とセメンタイト共晶温度の間には,[セメンタイト共晶温度=1142.6-11.6×Si量]の関係があります.一方,図3に示すように,C量を変えても,一般的な鋳物の成分範囲(2.9~4.2%)では,セメンタイト共晶温度は変わりません.よって,セメンタイト共晶温度を測定することにより,Si量を推定できます.例えば,セメンタイト共晶温度が1120℃ならば,Si量は約1.95%になります.
図2 Si量とセメンタイト共晶温度の関係
図3 C量とセメンタイト共晶温度の関係
Te入りカップの初晶温度より,炭素当量(CE)が分かります.この炭素当量を現場管理の範囲として使用し,無理にC%を出さない会社も多くあります.炭素当量からCを求める計算式としては,CE(=C+(1/3)×Si)またはCEL(=C+0.23×Si)が用いられています.いずれにおいても,セメンタイト共晶温度から求めたSi量と,初晶温度から求めた炭素当量より,C量が推定できることになります.ただし,セメンタイト共晶温度はCrなど他の元素によっても変化するため,正確にはそれらの元素も考慮する必要があります.
(『鋳造工学』89巻8号)
接種する事で組織が微細化され強靭になると言われるのはなぜでしょうか? 共晶セルを微細化すると結晶粒界の面積が増加するので,微細化しない方が引張強さは強いのではないでしょうか?
強靭化の度合にもよりますが,接種の効果も強靭化の一因子です.とは言え高強度で高延性を得られるかといえば,黒鉛化促進接種剤では延性向上を期待できますが,強度は低下し,パーライト促進接種剤を使えば逆となります.ご存知のように鋳鉄の機械的性質は,黒鉛組織に大きく依存し,同等ならば,基地組織のフェライト(α)/パーライト(P:α+共析Fe3C)率に依存しています.接種は,鋳鉄の凝固及び共析変態時のミクロ組織に大きな影響を及ぼし,その結果として機械的性質を改善しています.
次に共晶セル数が増加すれば,結晶粒界が増えるのは確かですが,含有する元素の偏析や反応生成物は分散化・平準化されます.そして,鋳鉄の強度は主に基地の連続性(有効断面積)に依存していることが実証されています1).鋳鉄は多結晶でα基地の場合,塑性変形(すべり)して破断するので必ずしも粒界が弱いとは言えないでしょう.また,微細化により強度が上がるのは,夫々の結晶ですべり方向が異なり,すべりの先端が隣り合う結晶の粒界で止められる回数が増えるためです.理論的には,ホール・ペッチの関係式:σy=σo+k/d1/2(σy:降伏応力,σo:結晶粒内の転位を運動させるのに必要な応力,k:結晶粒界による強化の比例定数,d:結晶粒径)に纏められています2).
1) 鋳鉄の科学、中村幸吉他著、社団法人日本鋳物工業会(2005)150
(『鋳造工学』91巻10号掲載)
金属材料の疲労限度を知りたいのですが,簡単に調べる方法はありますか?
一般に疲労限度は,疲労亀裂の発生に起因すると言われており,疲労亀裂の発生は材料のすべりに対する抵抗値(降伏点)に依存することが知られております.疲労試験は多くの試験片本数と試験時間を要するため,疲労限度の簡便な推定方法として,引張強さや硬さから推定することが多いようです.例えば,鉄鋼材料の回転曲げ試験の場合では,疲労限度σ_w(MPa)は下記のように引張強さ”σ” _”B” (MPa)やビッカース硬さHVから推定することができるようです1).
σ_w≅0.5″σ” _”B”
σ_w≅1.6″HV”
これらの式は,引張強さが1100MPa以下,ビッカース硬さで400以下の範囲で成り立つとされています.これ以上の強さや硬さを有する材料の場合,材料中に存在する介在物などの影響を受け,危険側の評価になりますし,誤差も大きくなります.
例えば,鋳鉄の場合,ねずみ鋳鉄では片状黒鉛の切欠き効果による影響を受け,上記の推定式から求めた疲労限度よりもかなり低い危険側の推定となります.一方,球状黒鉛鋳鉄では,基地組織の硬さと疲労破壊の起点の大きさに依存します.基地組織がフェライトなど軟らかくかつ靱性が高く,欠陥の大きさがそれほど大きくない場合,上式でも良好な推定が行えることが報告されています.ただし,上式は基地組織の硬さや欠陥寸法に依存し,ある値を超えると危険側の推定となります.疲労限度は引張強さや降伏点などの静的強度とは直接的に関係づけられるわけではなく,本質的には強化機構(固溶強化や析出強化など)を考慮して検討すべきものであり,そのような式も提案されています2).要は,その材料の疲労特性が推測可能な材料であるかどうかが問題になってくると思います.
疲労限度は試験片寸法や試験条件などの影響も受けることが知られておりますので,安全側の設計を行うのであれば,簡便評価による手法よりも疲労試験を行うのが無難と言えます.
1) 村上敬宜:金属疲労 – 微小欠陥と介在物の影響, 養賢堂, (1993)
2) 阿部隆 ほか:鉄と鋼, 70(1984), 1459
(『鋳造工学』87巻12号掲載)
軽量化のためにマグネシウムダイカストを使用したいと思っています。エンジンのそばの部品のカバーですが、どのようなことに注意して設計すれば良いでしょうか?
マグネシウム合金は実用金属の中で最も軽量な金属であり,鉄鋼材料やアルミニウム合金からの置き換えで,軽量化を図ることができます.しかし,機械的性質などの材料特性が異なるため,注意する必要があります.カバー類であれば,一般的にAZ91D合金が用いられます.しかし,AZ91D合金においては高温クリープが生じ,耐熱性がアルミニウム合金などに比較して劣るため,その部品の温度環境により材料選定をする必要があります.150℃を超える温度となるような部位への適用であれば,AS系などの耐熱性の高い合金を選定しなければなりません.また,ヤング率が低いため,剛性向上のためにリブなどを設置する必要があります.マグネシウム合金自体の耐食性は高いですが,他の金属と接触するとガルバニック腐食を起こすため,塗装等で接触面を絶縁するような構造にする必要があります.
一般的なダイカスト用アルミニウム合金のADC12と比較すると,凝固温度範囲が広く,ひけ巣や凝固割れが生じやすくなります.できる限り肉厚差をなくすような設計を行い,鋳造欠陥が出にくい形状とすることが重要になります.
(『鋳造工学』87巻12号掲載)
鋳鉄溶解炉としてキュポラが誘導炉に変わってきていますが,その理由は?
キュポラが誘導炉に変わってきた理由は企業の操業環境によって違うと思いますが,その代表的なものを紹介したいと思います.
一つ目は,キュポラはコークスを燃焼させ連続的に溶解,溶湯を作る設備であることです.連続操業の場合には適していますが,生産量の減少に伴い稼働調整(間欠操業)をしようとしても,溶湯は連続的に生成されるため,一時的に溶湯を保持する設備(電気炉)が必要になります.いわゆる<生産変動に応じた操業がしづらい溶解設備>という点です.
二つ目は,原材料である銑鉄,鋳物用コークスは大半が輸入に依存しており,市場の変動の影響を受けやすく,供給ネックや価格不安定さを抱えるなど<工場経営リスクが高い>という点です.
最後に,廃棄物(脱硫スラグ)処理という課題です.球状黒鉛鋳鉄を生産する場合には,コークスから混入する代表的な不純物である硫黄を取り除く処理(石灰石などの造滓材を添加)が必要で,この生成する脱硫スラグが廃棄物となり<地球環境課題対応(廃棄物低減)が必要>になるという点です.
このようにキュポラを用いた溶解は,操業条件に多くの制約があるため,電気誘導炉への移行が進んでいるようです.
更に,2015年7月,我が国は2030年までに温室効果ガス(CO2)を26%削減(2013年比)することを国連に宣言,この目標達成のために製造業は温室効果ガスを40%削減する必要があるとも言われています.このような企業を取り巻く環境変化を受けて,コークスに比べCO2排出量が少ない電気誘導炉への転換が加速するのではないでしょうか.
(『鋳造工学』88巻10号)
ねずみ鋳鉄の鋳物内で,A型黒鉛にD型黒鉛が混在していますが,なぜですか?
図1に,A型黒鉛にD型黒鉛が混在する組織写真の一例を示します.このような組織になる要因として,以下のことが考えられます.
- 接種が効かなかった可能性があります.接種剤がうまく溶けなければ,黒鉛の核が少なくなってすぐフェーディングするために,D型黒鉛になると考えられます.
- D型黒鉛は過冷された溶湯に表れやすいと言われています.一方,(a)硫黄/マンガン(S/Mn)の比率,(b)燐(P)の含有量,(c) R/G(冷却速度/凝固速度),等が増加すると,過冷度が大きくなります.その結果,D型黒鉛が現れ,A型と混在するようになると考えられます1).
- 最終凝固部に低沸点元素(例えば,アンチモン・鉛・テルル等)が逆偏析すると,溶湯が過冷されやすくなり,よってD型黒鉛になる可能性があります2).
1)Recent Research on Cast Iron:American Society for Metals(1964)438-445
2)米国鋳物協会編,日本鋳物協会訳:鋳物不良の原因と対策,丸善(1955)140-141
図1 A型黒鉛にD型黒鉛が混在する組織写真
(『鋳造工学』92巻1号掲載)
アルミニウム合金は高周波誘導炉で溶解できるのですか?
アルミニウム合金は高周波誘導炉で溶解できます.溶解速度も速く,短時間で高温にすることができます.溶湯温度の安定性も良好です.アルミニウムの場合,融点が低い合金が多く,電気ヒータでも十分であり,高周波誘導炉を導入する必要性が少なく,装置が高価なため,アルミニウム関係の量産現場ではあまり見られません.研究機関等で実験用の小型高周波誘導炉を使用している場合があります.実験炉としては,溶解速度がはやく,非常に便利です.
(『鋳造工学』88巻10号)
「魔法のフライパン」や「南部鉄器」などの良いといわれる調理器具の鉄の組織とはどういうものでしょうか.また,急須やフライパンなどはなぜ表面が黒いものが多いのでしょうか?
一般的な調理器具として使われる「南部鉄器」の組織として,白鋳鉄は避けなければなりません.その理由として,繰り返しの熱により,器具が割れたりするためにチル化した組織にならないように注意します.したがって,一般的な組織は片状黒鉛鋳鉄です.しかし,最近は電磁調理器等の使用により,さらに熱ショックに強い南部鉄器が望まれてきています.また,重いということで,薄肉で強度のある球状黒鉛鋳鉄を用いた調理器具が多く使用されています.
色については,昔より「南部鉄器」の調理器具には「漆」が塗られて,黒が基調となりそのなごりが残っています.最近の南部鉄器の調理用塗料としては,シリコン系の樹脂塗料やカシュウ(漆系の合成樹脂塗料)で着色されています.食品衛生法や耐熱性の樹脂の関係で,調理用塗料として適さない色もあることや,黒色は高級感があるということで使用されています.
(『鋳造工学』92巻12号掲載)
生型からシェル鋳型に変更したところ,バリが増えました.どのように対策したらよろしいでしょうか?
バリは砂型の寸法精度が悪いと発生します.工法を変更したことにより,砂型の寸法が変化したことが推察されます.特に,シェル鋳型ですと加熱をしているため,造型時に熱変形をして,砂型の寸法が変化し,バリが発生することが懸念されます.また,鋳造時に溶湯圧力で,中子や上型が浮き,バリが発生することもありますので,中子はしっかり固定し,上鋳型上に重りを載せるなどの対策も必要です.
(『鋳造工学』90巻7号掲載)
コールドボックスで使われるアミンガスは人体に有害と聞いているのですが,工場で感じる臭気レベルでは人体への影響はないのでしょうか.
コールドボックスは,1966年米国アシュランド・ケミカル社によって有機バインダによるガス硬化鋳型造型法を発明し,1968年に技術導入,1969年に実施許諾によって普及が開始され,1989年に基本特許が権利満了となっています. 実に半世紀以上に渡って使用されている鋳型造型プロセスとなります.
コールドボックスに使用されるバインダは,
Part1 ・・・・ フェノール樹脂
Part2 ・・・・ ポリイソシアネート
の2液から成り立ち,このバインダを砂と混錬して型込めし,触媒である第3級アミン(トリエチルアミン)を通気することによって硬化させる造型法です.ここで使用されるトリエチルアミンですが,健康有害性の急性毒性(吸入:蒸気)が区分3に該当し有害です.
この有害性は,急性毒性の吸入によって動物(ラット)試験されており,ラットLC50(4時間)値:1250ppm(換算値5.163mg/L)および2600ppm(換算値:10.74mg/L)となっています. この値は,試験におけるラットの半数以上が死んだ値となります. この数値に基づき工場の作業環境濃度は,この数値以下で管理することが大切で,きちんと換気された鋳造工場であれば,この数値以下となりますので,人体への影響は少ないと考えらます.
(『鋳造工学』92巻12号掲載)
アルミ材料の特徴としてリサイクルできるということですが,リサイクルの方法にはどのようなものがありますか?
アルミニウムに限らず,ほとんどの金属はリサイクルが可能で,地球環境にやさしい材料といえます.アルミニウムはボーキサイトを原料として,多大な電力を必要とする電解製錬によって製造されます.しかし,アルミニウムスクラップを溶解・再生するときのエネルギーは,新地金を製造するときのエネルギーの3.3%といわれており,リサイクル性に優れた材料です.
アルミニウムスクラップのみを分離できれば,溶解し,成分調整することにより,再生アルミニウムとして使用することができます.しかし,自動車部品のようにアルミニウムだけでなく,種々の材料を組み合わせて使用している場合には,アルミニウムとそれ以外の材料を分離し,さらにアルミニウムの展伸材と鋳物・ダイカスト材に分離する必要があります.
自動車部品を例にとると,解体業者で,エンジン,トランスミッション,ラジエータ,フードなどの主要なアルミニウム部品が取り外された後,シュレッダ処理されます.シリンダブロックやフードのように,材質がわかっているものについては,ボルトなどの異種材料や塗装をとった後,それぞれの材料に再生します.
シュレッダラインでは,鉄と非鉄金属との分離のために,風力選別,磁力線別,渦電流選別,比重選別などが行われています.シュレッドスクラップから展伸材と鋳物・ダイカスト材の分離技術については,種々の方法があります.成分の相違に起因する融点差を利用したホットクラッシュ法,薬液との化学反応に伴う発色性の差異を利用したカラー選別法,レーザ誘導型発光分光分析を用いるレーザ選別法,2種類のX線を用いるX線選別法などがあります.
詳細な技術内容については,下記の文献を参考にしてください.
大瀧光弘:軽金属 59(2009) 612
(『鋳造工学』90巻7号掲載)
光学顕微鏡で炭素鋼を観察すると黒と白の模様が現れます.どうしてフェライトは白く,パーライトは黒い縞なのでしょうか.
組織観察を行うためには,一般に落射照明による明視野の光学顕微鏡(金属顕微鏡)を用います.試料を鏡面研磨した状態で光学顕微鏡で観察しても金属組織は現れません.試料表面に当たる光が均一に反射されるためです.そこで組織を見るためには,結晶の構造によるわずかな反射の違いによるコントラストをつけるために,試料に微細な凹凸をつけることが必要です.この作業を「腐食(エッチング)」と言います.図1(a)に示す一様なフェライト組織を腐食させて観察すると,同じフェライト組織でもわずかに濃淡が見られます.これは,フェライト組織が一様に腐食されるのではなく,フェライトの結晶方位の違いにより腐食の程度にわずかな差が生じ,表面状態がわずかに異なるためです.腐食量のわずかな高低差による影が,結晶粒界として観察されます.
図1 エッチング後の組織観察
一方,パーライト組織とは,軟らかいフェライト相(α-Fe)と硬くて脆いセメンタイト相(Fe3C)の共析組織です.パーライトにおけるフェライトとセメンタイトの割合は,およそフェライト89mass%,セメンタイト11mass%ですので,薄いセメンタイト層の間にフェライト層が存在することになります.図1(b)に示すように,エッチングを施すとセメンタイト相よりも腐食しやすいフェライト相が優先的に腐食され,パーライト組織ではセメンタイト相が山に,フェライト相が谷になります.低倍率の光学顕微鏡でこれを観察した時,パーライト相はセメンタイト相の影により黒灰色または層状に見えます.高倍率で観察すると,パーライト相のフェライト層もセメンタイト相も反射して白っぽく見えますが,黒い縞模様が観察されます.この黒い縞模様は層になった凸状のセメンタイトの影を見ていることになります.
(『鋳造工学』92巻6号掲載)
鋳鉄を勉強すると出てくる鉄-炭素二元平衡状態図は、どんな時にどのように役立つのか?
状態図と熱力学のエリンガム図及び元素周期律表は、鋳造における3種の神器とも言われているものである.状態図はある化学組成と温度でどのような状態(相または組織)になるかを教えてくれる.
Fe-C状態図(下図)は,他の合金の状態図では見られない特殊な現象がある.それは、点線と実線の2つの状態図が一緒に書き込まれている点である.実線(準安定系)からは凝固時にチルが,点線(安定系)からは黒鉛が出る(晶出)からである.なお、準安定系を実線にした理由は,鋼の状態図が先に作られ,遅れて横軸を炭素当量(CE)とした鋳鉄の状態図が出来たからであろう.
さて、本題に入ろう.Fe-Cの状態図は以下のようなことを判定する場合に役立つ.
- 鋳物が固まる温度が分かる.例えば, FC300(下図↓)は,約1250℃程度で固まり始め, 1153℃付近ですべて固まる.
② 鋳物の基地組織が予測できる.例えば、730℃以上ではオーステナイト(γ)に、それ以下ではフェライト(α)とセメンタイト(Ce)になる.
③ てこの原理を用いて,高温の液相(液体)から凝固までの固相と液相の割合(この場合γ量と液相),共晶凝固温度(1153℃と1147℃)から共析変態温度(A1:738℃と727℃)直前までは固相(γとGあるいはCe)の割合とγ中の炭素濃度が分る.A1域過時にγが分解・消失しフェライト(α)とGあるいはCeになり室温に至る.各相(組織)の割合や組成(C%)を読み取ることができる.
④熱処理を行う温度の予測ができる.
⑤ 実線の共晶凝固温度と過冷反転温度から、溶湯のチル化傾向を判断することができる.
他にも、状態図には多くの情報が隠れており,有効に活用すれば、健全な鋳物づくりに役立つ.
(『鋳造工学』89巻1号掲載)
マグネシウム合金鋳物をアルミニウム合金鋳物の代替材として使用する際のメリットとデメリットは
マグネシウム合金鋳物の最大のメリットは,何と言っても実用金属材料中,最軽量という点です.良く用いられるマグネシウム合金鋳物にはAZ91合金ありますが,比重は1.82となりアルミニウム合金材の約2/3になります.そして,軽量であることから比強度(強さ/重量)も実用金属材料中最も大きな材料です.軽量以外のメリットとしては,振動エネルギー吸収しやすく高い減衰能や制振性があること,衝突時に発生するくぼみが小さく耐くぼみ性が高いこと,切削抵抗がアルミニウム合金の約1/2と小さく切削性が良好なことなどが挙げられます.
一方,デメリットとしては,マグネシウム合金は活性なため大気中でも酸化しやすく,アルミニウム合金鋳物と比較してもかなり耐食性が悪いことです.特に,屋外等で使用する場合,実用金属中最も耐食性が低い材料です.また,容量の大きいマグネシウム合金鋳物自体は容易に燃焼することはありませんが,機械加工などにより細くなった切粉の取り扱いについては特別な注意が必要です.火災による災害は,機械加工中の微細なマグネシウム片に起因することが多く,また,湿ったマグネシウム粉は可燃性の水素を発生しやすくなります.加えて,溶融したマグネシウム合金は非常に活性なため,溶解時には燃焼しやすく大気との遮断が必要になります.
(『鋳造工学』89巻1号掲載)
ねずみ鋳鉄FC200(JISG5501)で,別鋳込み供試材の規格がφ30に制定されているのは機械試験に使用するためでしょうか? 8B試験片にてφ20で鋳造し,φ12.5で引張試験を行うのは間違っていますか?
鋳鉄の引張強さは黒鉛量,炭素飽和度(Sc),肉厚などによって変化します.試験片の直径が小さい場合は,その鋳物の冷却速度が大きなり,引張強さは増大します.そこでJISなどでは,片状黒鉛鋳鉄の標準強さは直径30mmの試験の値で表示しています.また,炭素飽和度による引張強さの基準値としてσnを求め,実際に求めたφ30の試験片からの引張強さをσtとし,これとの比率をとって,成熟度RG=(σt/σn)×100を求めています.試験片の肉厚をφ30と統一することで,成熟度が100%より大きいほど材質が良好と判定できます.
φ20で鋳造した試験片の引張強さは,φ30で鋳造した試験片の引張強さよりも大きな値となるので,その場合の使用用途としては,規取引先との間で,「引張試験片は,φ20に鋳造した別鋳込み供試材とする」などと取り決められているような場合が想定されます.
参考文献:新版 鋳鉄の材質,日本鋳造工学会(2014)35-36
(『鋳造工学』90巻12号掲載)
マグネシウム合金の溶解作業で注意すべき点はなんでしょうか? カバーガスなどは何を利用すればよいのでしょうか?
まずはいつでも消火できる準備をすることが第一だと思います.溶解量にあった砂やフラックスなどの消火剤を準備してください.坩堝と炉蓋には隙間がないようにし,カバーガスによって炉内が常に正圧である事を確認してください.溶湯表面積を少なくするために,坩堝は胴長のものを使用し,坩堝の内面は酸化チタン等でコーティングして,坩堝から鉄分の溶出を抑えると良いでしょう.坩堝の加熱面は湯面より低くするとカバーガスの分解抑制と坩堝壁の燃焼を抑えられます.
湯を激しく撹拌すると,湯面の酸化被膜を溶湯中に巻き込んで容易に汚染されるので,必要時以外,溶湯には触れないこと.溶湯は容易に水素を吸収するので,鋳造直前にガスバブリングにより脱ガスするのが好ましいです.連続溶解の場合にはインゴットの表面を酸化させないことも重要です.重力偏析する合金も多々あるので,坩堝側面を加熱して自然対流を促進することも重要です.
カバーガスについては,経験の少ない人はSF6+CO2混合ガスが一番扱い易いのでお勧めです.温暖化効果ガスですが少量であれば問題ないでしょう.馴れてきたら温暖化係数の低いガスを試してください.
(『鋳造工学』90巻12号)
ヨーロッパでは30年前からワイヤー球状化処理が用いられていますが,日本では最近どうなっているのでしょうか?
日本でも近年,鋳鉄の球状化処理のためにワイヤー法が注目を集め,採用,または導入を検討する鋳物工場が増えています.それには下記の理由があると思います.
第一に『処理装置の発展』です.爆発的な球状化処理反応にも耐えうる装置が開発されMgワイヤーのHi-Mg化が進みコスト低減可が進みました.第二に『作業環境の改善』です.作業現場改善への意識が年々高くなってきています.また労働者確保のためにも働きやすい環境が求められる時代へと移り変わっています.ワイヤー法であれば球状化処理時に局所集塵が可能となりMgの煙が工場内で蔓延することはありません.また球状化剤,カバー材を処理鍋にセットする必要がなくなり,労働者の負荷低減にも繋がります.第三に『送線技術制御の発展』です.パソコン技術の進歩により比較的安価に様々な制御が可能となりました.また送線履歴,異常履歴等が自動保存されトレーサビリティが容易となっています.
しかし全てにおいてMgワイヤー法が優れているわけではありません.球状化処理の特徴をよく理解し,工場の将来像を見据えた操業に最も適した処理方法を選択していくことが理想といえます.
(『鋳造工学』90巻4号掲載)
実家に鋳物師職の許可書があり,今までの軌跡を記録に残そうとルーツや歴史を調べています.しかし,この許可書の意味がよくわかりません.どういうものでしょうか.
明治時代の初めまで「鋳物師職許状」というものがありました.これについては多くの方々の研究記事と歴史記念館に残された古文書を見ることができます.本会の鋳物の科学技術史研究部会編「鋳物の技術史」(1997年3月発行)にも記述があります.
鋳物が普及し,技術も定着するにつれて,独占的に製造し販売する権利を得て,他のものの参入を制限しようとする動きがでてくるのは鋳物だけでなく,その他の職業においても自然の流れであったようです.特権を与えることは古くから行われていたようですが,鋳物においては,京都の公家で古くから鋳物師との間で特別な関係があった真継家の17代久直が朝廷の権威を背景に16世紀の中頃に鋳物師の全国組織の構築をてがけ,鋳物師支配のしくみづくりに動きました.17世紀の終わりごろには24代珍弘は「鋳物師職許状」の発給などで鋳物師支配の拡大を進めました.徳川家などでは「朱印状」を授与したりして特権を与えていたようで,幕府の影響力が強かった江戸,京都,大阪では真継家の「職許状」などによるしくみに賛同する鋳物師ばかりではなかったようで,はじめは地方の鋳物師に限られていたようです.鋳物消費の拡大に伴い,鋳物師も増え,市場をめぐる争論も発生すると,朝廷の後ろ盾による特権を持つ鋳物師にとって営業権を保証されることは有利であったことから真継家の支配下に属すようになり,徐々に拡大されてきたようで,各地に「鋳物師職許状」が残されています.石川,富山,新潟,群馬,千葉などの歴史資料館などで見られ,また,研究記事も多く発表されているようです.鋳物業に古くから携わってきた鋳造企業にはこの職許状が残されている企業もあります.跡目を継ぐと新たに発給を受けていたようで,新規に発給されると前の許状は返納されていたとのことで,各地の鋳物師も多かったようですが,現存するものがその割に少ないのはそのためのように思われます.
鋳物師代替わりの際に発給された許状には「当該鋳物師がその職を先代から引き継がれていること.組織されている座の規則を守るべきこと」などが記載された短文のもので,鋳物師からの申請によって,真継家代々の当主よりその鋳物師に与えられていました.初期のものは別として残されている職許状はほぼ同内容の文面で真継家朱方印と当主の署名花押により作成されています.
「職許状」を得ている者は当時としてはかなりの冥加金を真継家に納める必要があったようで,得られた鋳物師は限られていたようです.幕府はこのしくみを認めていなかったようで,鋳物師には真継家の配下のグループ,江戸,京都など真継家と関係を持たなかったグループ,真継鋳物師配下にありながら登録されていなかった者,その他のグループがあったようです.明治維新となり,明治政府がこのしくみを認めなかったことから,まもなく発給されなくなり,真継家およそ300年の鋳物師支配は終わりを告げ,それ以降,鋳物師職許状は姿を消しているとのことです.
(『鋳造工学』90巻10号掲載)
マグネシウム合金は不純物が多いと腐食しやすいので,AZ91合金はD規格を使用しておりますが,構内で再溶解してリサイクルできますか?
構内リサイクルですが数点注意して頂ければ十分可能です.外部で行っているリサイクル工程では,フラックスを使用してマグネシウム合金内の酸化物除去を行うと共に再溶解に低下するAl,Mn及びBe成分の補正(添加)と上昇傾向にあるFe成分の除去になります.脱Fe工程では一旦溶湯温度を上げ,溶湯に塩化MnまたはAl-10%Mn合金を添加します.その後徐々に温度を下げて溶湯中にAl-Fe-Mn金属間化合物を生成させ重力偏析を利用して沈降させます.構内という事で,フラックスレスの連続溶解リサイクルを前提に話をさせて頂きますと,前記脱Fe工程が実施出来ないので,下記6点に注意して頂きたいと思います.
- 溶解時のFeの溶出を極力抑える為に溶湯温度を低めに設定する.
- 溶湯表面の燃焼を極力抑える為に炉内圧を正圧に維持すると共に保護ガスが溶湯表面に直接届く様なレイアウト及び流速を維持する.
- るつぼの内面に酸化チタン等を用いてコーティングする
- 酸化物分離が十分行える様にるつぼ容積を選定すると共に隔壁を設ける
- 溶湯表面及びるつぼ底部のドロス・スラッジを定期的に清掃する.
- 溶湯分析頻度を上げ,Al,Mn,Be成分補正を行う
外部リサイクルに比べて10~20%程度の費用で運用できますが,多少手間もかかりますので事前検討を十分行って実施してください.
(『鋳造工学』90巻4号掲載)
Al-Si系状態図では,共晶組成が11.6wt% と 12.6wt% の両方がありますが,どちらが正しいのでしょうか?
Al-Si 系状態図に関する2009年のMicroscopy Society of Americaの文献 (1) The Al-Si Phase Diagram,George F. Vander Voort* and Juan Asensio-Lozanoの記載をみますと,共晶組成は少なくとも1950年代までは11.6wt%Siと信じられていたと書いてあり,しかし今日現在では12.6wt%Siと記されています.ちなみにNaによる改良処理は1920年代には知られており共晶組成に影響を及ぼすと記されています.さらに,この文献によれば,The currently accepted diagram,すなわち今日現在受け入れられている状態図については,National Bureau of Standards(米国標準局)発行,Murray and McAlister の1984年の研究(2)に基づいていると記されています.これを取り寄せてみてみますと,Hansenの状態図の11.3at%Siは液相線を577℃まで外挿して定めたもので,now considered obsolete,すなわち時代遅れで今では受け入れられない,と書かれています.この文献では実験と熱力学的なデータを基にAl-Si系状態図を検討しており,その結果,共晶組成は12.2at%Siと記しています.これがすなわち12.6wt%Siが共晶組成であるとする根拠であろうと推測いたします.
なお,本件とは直接関係ないかもしれませんが,研究用ではなく,市中の合金として不可避な不純物として微量Ca,P等の濃度によって共晶Si相の形態や初晶Si相の形態に影響を及ぼし,冷却速度等の鋳造条件によっては,たとえ亜共晶組成であっても初晶Siのような形状の組織が見られることが知られています.実際,自動車においては,近年ではHEV化によりエンジンルームに搭載されるデバイスが多くなり,かつ車種によっては低CD化の設計要求もあり,熱交換器の小型軽量化が要請され,結果としてブレージング用クラッド材が薄くならざるを得ないといった理由で,初晶ライクSi相がろう付け不良につながることがあります.Al-Si系合金の金型や砂型の鋳造でも,場合によっては機械的性質や切削工程で問題になることがあるかもしれません.工業上観察される組織については,状態図上の共晶組成以外にもこうした不純物元素,改良処理剤の影響を受けることがあることに留意すべきと思います.
(1) https://www.cambridge.org/core/services/aop-cambridge-core/content/view/S1431927609092642
(2) Murray and A.J. McAlister, Bull. Alloy Phase Diagrams, Vol.5, No.1, Feb. 1984.
(『鋳造工学』89巻9号掲載)
アルミニウム合金中の成分がそれぞれ機械的性質に及ぼす影響はなんですか?
軽合金鋳物,ダイカストの生産技術(素形材センター)に詳しく書いてありますので参考にしてください.
・AC1A,AC1B(Al-Cu,Al-Cu-Mg系):銅とマグネシウムの固溶硬化とGPゾーン及び中間相θ’(準安定Al2Cu)並びに中間相S’(準安定Al2CuMg)の析出硬化により強さと硬さが向上する.
・AC2A,AC2B,AC4B(Al-Cu-Si系):Al-Cu系にけい素を加えた合金系で,熱処理によりAl2Cuの中間相θ’と微量のマグネシウムの含有によるMg2Siの中間相が析出して機械的性質が向上する.
・AC4A,AC4C,AC4CH(Al-Si-Mg系):マグネシウム添加によるMg2Siの中間相析出による強度・靱性を高めた合金である.鉄は靱性を低下させる不純物である.
・AC5A(Al-Cu-Ni-Mg系):銅,ニッケル,マグネシウムを添加成分とし,S’相(Al2CuMgの中間相)とY相(Al5NiCu)の析出により強化され,高温での強度に優れる.
・AC7A(Al-Mg系):マグネシウムを添加した固溶強化合金である.
・アルミニウム合金共通:TiやTi-Bによる微細化処理(組織の微細化)により強度向上させる.
・Al-Si系合金の共通:ナトリウムやストロンチウム添加による共晶けい素の改良処理で強度・靱性を向上させる.
(『鋳造工学』90巻1号掲載)
鋳造品は欠陥があって当たり前というものなのでしょうか?
「欠陥」という言葉の定義が曖昧ですが,「破壊の起点になる可能性があるもの(「きず*」)」と考えると,たとえ非常にミクロ的な格子欠陥,非金属介在物(酸化物,硫化物,炭化物など),微細なき裂やひけ巣でも,それが破壊の起点になり得ないとはいえません.そういう意味では,全ての構造材料に「きず」があります.特に鋳造品は下記のような鋳造という加工工程上,どんなに精緻に造られたとしても外面あるいは内部に微小な「きず」が存在しています.
さて,鋳造品と限定されているので,鋳巣やざく巣のような内部きずの生成について簡単に説明します.ご存知のように,液体の密度(g/cc)は温度上昇に伴い低下します(水のような例外もありますが).即ち分子運動が激しくなるので体積膨張が起こるからです.金属あるいは合金の溶湯に於いても同様です.鋳型に鋳込まれた溶湯は,鋳型壁と接する外側から凝固を開始します.即ち鋳物の殻をつくり,次第に厚くなって最終凝固に至るのですが,その過程で殻に閉じ込められた溶湯(液体)は,温度低下に伴う体積収縮と凝固収縮が進行して体積が減少することになります.したがって,凝固時に収縮量を補う膨張が無ければ内部きずが生成されるのは,当然のことと理解できます.同時に溶存ガスを吐き出しその分膨張するが,系外に吐き出すことが出来ないので内部にガス穴(ガスポロシティー)ができます.鋳造関係者は,これらを無くする,無くせなくとも無害化することに日夜取り組んでいます.たとえば,砂型では冷し金,金型では部分的加熱・冷却,ダイカストのような高圧鋳込みなどがあります.さらに化学組成の最適化,鋳込み温度の管理,凝固・湯流れシミュレーションによる湯口系の設計,砂型強度の改善,添加剤(脱酸剤,脱窒素剤),機械的撹拌などの溶湯のガス抜き,凝固形態を変化させる添加剤(Na,Sr,Ti,Bの単独あるいは複合で含有する処理剤,黒鉛球状化剤や接種剤など)などについての研究開発により,内部きずを実用上問題の無いところまで制御できるようになっています.
気泡の無い氷を作るような指向性凝固を鋳造品の特性をつぶすことなく可能にする3Dプリンターによる積層鋳造法の確立に注目したいと思います.
注)きず:非破壊試験/検査に於いては,評価基準に従って有害とみなされたきずを欠陥と定義しています.
*「きず」とは, 設計された使用条件で破壊する「有害なきず=欠陥」と「無害なきず」があり,これらを分けて考えることが必要です.
(『鋳造工学』90巻1号掲載)
ダイカストで凝固中の溶湯の凝固速度を測りたいのですがどのような方法でやればいいのでしょうか?
実際の鋳物が凝固するときの温度変化を測定することは,ひけ巣などの鋳造欠陥の解決や凝固シミュレーションの確認のために重要な技術です.重力鋳造法や低圧鋳造法などの場合は,金型や中子に応答性の良い熱電対をセットして,凝固過程における溶湯の温度変化を測定したりしています.しかし,ダイカストにおいては,溶湯が高速で射出されることや溶湯圧力が高いことなどもあり,重力鋳造や低圧鋳造のように簡単に測ることができません.そこで,金型に熱電対をセットして何度も使えるようにしたり,熱電対の先端だけを取り換えることができるようにしたりといろいろ工夫をしながら測定する努力がされてきました.また,光ファイバーを用いて測定するような技術も開発されています.
一方,厳密に測定する必要がなければ,出来上がった鋳物の切断面の組織を観察して,2次デンドライトアームスペーシングを測定して冷却速度を予測する方法もあります.同じ鋳物の中での冷却速度の相対的な差を調べるのであれば,このような方法も利用できます.
(『鋳造工学』88巻7号)
マッチプレートとパターンプレートの違い(形式,メリット・デメリット,用途など)は?
一般的に,マッチプレートとパターンプレートは,ともに生型造型に使用する型であり,模型を取付けた定盤(プレート)である.マッチプレートは定盤の両面に模型が取付けてあり,パターンプレートは片面だけに模型が取付けてある.マッチプレートの方がパターンプレートより比較的小さく抜枠鋳型である場合が多く,自動造型機では,一度に,上型と下型を同時に造型し,生産性が高い.一方,パターンプレートは比較的大きい枠付鋳型に使用され,上型と下型を別々に造型する.
また,自硬性鋳型においても,定盤(プレート)の片面だけに模型を取付けた型をパターンプレートと呼ぶ.
(『鋳造工学』88巻7号)
鉛鋳造して硬化室で硬化後,製品を使用時に触ってみると外気温が高い場合(夏場)では柔らかく,外気温が低い場合(冬場)では硬くなる傾向があります.何が一番の原因なのでしょうか.また外気温に影響せず安定した製品を鋳造するには,どこをコントロールするべきでしょうか?
鉛鋳物を硬化室入れても硬化しにくい大きな原因は硬化前の鋳物温度にあります.硬化前の鋳物保持(保管)温度が高いほど,硬化処理後の硬さは低くなります.
時効硬化を目的とした熱処理では,鋳造後の鋳物を溶質元素が固溶する適当な温度(Pb-Sb合金では約250℃)で一定時間温度保持した後に水中急冷してから硬化室にて時効硬化させると効果的です.しかし,溶体化処理後の保持温度(放置温度)が高いと,その保持中に時効析出が進行してしまい,硬化室で時効を進めると過時効となり,軟化してしまいます.溶体化処理はせずに水冷金型に鋳造してから硬化室に入れる場合でも,硬化前の放置温度が高すぎると過時効になり軟化します.
外気温が高い夏場は,硬化室に入れる前の鋳物温度が高いので,過時効になりやすいと考えられます.安定して硬さを出すためには,過時効を防ぐ対策が必要で,3つの手段が考えられます.(1)鋳造時(溶体化を行う場合は溶体化後の急冷時)の冷却速度を速くすること.(2)硬化室に入れる前の鋳物温度を低くしておくこと.(3)硬化後の鋳物を低い温度で保管すること.以上より,夏場には鋳物の保冷室があれば理想的ですが,生産コストが大きくなるのが問題です.その他,夏場には鋳型(溶体化を行う場合は急冷用)の冷却水の温度も高くなりやすいので,注意が必要です.水冷水の温度は30℃を超えないのが理想的とされています.型ばらし後はできるだけ涼しい場所に保管できれば良いのですが,少なくても溶解現場近くや直射日光のあたる場所は避けた方が良いでしょう.
アルミ鋳物を作っているのですが,厚肉部で圧漏れ不良が起こっております.何か対策方法はないのでしょうか? 合金はAC4B合金です.
実際の漏れ部位の観察結果から原因を特定し,対策方法を検討することが基本なので,原因特定と合わせて説明します.
多くの場合は内部にポロシティが存在し,それが3次元的に繋がって漏れるのですから,そのポロシティの主原因がひけ巣であるか,ガスであるかを見分けることです.すなわち,デンドライトが明確に認められればひけ巣,そうでなければガス,と仮定するのです.
しかし,実際の欠陥は明確にどちらとは言えないことがしばしばですし,現場の状況も原因追求の有力な手がかりですから,製品形状からひけ巣が発生しやすいか? 溶湯のガス量は? 中子からのガス発生が疑われるか? なども考慮してより優勢な原因に向けた対策を試みてください.
ところで,漏れ部位を拡大して詳細に観察し,ポロシティの内壁に酸化物が多く認められたら,溶湯の汚れが主原因である可能性があります.今回は溶湯の汚れとガスポロシティの関係を詳しくは説明しませんが,酸化物・介在物はひけ巣やガスポロシティを連結させる作用があるのです.したがって,漏れ不良に「きれいな溶湯」は基本対策です.もし製品に実害が無い程度にポロシティが存在しても構わない場合は,きれいな溶湯にすることで個々のポロシティが繋がらないようになり,気密が保たれる可能性があります.
Fe-C系状態図中の言葉の意味を教えてください.平衡状態図,初晶,共晶,共析,液相線,固相線,A1変態点,A3線,Acm線などイメージがわきません.
一般に平衡状態図とは,横軸に組成(含有量),縦軸に温度を取り,ある組成の溶液や合金などが,ある温度でどのような状態で存在している示す地図と考えると解りやすいでしょう.
そこでFe-C系複平衡状態図は,実線のFe-Fe3C系(準安定系)と点線のFe-C系(安定系)で表されています.炭素鋼では,FeとFe3Cの2相ですが,鋳鉄ではFeとFe3Cと黒鉛の3相になっています.
0.4mass%C 組成:Xの鉄-炭素合金を,高温均一融液状態(液相)からゆっくり冷却すると,AB線と交差します.この線を液相線と呼び,液体中に固体(固相)が現れる(晶出)始める温度を示しています.また,溶融金属から初めて晶出する結晶(固相,固体)を初晶といいます.さらに温度が低下するに伴って固相が増加し続け,JE線と交差します.この線を固相線と呼び,全てが固体(固相)となる温度を示しています.ここでは全てγ鉄(固相,オーステナイト鉄)になります.さらに温度が低下するとGS線と交差します.この線をA3線と呼び,γ鉄からα鉄(フェライト)が析出(一つの固相から別の固相が現れること)し始める温度を示しています.さらに温度低下に伴いα鉄は増加し続け,PS線の温度(727℃)になったとき,残っているγ鉄は,α鉄(フェライト)とFe3C(セメンタイト)に相変態します.この変態が起こる温度をA1変態点といいます.この反応は,1つの固相から異なる2つの固相が共に析出する(同時に現れる)ので,共析反応といいます.
1.0mass%C 組成:Yの合金を1000℃のγ鉄からゆっくり冷却すると,ES線と交差します.この線をAcm線と呼び,γ鉄からFe3C(セメンタイト)が析出しはじめる温度を示しています.ちなみにcmはセメンタイト(Cementite)のことです.
3.5mass%C組成:Zの合金を,高温均一融液状態からゆっくり冷却すると,BC線(液相線)と交差します.この温度で融液からγ鉄が晶出し始めます.さらに温度が低下するとE’温度(1153℃)で,残っている融液からγ鉄と黒鉛(G)が晶出します.この反応は,液相(液体)から2つの固体が共に晶出するので,共晶反応といいます.
(『鋳造工学』88巻11号)
オーステンパ球状黒鉛鋳鉄は強度に優れているそうですが,大型の機械部品にあまり用いられていないのはなぜですか?
「オーステンパ球状黒鉛鋳鉄」とは,特殊な熱処理で基地組織をベイナイトにすることにより,高靱性を持たせた高級鋳鉄です.一般的に,ADI(Austempered Ductile Iron)と呼んでいます.このADIは,一般的なパーライト系の球状黒鉛鋳鉄に比べて,高強度であるにもかかわらず高い伸びを示すことが知られています.熱処理のパターンとしては,A3またはA1変態点以上の温度(900℃程度)に加熱して基地組織をオーステナイト化した後,マルテンサイト生成温度Msより高い温度(375℃程度)で恒温変態させます.恒温変態には,通常ソルトバスが使われます.大物品の場合,肉厚であったりサイズが大きいために,内部まで十分な冷却速度が得られず,パーライトが析出する問題があります.また,無理に冷却速度を速めると,構造によっては大きな内部応力が溜まり,割れることがあります.ADI特有の水素脆性による割れの問題もあります.コスト的にも,大型のソルトバスが必要な事や,鋳鋼との競合においてADIと鋳鋼のどちらが優位かの課題があります.こう言う訳で,オーステンパ球状黒鉛鋳鉄は,大型の機械部品にあまり用いられないと考えられます. (『鋳造工学』87巻11号掲載)
ADC12合金のダイカスト品の湯口を折ると製品まで欠けこんで不良が出来てしまいます.破面が平らになっている部分が見受けられます.原因と対策は?
欠け込み不良の原因として,破面が平らになっている部位があるという事から,初期凝固片(破断チル層)や溶湯酸化膜等の噛み込みが,主因として推察されます.特に,初期凝固片(破断チル)は,スリーブ内に溶湯を給湯したときに,スリーブ壁との接触面で形成された凝固層が,射出と共にプランジャーチップにより破壊されて断片化したもので,それが溶湯に運ばれて湯口付近に残留すると,その部位の強度が低下するため,湯口を除去する時に,製品まで欠け込む原因となるものです.発生を抑制するには,スリーブを保温したり,断熱性の高いスリーブを使用したり,スリーブ内の溶湯充填率を上げるような発生防止策が考えられます.又,混入を抑制するために,湯道や,ゲート形状を工夫する対策も考えられます.一方で,発生源対策ではなく,ノッチをつけて湯口の折り位置を誘導したり,折り位置の拘束を確実にしてから折るなどの工夫により,欠け込み不良を抑制する事例も存在します.適切な対策を試みてください.(『鋳造工学』87巻11号掲載)
オーステンパ処理を施すとベイナイト組織が現れます.等温変態処理温度の違いにより上部(羽毛状組織)と下部(針状組織)のベイナイトに分かれますが,なぜ組織に違いがみられるのでしょうか.上部と下部のベイナイトで機械的性質(引張強さや硬さ)はどの程度異なるのでしょうか.
鋳造品におけるオーステンパ処理の代表として,オーステンパ球状黒鉛鋳鉄(ADI:Austempered Ductile Iron)を念頭にお答えしたいと思います.
「羽毛状」「針状」とは主に光学顕微鏡による組織写真のイメージから来ているものですが,エッチングした試料をSEM観察すると,等温変態時に析出したベイニティック・フェライト部は腐食されて凹,残留オーステナイト部は凸であることが分かります.等温変態温度が上部の場合はベイニティック・フェライトの析出は比較的緩慢で,長さが短いものが分散して存在します.そのため,残留オーステナイトは周囲をギザギザに縁取られた島状に残されます.光学顕微鏡ではエッジはSEMほどシャープには見えませんから「羽毛状」といった印象になります.一方,等温変態温度が下部の場合はオーステナイト化温度からの冷却が大きいため相変態の駆動力が大きくなります.このためベイニティック・フェライトはもっと長く直線的な成長を示し,これが「針状」といったイメージを与えるのです.
機械的性質の差については,引張強さは350MPa,硬さはHB80くらいで,いずれも下部の方が高くなります.
(『鋳造工学』92巻4号掲載)
接種をすれば引張強さが向上する事は事実です.しかし,接種をすれば黒鉛化が促進されて黒鉛量が増加し,密度は下がるはずですが,なぜ接種をして黒鉛化を促進した方が強度が向上するのでしょうか.
接種は,鋳込み直前の鋳鉄溶湯にフェロシリコン(Fe-Si)やカルシウムシリコン(Ca-Si)などを少量添加して凝固組織を改善し,機械的性質の向上を図る溶湯処理法の1つです.接種を施すことにより,鋳鉄の組織が改善され,チル化が抑制され,肉厚感受性が小さくなります.接種により片状黒鉛鋳鉄の組織は,A型黒鉛組織となり,基地組織のパーライト化が促進され,それにともない黒鉛面積率もわずかに減少するので,引張強度が向上します.
参考文献:中江秀雄監修:鋳物技術者と機械設計技術者のための新版鋳鉄の材質,日本鋳造工学会(2014)P18
(『鋳造工学』92巻4号掲載)
ねずみ鋳鉄FC300にはSnを添加し,球状黒鉛鋳鉄FCD700にはCuを添加して製造しています.それぞれ高強度にするために,パーライト量を増やす目的なのでしょうか.逆に,ねずみ鋳鉄にCuを,球状黒鉛鋳鉄にSnをそれぞれ添加しても問題ないのでしょうか?
高強度にするためにねずみ鋳鉄または球状黒鉛鋳鉄にSnまたはCuをそれぞれ適量添加し,ほぼオールパーライトにすることが目的です.
逆にねずみ鋳鉄にCuを,球状黒鉛鋳鉄にSnを添加しても問題ありません.
生産上高強度FCにはCu単独添加はほとんどありませんが,Mn,Crなどのチル(セメンタイト)化促進元素と併用するケースがよくあります.また,FCD450相当の球状黒鉛鋳鉄にSnを一定量(例えば0.07mass%程度)入れるとほぼパーライト基地が得られるので,高強度になります.
ねずみ鋳鉄のパーライト量に及ぼすCu添加の影響についてもう少し付け加えると,球状黒鉛鋳鉄に対してはCuがパーライトを促進することになりますが,一方でFCにおいては近年の研究報告1)によるとCuがフェライト化を促進する元素であるとの実験結果があり,FCの高強度化にはCuの単独添加は必ずしも効果的ではないことが示唆されています.詳細は中江らの論文1)をご参照いただきたいと思います.
球状黒鉛鋳鉄を高強度化するためにSnを添加する場合,0.1mass%以上の添加は避けるべきです.特にSnは結晶粒界に偏析しやすく,また,伸びと衝撃値の低下にも繋がってしまうので,適量の添加及びCuなどとの併用が効果的です.
1)鄒 瑩,駒田賢一,中江秀雄:鋳造工学 83(2011)378
(『鋳造工学』91巻11号掲載)
生型砂の‘ねかせ’時間は2時間ほどといわれていますが,2時間で何が起こっているのでしょうか?
生型砂の粘結材であるベントナイトは,水を吸収し膨潤することで粘結力を発揮します.ベントナイトを水に投入し自然に膨潤するには数時間という時間を要するため,物理的に力を加える混練(ねり作用)が行われて使用されます.混練は3~5分で終了し,混練機から排出され造型機に送られます.混練砂を直接造型機に送らずに一旦貯蔵することを‘ねかせ’と称しています.貯蔵する時間によって,フル・テンパー,プレ・テンパー,アーフター・テンパーの3タイプに分類されます.生砂の‘ねかせ’時間は2時間ほどといわれているのは,一般の感覚的な話であり,理論的な裏付けはありません.
混練された生型砂の水分は,図1に示すように粘土層内に存在する位置によって,自由水,付着水,吸着水に区分されます.図2の左半分は鋳込み後回収された戻り砂を右半分は混練された生型砂の粘土層における水分濃度を模式的に示したものです.戻り砂の粘土表面層は乾燥して内部に多少水分が残っている状態を示し,混練砂の粘土表面層は水分濃度が高いことを示しています.水分は砂粒の粘土層表面上の自由水から付着水の状態になり,さらに粘土層の粒子間隔に吸いつけられている吸着水(層間自由水)となり,ベントナイトの粘結層に存在しています.吸着水として取り込まれた水が粘土の粘着力となります.更に固相の中に強い結合力で引き入れられると収着水(層間結合水)や結晶水(OH型)となります.
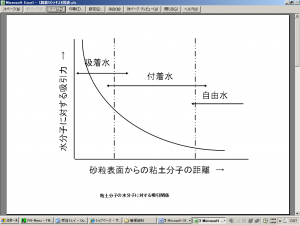
図1 粘土分子の水分子に対する吸引関係
3~5分混練した生型砂の水分の多くは,この自由度の高い自由水および付着水の状態で存在していると考えられます.この砂を‘ねかせ’ることで,自由水および付着水の状態から吸着水となり,徐々に熟成度が進むと考えられます.貯蔵する時間が長ければ,収着水や結晶水のかたちに進み,更に安定した生型砂が得られます.熟成した砂はしっとりとこしがあり水分が高そうで実際の測定値は低く,造型すると流動性が意外とよく均一にしまります.生型砂の熟成度が進むにつれて,生型砂の湿態性質であるCB値,水分,圧縮強度,SSI,通気
度等が安定します.
(『鋳造工学』91巻1号掲載)
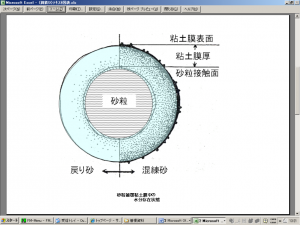
図2 砂粒被覆粘土膜中の水分存在形態
Zn-Al合金で室温まで冷えた鋳物が後になって熱くなっていることがあります.どうしてそんなことが起こるのでしょうか?
「鋳物」を大きな意味での鋳造品と考えると表面温度上昇の原因として次のことが考えられます.
熱が溜まりやすい部分がある鋳物,例えば,厚肉部分がある,中子がある,大きな湯口や押し湯が付けられている場合には,表面が冷えても内部は充分冷えておりません.このため,内部の熱でゆっくりと表面が熱くなることが考えられます.ダイカストでも同じようなことが起こります.
ダイカストでの特徴的な現象として,使用量が多いZn-4%Al合金では,急冷凝固されると平衡状態に近い組織,α-ZnとZnの固溶度の低いβ-Alの組織とならず,α-ZnとZnの固溶度の高いβ’-Alの組織になります.β’-Alは室温で,β’-Al →β-Al+α-Zn のゆっくりとした発熱反応を起こし,最終的に安定なβ-Alに変化します.凝固から室温までの冷却時にもこの反応が起こるため,全てがβ’-Alになるわけではありませんが,急冷ほどβ’-Alが多く残るため,発熱量が多くなります.この自然時効によって寸法変化が起こるため,寸法公差が厳しいダイカストに対して「安定化処理」と呼ばれる焼なまし処理を行います.
もう一度,鋳物の構造と,どの段階でどの程度温度が上がるのか,現場の鋳造品の状況を丁寧に調べ直すと答えが見つかります.
(『鋳造工学』91巻11号掲載)
海外産のダイカスト合金を使用しだした頃から,流動性が低下しだし,湯周り不良が多発するようになりました.合金成分的には問題無いと思っていますが原因がわかりません.何が原因なのでしょうか?
流動性の低下には大きく分けて2つの原因があります.ひとつは,酸化物の混入です.高い温度で溶解してしまうと,空気中の水分と反応してしまい,溶湯中に酸化物が浮遊します.またこの酸化物は空気との相性もよく酸化物に空気が付着してしまいます.これらの溶湯は粘性が高い状態になります.海外産の合金で十分なフラックス処理が行われないで再生塊になった場合には,酸化物の多い2次合金であると言えます.
2つ目はダイカスト用合金の化学成分以外の微量元素の影響です.2次合金であるダイカスト用の合金成分は主要な化学成分以外の規定がなく微量の元素が入っても測定されない場合があります.特に金属ケイ素に付着して混入するカルシウムは,微量であっても粘性を著しく悪くします.カルシウムの入ったダイカスト品の肌はがま肌になる特徴があります.
上記一つ目は,組織観察で非金属介在物として捉えることが可能です.2つ目の場合には,組織観察でAl-Siの共晶相が改良(微細化)されています.詳細な分析を行えば,カルシウムも分析されると思います.どちらも専用のフラックス処理で解決できますので,原因を掴んで,適切な処理を行ってください.
(『鋳造工学』87巻8号)
鋳鉄特有の鋳造欠陥にはどんなものがありますか? どのような機構で発生し,どの程度の大きさになりますか? また,発生しやすい部位を教えて下さい.
日本鋳造工学会編「鋳造欠陥とその対策」では,鋳造欠陥を発生箇所や原因により,A)寸法・形状不良,B)ひけ巣,C)ガス欠陥,D)割れ,E)介在物,F)外観不良,G)中子不良,H)鋳肌不良,I )組織不良,J)破面不良,K)強度不良,L)工業的性質の不足の12種類に分けています.
鋳鉄鋳物ではA)からL)のすべての鋳造欠陥が見られますが,鋳鉄は黒鉛を多量に含有することで他の鋳造材料と異なり,異常黒鉛やチルの晶出が,鋳造欠陥となります.ここでは,鋳鉄特有の鋳造欠陥としてI )組織不良に関するものについてお答えします.
チルは一般的に隅角部や薄肉部のように急速に冷却された場所に発生しますが,逆チルは,鋳物の中心部に炭化物が発生する不良です.特に厚肉鋳物ではMn,Cr,Moなどの炭化物を形成しやすい元素が最終凝固部に偏析することにより,逆チルが発生します.
チャンキー黒鉛は鋳物中心部に発生した少し黒ずんで見える異常黒鉛組織です.チャンキー黒鉛の生成機構については諸説有り明確ではありませんが,過剰なCeやCaやNi,そして過剰なSi添加の場合に発生しています.チャンキー黒鉛の防止には,黒鉛の球状化を阻害するSbの添加が有効とされています.
ウィドマンステッテン黒鉛は,ひげ状の黒鉛が成長した異常黒鉛です.FC250では鉛が30ppm,FCD600では鉛が50ppmを超えると,この異常黒鉛が鋳物全体(特に大物鋳物)に発生します.
フラン鋳型に鋳造したFCDの鋳肌付近(1~1.5mm程度)に球状化不良が発生することがあります.これは,フラン鋳型に用いる硬化剤にSが含まれているため,溶湯中のMgと反応して球状化に必要なMgが不足するために発生します.
(『鋳造工学』87巻8号)
鋳鉄の溶湯の中から非金属の黒鉛が出現するのはどうしてですか.さらにオーステナイトからも黒鉛が現れるのはなぜですか? 教えてください
確かに不思議な現象ですね.謎解きは,昔習った理科の「溶液の勉強」で溶媒と溶質,飽和溶液と過飽和溶液,溶解と沈殿,溶解度などを思い出そう.
鋳鉄の溶湯とは,溶媒が液体の鉄で,溶質が主に炭素(C)とけい素(Si)の溶液と考えることもできます.広い意味で2つ以上の金属同士あるいは金属と非金属元素の溶液が固まった物が合金です.鋳鉄は鉄と炭素の合金です.鉄-炭素2元平衡状態図は,あるC%の溶湯が,温度低下に伴いどのような状態で存在しているかを教えてくれます.
話を質問に戻そう.鋳鉄の溶湯(溶液)を鉄と炭素からなる溶液とすると,高温では飽和溶液に達していませんが,温度低下により飽和し,そして過飽和の状態になると溶質が溶湯中に晶出します.亜共晶組成(CE≦4.3%)の場合には共晶温度になるまで炭素は飽和せず,溶湯中に初めに現れる結晶(初晶)は,オーステナイト(γ鉄)です.過共晶組成(4.3%≦CE)の場合には,液相線温度に達すると溶湯から炭素が吐き出されて初晶の黒鉛(固相)として晶出します.溶湯組成が共晶(CE=4.3%)で温度が共晶温度に達すると,亜共晶,共晶,過共晶いずれの組成でも残液からオーステナイトと黒鉛が同時に晶出し始め共晶凝固終了時には,すべてが固相(オーステナイトと黒鉛)になります.すなわち,溶液から非金属の黒鉛が現われるわけです.
固体には,溶解度の代わりに固溶度があり温度によって変化します.鋳鉄の場合,共晶凝固直後のオーステナイト中に固溶する炭素は,組成(亜共晶,共晶,過共晶)に関係なく約2%※)(共晶温度1145℃)ですが,温度が低下し共析温度(723℃)に達すると,0.8%になります.この間に固溶していた炭素の約1.2%がオーステナイトから吐き出され,黒鉛として主に既存の黒鉛の周囲に析出します.すなわちオーステナイト(固相)から黒鉛(固相)が現れるのです.溶液,溶解度,固溶度と鉄-炭素状態図が謎解きの鍵でした.
※)鋳鉄の場合この値はCE%なので実際のC%は,Si含有量の1/3を引いた値になります.
(『鋳造工学』89巻2号掲載)
(アルミニウム合金)ダイカストが一般に溶接や熱処理が困難な理由をわかりやすく教えてください(近年行われている対策方法も含めて)
一般的にアルミニウム合金ダイカストは,高速・高圧で金型に溶湯を射出するため,ダイカスト中に空気を多く巻き込んでいます.その量は20-100ml/100gAlとも言われております.そのため,T4・T6・T7など溶体化処理を伴う熱処理を通常のダイカストに行うと内部の空気が膨張し,膨れブリスターが発生します.同様に部分的に溶解させる溶接は内部の空気が急激に蒸発するため,酸化防止のシールドガスを破り大気を吸収したり,溶接部に多くのブローホールの発生原因になったりします.一般的に熱処理可能なアルミニウム合金鋳物中のガス量は3ml/100gAl以下,溶接可能なガス量は1ml/100gAl以下と言われています.
溶接や熱処理可能にするためには,巻き込まれるガス量を減らすことばかりでなく溶湯中に含まれるガス量すなわち水素量も減らすことが重要です.使用する溶湯の脱ガスをすること,そして巻き込みガスの少ないダイカスト工法を選ぶことです.巻き込みガスの少ない工法では,PF法,低速充填法,高真空ダイカスト法などを選び,ガスの巻き込みが少なくなる方案にすることが大事です.
(『鋳造工学』89巻2号掲載)
中国からのREが入手困難になり昨年末は騒ぎが大きくなりました.今年に入り一段落ついたようですが,鋳鉄用黒鉛球状化材におけるREの役割について改めて教えて下さい.
REとは
REはRARE EARTH の略.希土類 と訳されています.
希土類元素は,周期表3(A)族であるスカンジウム(Sc),イットリウム(Y)およびランタノイド15元素を合わせた17元素です.ランタノイドにはLa,Ceなどがあります.
REが鋳鉄の黒鉛球状化材に使われた経緯
現在アルカリ土類金属のMg,Caなどが入った球状化材を使った黒鉛球状化処理が一般的に普及しています.球状黒鉛鋳鉄が開発された当初,鋳鉄中のS(硫 黄)やO(酸素)と親和力が強い元素としてMg,Caが単独で使われていましたが,鋳鉄の片状黒鉛の形状とは異なる黒鉛形状を呈した白銑から熱処理で作る 可鍛鋳鉄(今ではあまりなじみがなくなりました)に比べて熱処理時間が短く,延性に優れている点で工業化技術が急速に進み,球状化処理用の合金の開発に伴 う鋳放し球状黒鉛鋳鉄が使途を広めていきました.
REを含むミッシュメタルは鉄鋼では強力な脱酸効果があるということで使用されていました.一方,純Mgを使ったコンバーター法でも球状化処理に併用されていました.なお,REと言ってもCeが全体の約50%,Laは約30%またほかの元素も約20%含まれています.
Mg合金におけるREの役割
通常使われている球状化処理材には45%SiをベースにMg3%から7%,RE1%から2%,Ca2%,Al0.5から1%などが含まれています.
まずメインのMgによって脱酸,脱硫されます.その結果Mgと酸素や硫黄との化合物が黒鉛の核となると言われています.Mg自体は鉄にほとんど溶け込みま せんので蒸発し,時間とともに効果が斬減 (フェーディング)すると言われています.Ca,Alはどちらかというと必然的に含有している元素で意図的な添加によるものではありません.Caは1%か ら2%含まれていますが,Mgの酸化物や硫化物に比して沸点が高いため,反応の激しさを抑えることができます.一方多くなるとノロが増えます.
Alは脱酸材として広く知られていますが上記同様1%から2%含まれ,低めに抑えたものはノロが発生しにくくなります. さてREは酸素,硫黄との反応性(親和力)が高く,添加によって鋳鉄溶湯の脱酸,脱硫が行われます.Mgのフェーディングをカバーして球状化不良を抑制します.また,今般スクラップ材料に含まれている球状化阻害作用を持つ元素を中和する作用もあるとも言われています.
REの役割としては
球状黒鉛鋳鉄を製造するには球状化材にREが含まれたものを使った方が簡易で安定した品質が得られると言えるでしょう.ところが,これは肉厚が30mm以 下の小物中物製品を対象にした話です.大物の200kg,500kg,1トン,10トンの製品になるとREが逆にチャンキー黒鉛の原因になる場合もあり, 鋳造品の肉厚による凝固速度の相違の問題になります.これに関しては別途解説をしていきます.
アルミニウム合金ダイカストの材料強度を左右する因子にはどんなものがあるのでしょうか?
アルミニウム合金ダイカストの材料強度は,鋳造欠陥の存在,凝固組織の大きさ,材料成分の影響を受けます.
特に鋳造欠陥による材料強度への影響は大きく要求品質に強度要件がある製品の製造では,鋳造欠陥をなくす工程検討が必要になります.鋳造欠陥には,①スリーブ内で溶湯の一部が凝固して巻き込まれる破断チル層,②空気や離型剤・潤滑剤が溶湯と反応してできるガスの巻込巣,③肉厚部で溶湯補給が不十分でできる引け巣,④溶湯中に含まれる介在物,⑤ガスの介在による表面の融合不良でできる湯回りや湯境などの表面欠陥があります.特に①の破断チル層は,スリーブとの接触で酸化被膜が形成されるので強度低下への影響が大きくなります.
凝固組織(Al初晶αや共晶の組織)は,主に冷却速度によって変化し,製品肉厚が厚く,金型温度が高いほど,凝固組織が大きくなり,強度特性が低下します.表面チル層は強度特性が良いので,この部位を削除する機械加工の有無によっても製品の強度特性が変わります.
アルミニウム合金ダイカスト生産の95%はADC12が使用されますが,規格の範囲内でも主要元素のSiの量や不純物のMg,Feの量によっても強度特性が変化します.
黒鉛はなぜ球状,CV,片状になるのですか?
鋳鉄中に現れる黒鉛は,六方晶系の結晶構造(六角形)です.片状黒鉛は黒鉛結晶のプリズム面方向(六角形の各辺が連なる方向,a軸方向)に成長した黒鉛で,基底面方向(六角形の面,c軸方向)放射線状に積層した黒鉛が球状黒鉛(六角形の皮を継ぎ合わせたサッカーボールのマトリョーシカ)となります.球状黒鉛の生成機構は,次のような説があります.
(1)核説:球状黒鉛晶出のための有効な異質核が存在する.
(2)過冷説:球状黒鉛の生成が過冷度の増大に起因する.
(3)界面エネルギ-説:球状化元素の添加により黒鉛のプリズム面に吸着するS,Oなどの活性不純物元素が取り除かれるため,黒鉛のプリズム面と溶湯間の界面エネルギーが大となり,黒鉛がエネルギー的に安定な基底面方向に成長し球状黒鉛となる.
(4)吸着説:球状化処理により黒鉛表面にMgなどの活性な元素が吸着し,高温における黒鉛の塑性変形能が増大し溶湯圧により球状化すると考える.
(5)転位説:Mgなどの球状化元素が黒鉛基底面の成長先端に吸着してらせん転位を生じ,これがC軸方向への成長を促進し,球状黒鉛となる.
(6)気泡説:球状化剤のMgなどが溶湯中で気泡を形成し,凝固に際して黒鉛は気泡の表面で生成し,隣の黒鉛と接した後,基底面に向かって成長して球状黒鉛になる.
CV黒鉛は,球状化に失敗した時に球状黒鉛鋳鉄に存在していますが,これらの説やCV黒鉛化機構について,詳しく知りたい方は,下記の文献を参考にして下さい.これまでは,鋳型内に注湯された鋳鉄の凝固過程を直接観察することができなかったので,熱解析、凝固組織の観察などから理論的に推測するに過ぎませんでしたが,最近では,SPring-8の放射光を利用した“時間分解,その場観察X線イメージ”による鋳鉄の凝固現象の研究が進んできています.近い将来,鋳鉄の凝固の“その場観察”により黒鉛の生成の様子が明らかにされることでしょう.
<参考文献>日本鋳造工学会編:鋳造工学便覧(丸善)(2002)237,鋳造工学,79(2007)605,鋳物,56(1984)329
接種量が多い場合,引け巣が増大するといわれていますが,どの様なメカニズムにより増大するのでしょうか?
『接種量が多いとひけ巣が増大する』とは一概に言えません.言えるのは,①FeSi系接種剤から核生成物質がSiと共に添加されるので,②黒鉛化(溶鉄に溶解している炭素は晶出して黒鉛になる)が一挙に進みます.すると鋳鉄の場合,③溶質である炭素が過飽和となり黒鉛として晶出,体積が約3.4倍になるので膨張(張り気)が起こり,鋳型内壁を外に押し広げる力が働き,鋳型変形あるいは上型を持ち上げます.結果として鋳物空洞の容積が大きくなり,これがひけ巣の一因となることもあります.鋳型が十分に強くかつ製品になる部分が共晶凝固する時,湯口系へ溶湯の逆流が無ければ,この膨張はひけ巣低減に寄与することになります.特に球状黒鉛鋳鉄は片状黒鉛鋳鉄の表皮生成型(スキンフォーメイション)凝固に比べ,凝固殻が弱いマッシイ型(かゆ状)凝固なので鋳型にかかる力が大きく,鋳型強度もひけ巣の一因なります.とは言え,ひけ巣は溶湯が湯口系と遮断された後の凝固過程で外殻が出来,内部の液相の収縮と膨張量,鋳型強度と膨張,型締め力とウエイトさらに鋳枠の強度などとのバランスが問題で,接種の添加量だけでは説明できない現象なのです.
逆に,「接種量が多い」とは,どのように考えての質問だったのでしょうか? 教えて下さい.さらに接種には,チル防止,機械的性質の改善,ひけ防止などいろいろな目的があり,目的に応じて接種剤,添加方法そして添加量を決めなければなりません.今回はここまで,さらに詳しくは,次の質問か別の機会で,下記文献も参照ください.
参考文献:新版「鋳鉄の生産技術」P405~412平成24年10月10日発行,素形材センター
球状黒鉛鋳鉄の回転曲げ疲労試験と軸荷重疲労試験の試験結果に差がみられました.その理由について教えてください.
回転曲げ疲労試験とは,一定の曲げモーメントを作用させた丸棒を回転させ,試験片平行部の表面に繰返し応力を負荷させる疲労試験です.また,軸荷重疲労試験とは,試験部の断面上のどの点においても単軸の引張圧縮状態になる様に繰返し負荷をかける疲労試験のことです.
さて,球状黒鉛鋳鉄の疲労試験を行うと,回転曲げ疲労試験に比べて軸荷重疲労試験の疲労限度は低下します.これは主として荷重方式の違いによる危険体積の変化が影響しています.危険体積とは,試験片中の繰り返し最大荷重,最小荷重が負荷される部分のことです.疲労き裂は危険体積中に存在する最大の欠陥から発生すると言われております.この場合,球状黒鉛鋳鉄の破壊起点となる欠陥は,引け巣や集合黒鉛,球状化されてない黒鉛が知られております.試験片平行部を有した試験片を用いた場合,回転曲げ疲労試験における危険体積は,平行部の表面近傍であるのに対して,軸荷重疲労試験では平行部全体が危険体積となります.この影響は破壊起点の箇所にも現れます.回転曲げ疲労試験では破壊起点は試験片表面もしくは近傍に存在するのに対し,軸荷重疲労試験は表面および表面近傍だけでなく平行部内部の欠陥も破壊起点となることがあります.
すなわち,軸荷重疲労試験における危険体積は,回転曲げ疲労試験に比べて大きくなるため,結果として大きな欠陥が破壊起点となる可能性が高くなります.そのため,疲労限度に差が生じたと言えます.しかし,基地組織の違いにより疲労限度に差が生じる場合と生じない場合があります.一般に基地組織が軟らかい(例えばフェライト地など)場合,試験法の違いによる影響が現れにくく,硬くて靱性に乏しい(例えばパーライト地など)場合は,存在する欠陥寸法が小さくても,試験法の違いにより疲労限度に差が生じます.
鉄-炭素2元平衡状態図は常温で基地組織はフェライトなのに,なぜパーライトが出るのですか?
確かに熱力学平衡状態では,室温でフェライトと黒鉛になります.しかし質問にあるように,実際の鋳鉄鋳物ではねずみ鋳鉄に代表されるようにフェライトとセメンタイトの層状組織であるパーライトが基地組織中に生成します.パーライトが出るということはセメンタイトが出るということであり,平衡状態ではないセメンタイトが生成する要因は2つあります.
一つ目は化学的な要因です.黒鉛はセメンタイトよりも熱力学的に安定なのですが,その差は僅かであり,セメンタイトも生成しやすいのです.Fe-C二元系の共析温度で比較してみると黒鉛共析が安定になる温度は740℃以下に対してセメンタイト共析が安定になる温度は727℃以下であり,その差は13℃しかありません.
二つ目は核生成・成長の要因です.共析変態における黒鉛は基地組織中からはほとんど核生成せずに凝固中に生成した既存の黒鉛が成長し,共析変態が進行することが知られています.しかし,平衡量になるまで黒鉛が成長するには,基地組織中の炭素が黒鉛に向かって拡散移動する必要があり,それに時間を要します.その前に鋳物が冷えて,セメンタイトが安定になる温度にまで冷却されるとパーライトが生成します.
パーライトを出したくない場合はセメンタイト共析温度以上,黒鉛共析温度以下で十分な時間保持すれば,黒鉛とフェライトの組織となります.基地をフェライトにしたい場合は,このような熱処理が施されます.反対にパーライトを出したい場合は,冷却速度を速くするかマンガン量を増加させるなどオーステナイト安定化元素を利用することで,黒鉛共析とセメンタイト共析の熱力学的安定性の差を小さくすることが有効となります.球状黒鉛鋳鉄においては,銅を添加してもパーライトが出やすくなるのが有名ですが,このメカニズムは少し複雑で,黒鉛と基地との間に銅の薄い層が存在するために基地と黒鉛間の炭素の拡散速度が非常に小さくなるためだと考えられております(ZOU Ying他:鋳造工学, 83(2011)7, 378-383).
チャンキー黒鉛をなくす方法についてお教えください.
もちろん黒鉛粒数を増せばチャンキーはなくなるのですが, 実際の大物製品ではそれほど黒鉛粒数を増すことは出来ないので, 現実的にはSb(アンチモン)を使ってチャンキー黒鉛を止めている会社が多いようです.
RE(レアース)のない溶湯をつくる方法や冷やし金を多様することにより, チャンキー黒鉛を防止している会社もあります. ヨーロッパなどでは, Sbの変わりにPb, Bi などを使うこともあるようですが, Pbは球状黒鉛の周りにトゲ状の黒鉛を発生させますし, Biでは整列状黒鉛などが発生します.
鋳造工学会誌の76巻2号P125に津村氏が, Sb/RE>0.7でチャンキー黒鉛がなくなることを示しています. REの50%がCe(セリウム)だと考えると, Sb/Ce>1.5でチャンキー黒鉛は防止できることになります. 海外の人などと話すとSb/Ce=2とも言います. 球状化剤から入るCe量とスクラップから入るSb量(ダライ粉や電磁鋼板にSbが含まれます)を加味して, Sb/Ce>1~2になるようにSbを添加します.
Sb/Ce比は, 製品の肉厚・重量等によって変わります. ただしSb量は好ましくは20-50ppmの範囲にする必要があるため, あらかじめ球状化剤中のRE量をSbがこの範囲に入るように調整する必要があります. Sbが50ppmを越えるようになるとSbによる部分的なパーライトや星状の片状黒鉛が出るようになります.
CuやSnを使う場合は, これらの元素がSbと類似の働きをしますので, Sb量は下げられると考えられますが, CuとSnの効果が不明なので, どの程度下げられるかはわかりません.
黒鉛球状化率とは何物なのでしょうか? 球状黒鉛鋳鉄品のJIS G 5502に示されている測定法と評価基準の一つなのですが,物理的にどんな意味合いがあるのでしょうか?教えてください.
鋳鉄とは,片状黒鉛,CV黒鉛,球状黒鉛などの黒鉛(非金属)が鋼の中に3次元に分散している自然に出来た複合材料です.そしてどの形状の黒鉛が存在するかにより,機械的性質(引張強さ伸びなど)や物理的性質(熱伝導度,ヤング率,減衰能など)が異なります.
特に球状黒鉛鋳鉄の機械的性質(引張強さと伸びなどの規格値)は,球状の黒鉛が顕微鏡観察(100倍,腐食なし)で平均80%以上なければ得られません. したがって,黒鉛球状化率は物性値ではありませんが,引張強さと伸びを保証する重要な評価基準の一つ,必要条件なのです.黒鉛球状化率が80%以上あるこ とを前提に,球状黒鉛鋳鉄の種類(FCD400,450,500,600,700,800)が存在する事も事実です.
QQさんへ:黒鉛球状化率と伸びや引張強さをグラフ化(横軸に黒鉛球状化率,縦軸に機械的性質)してみよう.
鋳鉄は,生産性の良い金型をあまり使わないのはなぜですか?
鉄には非鉄や鋼とは異なり,チル化という問題があります.これが,金型をあまり用いない最大の原因です.
鋳鉄は,ジキルとハイド氏のように黒鉛が出るタイ プ(片状黒鉛や球状黒鉛鋳鉄)とチルと言って黒鉛が析出しない硬くて脆いタイプの2面性を有した困った材料です.冷却速度に合った黒鉛核生成能力と成分に しないと,ハイド氏のようにチルになってしまいます.その他の問題としては,溶解温度がアルミニウム合金や銅合金より高いという問題もあります.温度が高 いので,金型が長持ちしなかったり,溶湯と金型がくっ付いたりすることになります.
しかしながら,鋳鉄の金型鋳造が全く行われていない訳ではありません.昭和51(1976)年11月には,「鋳鉄の金型鋳造」という本が日本鋳物協会(現 在の鋳造工学会)から出版されています.その本によれば,1965年における各国の鋳鉄生産量における金型鋳造の比率は,ソ連9.5%,東ドイツ 5.8%,アメリカ3%,西ドイツ1%となっています.
当時のショット回数は,500-5000回程度だったようです.また,鋳造工学会への「鋳鉄の金型 鋳造」に関する研究論文は34件出されています.どなたかが、生産性の良い鋳鉄の金型鋳造を開発すれば,鋳鉄の世界もダイカストのようになるのかもしれま せん.
球状黒鉛鋳鉄の引張試験用供試材は,JISG5502では,「鋳込みの終わり近くに鋳造する」と記載されています.しかし,実際の鋳込みは,製品等により時間がばらついて,結果として安定的な試験結果が出ません.そうならないようにするためには,(フェイディングを見越して)予めMgを高めにする等の工夫をした方がよいのでしょうか? また弊社では,ほとんどの場合(客先立ち会い等含めて),試験片は球状化処理直後に採取していますが,それは厳密には正しくないやりかたでしょうか?
球状化処理後,注湯までに長時間経過した鋳鉄溶湯では,球状化不良やチルの発生などの問題が生じます.
良好な球状黒鉛鋳鉄を得るための溶湯処理条件は,球 状化剤の粒度や添加量,溶湯の量,処理温度などの諸条件により変動しますが,標準的な効果の持続性(フェイディングが起こらない時間)は,10分程度と言 われています.そこで,10分以内に全ての鋳型に注湯し,最後の鋳型に注湯するのにあわせて,引張試験採取用鋳型に注湯するのがよいでしょう.
鋳込み終わり近くの溶湯を鋳造するのは,同じ取鍋から先に鋳込まれた試験片の材質の方が,終わり近くの溶湯から鋳込まれた引張試験片の材質より悪くならな いと考えているからです.鋳込みまでの時間が異なれば,引張試験結果もわずかに異なりますが,この場合安定的した試験結果を得ることが目的ではなく,同じ 取鍋から鋳込まれた鋳造品が,定められた基準以上であることを保証する意味もあります.
また,過剰なMg添加は,チルを誘発するので,最終鋳込みでのフェイディングを見越して,はじめからMg量を多くすることは,決して良い方法とはいえません.
なお,現実には,引張試験片として球状化処理直後の溶湯を鋳込んで採取したものを評価している鋳物工場も数多くあります.ただし,この場合も,数々の経験と実証の上で,客先と話し合って両者で取り決めて自社の責任で行っているものです. 球状化処理後,注湯終了までの時間経過にともなう残留Mg量の減少については,あらかじめ調査を行い,フェイディング時間をよく管理することが大切です.
片状黒鉛鋳鉄の引張りと圧縮の機械的特性は,どう違いますか?また,疲労試験において圧縮成分を含む試験を行った場合(応力比R<0),注意するべき点はありますか?
引張強さは鋳鉄の材質を表わす目安となっていることはご存じかと思います. JIS G 5501ではねずみ鋳鉄(片状黒鉛鋳鉄)の引張強さは,100〜350MPaとなっています.
圧縮試験は引張試験ほど頻繁には行われませんが,延性金属の 塑性加工性の判定や鋳鉄,コンクリートの様に脆い材料では行われることがあります.通常,引張応力はき裂を開口し,圧縮応力はき裂を押しつぶし閉口させる 作用があり,延性にやや乏しい材料においては,圧縮破壊応力は引張破壊応力よりも大きくなります.片状黒鉛鋳鉄では圧縮強さは引張強さの3〜4倍に達し, 引張強さの低い鋳鉄ほど,その比が大きくなるようです.
応力比R>0で行う疲労試験(引張-引張)を片振り試験というのに対し,応力比R<0で試験を行う疲労試験(引張-圧縮)を両振り試験と呼びます.両振り 試験ではR=-1(最大引張応力と圧縮最大応力が等しい)で行われることが多く,回転曲げ疲労試験がよく知られています.
丸棒や板で疲労試験片を作製し, 軸方向に繰り返し荷重を負荷し,疲労試験を行う報告もありますが,負荷する応力や試験片の断面積,ヤング率,試験片の長さによっては,「坐屈 (Buckling)」と言って,ある荷重で急に変形の模様が変化し大きなたわみを生じてしまう場合があり,注意が必要です.
鋳鉄の溶湯処理で,フラックス処理・接種処理・球状化処理は同時にやらないのは何故ですか?
それぞれの処理に以下のような役割があり,同時処理ではそれぞれの効果が十分に発揮できないからです.また,処理効果は経時変化により減衰していく(フェーディングする)ものです.処理時間の経過で質が変化するという点では,鋳鉄溶湯は生ものといえるかも知れません.
フラックス処理は,あまり聞かないものですが,元湯の性状を一定にするための処理と考えられます.元湯S%の調整には脱硫処理や加硫処理で溶湯中のS% を,脱酸処理では溶存酸素量をある量以下に低減させます.窒素ガスが悪さをするときは,Zr,Al,Ti(片状黒鉛鋳鉄のみ)など窒素と仲の良い元素を含 有する合金を添加します.これらは,接種処理や球状化処理の前に行われます.
片状黒鉛鋳鉄の接種処理は,一定性状にした溶湯の黒鉛化(溶湯から黒鉛を晶出させる)を促進させると共に共晶セル数を増加させA型黒鉛を得るための処理です.
球状黒鉛鋳鉄では,溶湯中で球状黒鉛が作られる環境を作る球状化処理後に接種を行い,黒鉛化を促進させて黒鉛粒数を急増させます.これにより引け傾向やチ ル化傾向が低下し健全な鋳物を造ることが出来ます.
このような順序は,電気炉熔解の原料投入順序や料理の味付けの基本「さしすせそ」にも通じるでしょう.先人の経験の積重ねや実験・研究結果に基づく現状 では最良の知恵です.しかし,環境が新しくなれば,変わる事もあります.常に新たな発想とその実証を怠らずに良い製品を作ってください.
鋳鉄のインモールド法とコンバータ法を比較すると製品の特性に差がでますか?
【コンバーター法】 は,コンバータの底部の一角に孔の開けられた黒鉛製の仕切り板で囲まれた反応室を設置し,コンバータを水平状に倒した状態で,反応室にMgを装入して蓋を します. その後,反応室を下にして垂直に起こすことで,溶湯とMgが接触し反応するものです.反応状況のコントロールは仕切り板の孔のサイズで調整されます.
一方,【インモールド法】 は,鋳型内に球状化剤を入れる反応室を設け,脱硫した溶湯を注入すると反応し,その後鋳型の製品部分に入るものです. 鋳型内での反応であるため,これに使用される合金は4~6%Mg合金が使用されます.
両者の球状化処理方法の違いによる製品の特性の差は,インモールド法は,コンバータ法に比べ,Mg処理と同時に接種されるので,フェーデイングが起こり ません.したがって,薄肉鋳物でもチルが出にくく,黒鉛粒数も多くなり,安定した鋳物が得られます
同時に引け巣も発生しにくい.しかし,鋳型内に反応室 を設けるだけに,コスト上不利である.また,ドロス巻き込み欠陥発生リスクが高くなり,フィルターの活用が欠かせません.一方,コンバータ法は,高S溶湯 処理も可能で,歩留りもよく,コスト面で有利です
品質面において,清浄な溶湯が得られ易く,インモールド法とは違った特性を示します.
鋳鉄の引張り試験を行ったとき、明瞭な降伏(弾性限)が認められないのはなぜですか?
金属の塑性変形は,特定の結晶面を原子がすべることによって起こります.
すべりは転位が動くことによって生じます.転位が何らかの理由により固着さ れて,すべりが困難なとき明瞭な降伏点が認められます.たとえば,軟鋼の場合,炭素や窒素などの小さな原子は鉄の原子間に入り力学的に安定な状態を作りま す.
これをコットレル雰囲気といいます.このため,転位をすべり始めさせるためには大きなせん断応力が必要となります.この時の応力が上降伏点となりま す.一度すべりが進行したあとはコットレル雰囲気による原子の拘束が解かれているために転位は小さなせん断力で移動することができます.この時に下降伏点 を生じます.
FCやFCDのような鋳鉄ではマトリクス中に黒鉛を含有しています.降伏点近傍の応力状態では,黒鉛片縁部での降伏の進行,き裂やボイドの発生, 内部での微小損傷が進行しています.特にFCでは低応力域から局部的な降伏,塑性変形,部分的な破壊が同時多発的に連続して発生しています.
これらの応力 ‐ひずみ曲線へ及ぼす影響が転位の固着による変化に比較して非常に大きいため,全体としての明瞭な降伏開始点が現れません.
鋳鉄の引け巣試験をしたいと思っていますが、試験片の形状について教えてください.
一般に,「鋳鉄ではひけ巣は発生しない」としていますが,実際にはひけ巣が問題となることがあり,これに関する研究報告も数多く発表されています.
引け性の実験には,アルミニウム系では円錐形の試験片を用いたりしているようですが,鋳鉄では使いにくいと思います.これまでの報告で,球形,立 方体など形状を工夫したり,押湯寸法を変えたりした例がありますが,得られた数値(ひけ面積,体積,比重など)が何を意味しているか,実際の鋳物との関係 をどう考えればよいかなど,はっきりした結論を得た例は少ないようです.
ひけ性の実験をされるのであれば,何を調べたいか目的をはっきりさせることが大切です.ひけ巣の発生する要因として,鋳造方案,溶湯の化学成分, 鋳型の強度などが挙げられ,これらおのおのについての報告も数多くあります.これらをよく調べて,場合によっては自分で独自の形を考案することも必要かも しれません.
データを検討するときには思い込みや偏見は禁物ですが,自分の考えに沿って,はっきりとした結果を得られるように実験方法を考えることも大切 なことと思います.幸い,鋳造技術者であればほぼ思い通りの形を作ることが可能ですから,この特権を十二分に生かしてください.
球状黒鉛鋳鉄の黒鉛はどうして球状になるのですか?
これまでのところ球状黒鉛鋳鉄の黒鉛がどのようにして球状になるのかについて統一された理論にまでには確立されていません.
(i)核説(ii)過冷 説(iii)表面エネルギー説(iv)吸着説(v)転位説(vi)気泡説など,いくつかの学説が提唱されていますが,製造現場で球状黒鉛鋳鉄製品を鋳造し てきた回答者が理解している考え方を紹介します.
鋳鉄は鉄と炭素,シリコンを基本に硫黄,燐など鉄源から含まれる元素や多種の合金元素から構成されている.原材料を溶かす,鋳造するといった鋳造工 程を物理現象として捕らえるには,溶融と凝固という固体と液体との相の移り変わりを考えることになる.更に球状黒鉛鋳鉄に関しては材料を溶かして,凝固さ せるまでに球状化処理を行う.
純Mgを直接溶湯に添加する方法や合金化されたMgなどを添加することによって黒鉛を片状から球状に変化させることが出来る.しかしその過程を説 明するには,溶湯から黒鉛が生成するという液相から固相が晶出する現象と溶湯が段々と凝固していく時間を追って変化する固相と液相の割合の変化を考える.
鋳鉄溶湯から黒鉛が晶出してくるというのは凝固の過程で液体の鉄に溶け込んでいられない炭素が純物質に近い黒鉛になるということである.更に球状 になるというのには溶湯という液体中では異物質の黒鉛に対してあらゆる方角から力がかかる.よって黒鉛は表面積の最も小さな球状になると考えられる.また 最初に炭素が液体から出て来るにはきっかけが必要なはずである.
液体に溶け込んでいない不純物や高融点物質があれば,液体とその物質との界面には原子レベ ルのわずかな空隙ができそこを起点に炭素が凝集を開始して成長すると考えられる.もちろん成長しようとすると上記のような液体からの力が働き球状になる.
また凝固中に出来た空隙も上記同様に球体となりやすく,温度低下とともに溶けきれなくなった炭素が黒鉛として晶出する.またそれに伴い周囲に分子同士の摩 擦熱を発するので冷却時の過冷を打ち消すように潜熱の放出が起こる.球状黒鉛鋳鉄の判定を熱分析で行えるのはこれに基づいている.
因みに,凝固中に黒鉛が丸くになって生成してくるのか,途中から丸くなるのかをその場で観察して見極める最先端の研究が現在も行われています.
長時間保持された溶湯でつくられる鋳物は,化学組成が同じでも「チルが出やすい」,「引けが出やすい」のはなぜですか?
この問題を理解するためにはFe-C系平衡状態図を理解する必要があります.
すなわち,Fe-C系状態図で黒鉛共晶温度Tec,白銑(チル)共晶温 度Tezはそれぞれ1154℃,1148℃といわれています.両者間の温度差⊿Tcはわずか6℃しかありません.したがって,鋳鉄が共晶凝固時,黒鉛の晶 出の容易さにより共晶温度が変化し,黒鉛の晶出が困難であるほど大きな過冷温度(過冷度増大)が必要となります.凝固速度が速くなることにより黒鉛凝固 (成長)に支配される溶湯中のCの拡散距離は次第に短くなり,間に合わなくなる場合には黒鉛共晶凝固から白銑(チル)凝固に変ってしまいます.
そして,黒鉛共晶凝固の場合,黒鉛が晶出することにより体積が膨張します.一方,白銑(チル)凝固の場合は体積が減少します.
次に,溶湯を高温で長時間保持すると何が起きているかを考えると,凝固時に黒鉛化不足が起きます.
黒鉛化不足となった溶湯は仮に化学組成(例え ば,C,Siの黒鉛化元素)が全く同じであっても,黒鉛核物質の減少により凝固時より大きな過冷温度が必要となることが考えられます.
つまり,同じ化学組 成で長時間保持しなかった溶湯に比較して過冷温度が大きくなるため,よりチル凝固になる危険性(傾向)が増大します.その結果,チル化凝固傾向の強い溶湯 (黒鉛化不足溶湯)は鋳物の最終凝固部位(押し湯の補給が困難または不十分な場所)には体積の減少により引けてしまいます.
したがって,長時間の溶湯保持はできる限り避けなければなりませんが,万が一長時間保持となってしまった場合には,加炭や有効な接種を行うことを お勧めします.
しかし,保持前の元の溶湯状態(例えば共晶温度)に100%戻ることはできなくなるという実験報告があることを参考までに付け加えておきま す.
ひけ巣は,どうして厚肉部や交差部の中心付近に出るのですか? その対処法は?
まずひけ巣が発生するメカニズムを考えます.鋳型に充填された溶湯は,温度の低下とともに液体収縮を起こします.
冷却が進んで凝固が始まると固体収 縮が起こりますので,足りない分の体積は液体側から補給することになります.凝固が進むにつれて液体側からの補給量が増加していきますが,凝固が終わりに 近づくと液体の残分が足りなくなるため補給ができなくなり,足りない分は空間となります.この空間がひけ巣です.ひけ巣はこのように発生するため,ひけ巣 は最終凝固部に発生します.
厚肉部や交差部の中心にひけ巣が発生しやすいのは,これらの部分が最終凝固部だからです.逆に,ひけ巣が発生するのは最終凝固 部ですので,厚肉部や交差部でなくとも,最終凝固部であればひけ巣が発生する可能性があります.
ひけ巣をなくすためには,最終凝固部を製品外に移動させればよいので,押し湯や冷やし金を利用し,最終凝固部を押し湯などの製品外に移動させる方 法が効果的です.また,注湯温度を下げて液体収縮分を減らすことも効果的です.
鋳鉄の場合には,凝固時に黒鉛が晶出して体積膨張を起こすため,この体積膨 張を上手に利用することでひけ巣をなくすことも可能です.
電気誘導炉で溶かされた湯は原材料の成分に近いですが,キュポラの場合はC,P,Sなどが増えるのはなぜですか?
一般的に「誘導炉」には低周波,高周波という分け方と,るつぼ型,溝(チャンネル)型という分類があります.どちらにしても,容器の中に材料を入れて加熱 (厳密にはジュール熱,自己発熱)するもので,コップの中に水と塩を入れて温めるようなもので,砂糖を入れない限り甘くはなりません.
一方,キュポラは,簡単にいえば筒の中に材料とコークスを入れて風を送り,コークスを燃やしながら材料を加熱溶解します.溶けた材料はコークスの間を通過 しながら底にたまっていきます.高温で炭素と触れるので,鉄は加炭され,同時にコークス中の硫黄,燐なども入ってきます.溶鉱炉から出る銑鉄と似たような ものです.また,送風によって,燃えやすい(酸化しやすい)シリコンや亜鉛などは蒸発したり,スラグになって排出されたりして低下します.その程度は,温 度,炉形,送風量,コークス比など様々な要因によって変化します.
以上はごく一般的なことで,実際には炉の耐火物や雰囲気,スラグとの反応などで,るつぼ炉でも配合量からの計算と成分が異なることがあります.ま た誘導炉でもキュポラに似た構造のものがあり,このような炉では加炭されます.素形材センター発行の『鋳鉄の生産技術』*などをご覧ください.
*『新版 鋳鉄の生産技術』
発行:財団法人素形材センター
判型:A5判 625頁
価格:5250円(税込)
平成24年10月発行
ブローホール対策の一環として冷し金の適切な清掃や使用回数の設定/管理等が必要だと思いますが,なかなか情報がありません.冷し金の適切なメンテナンスについて教えてください.
確かに,“誰も聞かない,言わない”で,教科書的情報はありませんね.まず,冷やし金によるブローホールの発生原因から考えてはいかがでしょうか?
①冷やし金部位は溶湯が急冷されるために,溶湯表面の酸化被膜と共に空気も巻き込んで凝固してしまう場合,
②脱酸が不十分で凝固表面で発生するガスが急冷で表層に取り込まれる場合,
③湿気による水分が冷やし金表面にあり,水蒸気や分解,溶解したHが凝固時にガスとして捕獲される場合
④冷やし金表面の鉄酸化物が還元滓化し酸素が溶湯に取り込まれ,凝固表面で脱炭,リミングアクションとなり,急冷凝固で表層に取り込まれる場合
等が考えられます.
①は鋳込み方案も問題,② は製錬も問題,③ は鋳型にセット後の鋳型管理の問題もあるでしょう.④ は冷やし金そのものの管理の問題となるでしょう.
これらから,まず,溶湯に接する部分のサビは除去しておくこと,(ショット,グラインダ等での手入れ)鋳型にセット後の結露を防ぐこと(鋳型の熱 風乾燥等)が挙げられます.
海外のメーカで,溶湯側表面に被膜剥離できる塗料をぬっておき, 型被せ時に除去するというところもありました.回数はこれら の要因と冷却能としての,厚み,面積,重量,形状等の許容範囲から酸化ロスによる減量等を評価して使えるだけ使うと決めれば,と思います.
FCD450の黒鉛球状化率の算出で困っています。画像解析処理を使わず球状化率を算出する方法を教えてください.
超音波の伝播速度(音速)や共振周波数,打音試験などの非破壊試験があります.
測定条件と精度の関係から現場で普及しているのが音速法です.音速 (V )は,伝播媒体となる鋳鉄品のヤング率(E ),密度(ρ)からV ∝ √(E/ρ)・・・①で求めることができます.だからといって,これらの物性値を個々の鋳鉄で求める必要はありません.速度ですから伝播距離(L)と伝播 時間(T)からV=L/Tの式で計算できます.
音速測定が出来ても「音速と黒鉛球状化率との関係」が分からない.以下に双方の関係を説明します.
鋳鉄の名称に黒鉛形状が載っているのは,内在す る黒鉛形状がそれぞれの鋳鉄の機械的物理的性質を決定しているからです.ヤング率もその一つで片状<CV<球状の順に増加します.これらの鋳鉄の密度は, 約7, 000kg/m3(7.0g/cc)で大差なく,公式①から黒鉛形状と音速の関係が見えてきます.実際の黒鉛形状と音速の実測値より回帰式を作れば,音速 で黒鉛形状を推定できるようになります.
鋳放し球状黒鉛鋳鉄(球状化率80%以上)の音速は,5600~5700m/s,CV,片状黒鉛はそれぞれ 5200~5450m/s,4000m/s台の範囲です.詳細は6月開催のUT講習会に参加ください.
電気誘導炉で鉄原に銑鉄を使用するとひけ傾向が緩和されるのはどうしてですか? 銑鉄が白銑組織の場合と黒鉛が晶出している場合とでは違うのですか?
難しい質問です.銑鉄を使用すると,ひけ傾向がどう変わったか,ということを定量的に示した文献をあまり見たことがありませんが,現場的にはありそうな話です.
日本では,鋳鉄製造時には一般的に鋼屑を使用しますが,いろいろな事情から銑鉄を使うこともあります.鋼屑を使用すると加炭が必要ですが,銑鉄で は通常加炭は必要ありません.ひけ傾向が炭素量と関係がある(凝固時の膨張量は黒鉛量に対応する,とされている)とすれば,鋼屑の場合,加炭量が不足する ことがあると,ひけが出やすくなる,というのかもしれません.
炭素量のほかに,微量成分も鋼屑と銑鉄で異なることがあるのに加えて,加炭材に随伴する元素 もあるので,これらの影響でさらに差が大きくなるとも考えられます.加えて接種も当然黒鉛量に影響します.それならば,すべての成分,工程を同じにすれ ば,ひけ傾向は同じか? ということになりますが,可能でしょうか?
銑鉄の組織も高炉からの出銑時の状況等で種々変わりますが,ごく大ざっぱにいえば,白銑組織よりも黒鉛化している方が,再溶解して鋳物を鋳造して も黒鉛化しやすい成分になっているはずです.
黒鉛が大ければ凝固収縮はすくない,つまりひけ傾向を緩和する銑鉄となるでしょう.
なぜセメンタイト(Fe3C)をチルと呼ぶのですか? パーライトはフェライトとセメンタイトの積層組織と聞きましたが,このセメンタイトもチルなのでしょうか.
チル組織中のセメンタイトとパーライト中のセメンタイトを理解するには,Fe-C系状態図での安定系,準安定系状態図を見ていただく必要があります.図1にFe-C系状態図(炭素10wt%まで,標準状態)を示します.
図1 Fe-C系状態図
この図で,チル組織のセメンタイトは,溶融状態から1146℃で準安定状態を表す実直線の,E-C-Fでの共晶反応によって現れます.冷却速度が十分大きいとき,
L(液体)→γ(fcc)+Fe3C(斜方晶)
の準安定凝固が起こるのです.γ(オーステナイト)とFe3Cの共晶組織をレデブライト(ledeburite)といいますがこの組織は硬くて脆く,鋳鉄の破面に現れると白く見えるので,これをチル組織といいます.
パーライト中のセメンタイトは,図1中の723℃のP-S-K線での共析反応によって現れます.冷却速度が十分大きいとき,
γ(fcc)→α(bcc)+Fe3C(斜方晶)
のように,固相から2つの固相が同時に出てくるのです.この組織をパーライトといい,フェライト(α)とセメンタイト(Fe3C)が層状に重なった組織になります.これは十分な靱性があります.このようにFe3Cは状態図上の炭素量6.67%の縦の線上の化合物であり,結晶の種類としては同じものです.しかし,その生まれ方は異なっており,溶湯から凝固によって晶出したものがチル組織となります.
さて,ここまでは2種のFe3Cが,生まれは違うが結晶は同じだとしました.しかし,最新の研究では,図2に示したように1),パーライト中のセメンタイトは一体の結晶ではなく,数十ナノメートルの微結晶から構成されていることが判ってきました.
図2 パーライト中のセメンタイトの微細構造
すなわち,固相から析出したパーライト中のセメンタイトは,その結晶が不完全であることが判ります.パーライトを熱処理することによって,この結晶が構造を変えていることが明らかになりつつあり,この意味では2種のFe3Cが同じものではないことになります.
1)山口浩司:SEIテクニカルレビュー175(2009)57
熱処理すると鋳物の機械的・物理的性質が大きく変わると教わりましたが、アルミ合金や銅合金の鋳物では少なく鋳鉄だけ大きいのはどうして?
鋳鉄は室温ではフェライトとパーライトと黒鉛からなる組織ですが,これを熱処理して室温からゆっくり加熱するとオーステナイトと黒鉛の組織になります.こ の状態から冷却すると,共析反応によってオーステナイトがフェライトと黒鉛になります.その後,Fe3Cが析出しパーライト組織になります.
鋳鉄の熱処理 では,焼なましでは炉冷,焼ならしでは空冷,焼入れでは油冷または水冷処理を行うので,この熱処理の過程でオーステナイトからの冷却速度によって,基地組 織中のフェライトとパーライトの割合が大きく異なってきます.球状黒鉛鋳鉄の強度は基地組織に依存するので,熱処理によりフェライトとパーライトの割合が 変化すると機械的性質も大きく変わることになります.
例えば,球状黒鉛鋳鉄では,鋳放しで引張強さが450~500MPa,伸びが10~12%である材料 に,焼きなましを行うことによって強度はやや低下しますが,伸びは15~20%に上昇します.
また,焼ならしを行うと,引張強さは600~700MPa, 伸びは3~8%程度となります.そして,焼入れ・焼戻し処理を行うと引張強さは800~900MPa,伸びは2~3%程度になるようです.
鋳鉄の坩堝型誘導炉(3倍周波~500Hz)の500kg~2トンの炉材としてシリカ質のドライスタンプ材が使われているようですが,天然シリカと溶融シリカの違い,硼酸の添加量について教えてください
一般的に,誘導炉用酸性スタンプ材には天然シリカと電融シリカがあります.
天然シリカ材は天然シリカ:100%,電融シリカ材は天然シリ カ:50~80%・電融シリカ:20%~50%で形成され,両材質ともに硼酸0~数%を含みます.この硼酸ですが,シリカ自体は粒度と密度(充填状態)に よって差はあるものの,概ね1000~1200℃以上までは焼結(強度発現)をしないので,1000℃以下でも強度を発現させるためのバインダーとして添 加します.
硼酸量を変えることで強度の調整が可能ですが,天然シリカと電融シリカでも強度発現性が異なり,一般には天然シリカの方が焼結し易い性質を持っ ています.参考として表1に一例をご紹介します.
表1 ホウ酸量α%における天然・電融シリカ材圧縮強度一例
※)電融シリカ30~40%含有品
強度発現性以外にも,天然シリカは電融シリカに対して安価ですが,熱による構造変化(体積 変化)を起こし易い性質があります.このため,適用操業として天然シリカ材は温度変化の小さい低周波炉・連続操業,電融シリカは温度変化の大きい高周波 炉・急速溶解,間欠操業(全出湯)となります.
接種するとチルが消えるのはどうしてですか? さらにCrなどが高いとチルやひけ巣が出やすいのはなぜでしょうか?
鋳鉄は,二種類の共晶凝固の形態をとることが知られています.一つが鉄-黒鉛系で,もう一つが鉄−セメンタイト系です.
普通鋳鉄の場合,黒鉛系の共 晶温度の方がセメンタイト系より高いのですが,その差はあまり大きくなく,凝固時に少し過冷すると,セメンタイト共晶の温度に達しセメンタイトが晶出しま す.チルとは鋳鉄の凝固時に晶出するセメンタイトのことで,冷却速度の大きい薄肉部などによく現れます.
セメンタイトが晶出した鋳鉄は,硬く脆いので,セメンタイトを晶出させないように接種します.接種の効果としては,核生成の促進があり,共晶セル と呼ばれるオーステナイトと黒鉛からなる成長単位の数が増えます.接種により,あまり過冷することなく凝固しますので,セメンタイトが晶出しにくくなり結 果としてチルが消えます.
またクロム(Cr)が鋳鉄中に入ると鉄−セメンタイト系共晶温度が高くなり,鉄-黒鉛系共晶温度が低くなります.従いまして,ゆっくりとした冷却 の場合でもセメンタイト共晶の温度に達し,セメンタイトが晶出します.セメンタイトやクロム炭化物は,黒鉛に比べると密度が数倍大きいので,凝固時の収縮 が大きくなり,ひけ巣が出やすくなります.逆に言うと,他の金属材料に比べて黒鉛の晶出する鋳鉄はひけ巣が出にくい特殊な材料であるとも言えます.
超音波伝播速度を測定すると鋳鉄の黒鉛球状化率がわかるのはなぜですか? 球状化率は%で音速はm/sですよね?
超音波の伝播速度(音速)や共振周波数,打音試験などの非破壊試験が有ります.
この中で普及しているのが音速法です.音速(V )は,伝播媒体となる鋳鉄品のヤング率(E ),密度(ρ)からV ∝ √(E/ρ)・・・①で求めることができます.だからといって,これらの物性値を個々の鋳鉄で求める必要はありません.速度ですから伝播距離(L)と伝播 時間(T)からV=L/Tの式で計算できます.
音速測定が出来ても「音速と黒鉛球状化率との関係」が分からない.以下に双方の関係を説明します.
片状黒鉛-,CV黒鉛-,球状黒鉛鋳鉄など鋳鉄の名称に黒鉛形状が冠されているのは,内在する黒鉛形状がそれぞれの鋳鉄の機械的物理的性質を決定してい るからです.
ヤング率もその一つで片状黒鉛鋳鉄<CV黒鉛鋳鉄<球状黒鉛鋳鉄の順に増加します.これらの鋳鉄の密度は,約7, 000kg/m3(7.0g/cc) で殆ど差がなく,公式①から黒鉛形状で音速が変化することが理解できます.これまでに同じ製造履歴を有する黒鉛形状の異なる(フェーディングさせた)鋳鉄 の黒鉛形状(黒鉛球状化率,形状係数など)と音速の関係が調べられ,これらの間には非常に高い正の相関関係が存在していろとの研究報告が幾つもあります.
国内の報告では,日本鋳物協会,研究報告47(1987)が参考になるでしょう.
球状黒鉛鋳鉄用Y型供試材(Yブロック)の平行部から切り出した試験片の 機械的性質(引張強さ,伸びや疲労強度)は,切り出す位置で差が出ますか?
鋳鉄の機械的・物理的性質は,黒鉛形状と基地組織に依存しています.球状
黒鉛鋳鉄品の機械的性質は,JIS規格(JISG5502)のY型供試材の平行部であれば,JIS規格(引張強さ,伸び,衝撃値)の範囲ではどの位置から切出してもほぼ同等な特性が得られるでしょう.
とはいえ,「平行部の下部(底付近)では伸びが大きく,上部(押湯側)では引張強さが大きいという傾向がある.」という報告もあります.一度試してみてはいかがですか.
回答者は,Y型供試材の顕微鏡組織は,下部と上部で差があることを経験しています.下部は凝固が速く,そのため黒鉛粒数が多くなり,結果としてフェ ライト基地が多くなります.
一方,上部は凝固が遅いために黒鉛粒数が少なく粒径が大きくなり,含有元素の偏析も強くなっています.すなわちセル境界 は,MnやPなどの元素が強く偏析し相対的にパーライトが増えることになります.いわゆる鋳造という金属加工法に由来する肉厚感度です.このような顕微鏡 組織の違いは,JISの引張強さ(破断強度),耐力,伸び(破断伸び)には,はっきりした影響を及ぼさないが,疲労特性においては多少影響を及ぼすようで す.
一般に疲労強度は静的強度よりも内部の顕微鏡組織や微細な内部きず(ざく巣や点状巣のような)の影響を強く受けことが知られています.するとY型 供試材の上部は,最終凝固部に近いため微細な内びけ巣や微細な点状巣が存在する危険性があります.
さらに,凝固が遅いので黒鉛形状は崩れ粒径が大きくなる 傾向があります.これらは疲労き裂の発生個所のひとつとなるので上部から切出された試験片は疲労強度が低下する可能性があります.
チルと引け巣との関係を教えてください
引け巣もチル(遊離セメンタイト)も凝固完了までに発生します.チルが出ると引け巣が出やすくなります.「どうしてか?」を以下に説明します.
鋳鉄の溶湯は,溶媒が鉄で溶質が炭素の溶液です.溶液の温度が低下すると溶質の溶解度が下がり溶質が過飽和になり晶出 します.即ち,鋳鉄の溶湯から炭素が吐き出され,非金属の黒鉛(炭素の結晶)として晶出します.結果,高温の鉄(固体)であるオーステナイト中に黒鉛が3 次元に分散した鋳鉄(複合材料)が出来上がります.
溶湯の化学組成により初晶は異なりますが,共晶温度で共晶組成になった残湯の炭素濃度は同じ (CE=4.3%)です.この残湯がFe-G(安定)系あるいはFe-Fe3C(準安定)系で共晶凝固するのです.共晶凝固開始時の溶湯の炭素濃度は飽和状態にあるのですが,過冷や接種によるサイト(異質核,異質液体,ガスなど)やSi%のゆらぎ(濃淡)などにより過飽和になり,安定系では黒鉛,準安定系ではFe3Cがオーステナイト(CE≒2.0%)とともに同時進行で晶出し,凝固完了になります.
凝固は外側から始まり,それが容器になります.この容器の中にはまだ溶湯(液体)が残っています.液体は,温度が下が ると体積が減少します(液体収縮:1.5%/100℃).さらに,高温での鉄であるオーステナイトの晶出は,約3.5%収縮(溶鉄の凝固時のそれと同一と みなされるので)します.
一方,炭素は晶出して黒鉛になると,膨張して約3.4倍(ρFe /ρG,溶鉄の密度:ρFe=7.66g/cc,黒鉛は:ρG=2.26g/cc)になります.引け巣は容器内に残った液体・凝固収縮量と膨張量の差と考えられます.鋳鉄以外のほとんどの金属やその合金は収縮だけで凝固します.従って,鋳鉄品は鋳鋼に比べ引け巣が少ないものとなります.
ところで,チルはセメンタイト(Fe3C)とよばれる鉄と炭素の化合物(炭化物)です.前述の炭素が黒鉛として晶出せずに,Fe3Cとして凝固してしまうと,その分膨張が少なくなります.結果として引け巣が大きくなります.
以上,参考にして下さい.
詳しくは,張博ほか共編,川野ほか共著『球状黒鉛鋳鉄:基礎,理論,応用』の押湯無し方案の項をご覧ください.
(この本は絶版ですが、下記URLをクリックし,図書館で探してください.)
なぜ鋳鉄は鋼に比べ,錆が進行しにくいのでしょうか?
鉄は水に接すると鉄イオン(Fe2+)となります.そして,水中の水酸化イオン(OH-)と反応すると水酸 化第一鉄(Fe(OH)2)ができ,さらに酸化が進行すると水酸化第二鉄(Fe(OH)3)が出来ます.これがいわゆる赤錆と呼ばれるもので,この赤錆は 鉄表面には密着せず鉄を保護する力はありません.
鋼の場合,錆が進行するとどんどん剥がれ,酸化膜が腐食の防止の役割を果たしません.これに対して鋳鉄の 場合,鉄と黒鉛が存在し,この黒鉛は全く錆びず鉄分だけが腐食されます.この黒鉛を含む腐食層は,黒鉛そのものの機械的な固定効果(アンカー効果)がある ため剥がれにくくなり,腐食も進みにくくなり,結果的に腐食を防止する効果があるようです.
また,鋳鉄には2%程度のSiが含有するので,錆び層の安定化 効果により保護層(Fe-C-Siの混合層)が形成されるのです.腐食に対する基本的な性質は,鋳鉄も鋼も大きな差はありませんが,実環境中では鋳鉄の方 が良好な耐久性を示すことが多くあります.フランスでは,ルイ14世によって建役されたヴェルサイユの街と宮故に水を送るために1644年に約24kmに 渡って敷設された鋳鉄管は,百年以上もの長い間,錆にもまけず現役の水道管としての使命を果たしています.
参考文献として日本鋳造工学会編:鋳造工学便覧 (丸善)(2002)250,中村幸吉著:鋳鉄の科学(日本鋳物工業会)(2005)48があります.
鋳鉄の成長とはどういう現象でしょうか.何故発生するのでしょうか.
鋳鉄に加熱・冷却を繰り返すと鋳鉄寸法が少しずつ大きくなる現象を鋳鉄の成長(生長)と云います.
片状黒鉛鋳鉄の寸法変化の方が大きいですが,球状黒鉛で も起こります.鋳鉄を加熱した後に元の温度に戻しても鋳物寸法は元に戻ることはなく,不可逆的な現象として知られています.特にA1温度(共析変態温度) 以上に加熱されると成長量は大きくなりますが,A1変態以下の温度でも成長が起こります.
一般にパーライトがフェライトと黒鉛になるとセメンタイトの密度 よりも黒鉛の密度の方が小さいので鋳鉄の寸法は大きくなりますが,鋳鉄の成長はこの現象とは異なり,相変態がない場合でも起こります.
成長の理由については,「酸化説」,「き裂説」,「ガス説」,「黒鉛不可逆移動説」などが提案されており,長岡金吾による「黒鉛不可逆移動説」が最も支 持されております.この説によると,鋳鉄中の黒鉛は加熱によって減少するが,黒鉛はポーラスになる(長岡ら:鋳物 49(1977) p.742-746)ことで黒鉛サイズにほとんど変化は無く,そして冷却によって黒鉛は増加するがポーラスになった部分を埋めることなく既存の黒鉛が粗大 化するかマトリックス中の別の場所に析出すると説明されております.
成長に影響する因子としては加熱・冷却の温度と速度,組成,雰囲気,黒鉛組織が知られています.成長によって鋳物の寸法は変化すると同時に強度が低下し てしまうので,あまり歓迎されない現象ではありますが,黒鉛がポーラスになるので減衰能が向上するという良い所もあります(相馬ら:鋳物 55(1983) p.199-205).
共晶時のチル(共晶セメンタイト)とパーライトを構成するセメンタイトは同じものなのですか?
同じと思って良いと思います.
図は,鉄セメンタイト系状態図を模式的に表した物です.オーステナイトが冷却されていくと,フェライトとセメンタイトの2相に変化します.この時は,すべて固体なので,炭素原子も拡散しにくい状態になっており,細かい層状の組織が得られます.これがパーライトです.
チルの場合は,液体から2種類の固体に変化します.重量で炭素が 4.3%入った溶湯が冷却されると,オーステナイトとセメンタイトが出現します.この共晶組織をレデブライトと呼びます.温度も高く炭素が拡散しやすい状 態なので,セメンタイトが大きく出現し,脆い材料となってしまいます.
材料特性に与える影響は大きく異なりますが,状態図上では,共晶 変態で現れるセメンタイトも共析変態で現れるセメンタイトも温度が違うだけで,同じエリアに含まれています.すなわち,同じ物と言って構いません.ただ し,オーステナイトと平衡するセメンタイトとフェライトと平衡するセメンタイトの組成が若干異なることなど指定されていますので,完全に同じとまでは言え ないようです.
セメンタイトについて詳しく知りたい方は,下記の文献等をご参考に.
梅本,土谷:鉄と鋼,vol.68,(2002) 117
球状黒鉛鋳鉄のヤング率は何GPaですかと聞かれました.これはどんな時に必要で,その値も教えて下さい.
球状黒鉛鋳鉄のヤング率(縦弾性係数)は片状黒鉛鋳鉄の80〜130GPaに比べて大きい値であり,140〜170GPaの範囲にあると言われてい ます.
一般に鋼のヤング率は200〜210GPaなので,球状黒鉛鋳鉄は鋼の約70~80%と言えます.鋳鉄ではヤング率は,基地組織や強度よりも黒鉛の 形状及び分布状態の違いに大きく影響を受けると言われております.
そのため、黒鉛球状化率が低下すると黒鉛縁の応力集中やひずみが増加することでヤング率 が低下すると言われております.ヤング率は組織的には不敏感な性質であり,熱処理によって組織や強度など変化させても,ほとんど変わることはありません.
ヤング率の測定方法は様々な方法があり,静的もしくは動的に求める方法が知られています.測定方法により,原理,測定温度範囲,試験片寸法等異な るため,適切な方法を選定する必要があります.
静的試験(機械的試験法)には,引張試験,圧縮試験やねじり試験があり,ヤング率は応力−ひずみ線図の傾き から算出されます.しかし,試験片の品質や加工精度の影響が大きく,測定結果には若干の誤差が含まれます.
一方,動的試験では静的試験に比べて小型試験片 や脆性材料の測定も可能です.動的試験の代表的な測定方法として,振子法,共振法,超音波パルス法があります.共振法は試験片に機械的または電気的に強制 振動を与えて共振周波数(固有振動数)を計測し,この共振周波数からヤング率を計算する測定法です.
また,超音波パルス法は縦波用振動子及び横波用振動子 を用いて約1〜20MHzの超音波パルスを試験片に伝播させ,試験片内を伝播する縦波及び横波の伝播速度からヤング率及び剛性率を計算する方法です.
ヤング率は材料の外力に対する変形量の計算には不可欠なものです.例えば,負荷されている応力とヤング率から伸びやひずみを算出することができま すし,梁の撓みを求めたり,柱の座屈荷重を求めたりする時にも用いられます.
構造用部材として用いられる場合,ヤング率は安全な設計を行うための重要な値 の1つであると言えます.
FC200をある一定も応力で引張り続けた場合,徐々に亀裂が進展する ことはありますか? また,繰り返し疲労は起こりますか?
まず,FC200をある一定応力で引張続けた場合ですが,応力値が引張強さの60%以下等の応力範囲ならば,そのようなことは常温では起こらない.というのが一般的了解です.
次に,繰り返し疲労は起こりますか? ということですが,これについては,質問の意味が良くわかりません.「一定荷重(応力)を加えた上に,さら に繰り返し荷重を負荷する」という意味であれば,一定条件を満たせば( 修正Goodman線図など)疲労亀 裂が生じ,進展することになります.
「静的な応力の下で,繰返し応力による疲労と同様の現象が生じうるか?」という意味であれば,高応力下でそのような現 象が生じる可能性があるかもしれません.理由として,FC200くらいですと,引張強さの80%程度以上ではすでに局部的な微小亀裂(部分破壊)が多数生 じているからです.95%くらいでは,顕微鏡で明瞭に確認できるような大きさ の亀裂になっています.
したがって,荷重(応力)の継続によって,少しずつ亀裂が進展するということが起こりえると考えます. ただ,そのメカニズムは確定的ではありません.
鋳鉄にはどのような種類が存在して,どのように使い分けをしているのでしょうか?(質問者:LICCA)
鋳鉄の分類は,鋼に対する広義的な場合の鋳鉄という分類のほか,狭い意味で鋳鉄と呼ぶ場合は可鍛鋳鉄や球状黒鉛鋳鉄などに対して,単にねずみ鋳鉄(片状黒鉛鋳鉄)を指すことが多いです.表1に古い図書に載っている分類例を示します.表1に示すように,鋳鉄の名称は実に多種多様であって,同じ名称を人によって異なって使用することがあるので注意しなければなりません.また,最近の著書2)には黒鉛組織,基地組織,その鋳鉄の特徴を加味した鋳鉄の分類法があり,興味のある方はそちらの図書を参照されることを勧めます.
さて,鋳鉄はどのように使い分けをしているかとのお話になると,まずは強度や鋳造性,経済性(コスト)などによって使い分けされています.鋳鉄の使用が圧倒的に多い自動車の例でいうと,足回り部品の中の,サスペンション部品,駆動(ハブ,デフ,キャリア)およびシャシ部品(各種ブラケット,ビーム,サポート)では高強度・高靱性のダクタイル鋳鉄が多く使われています.また,同じ足回り部品でブレーキロータやドラムなど,エンジン部品でシリンダーヘッドとブロックなどでは一定の強度特性の他,熱伝導性や減衰性,耐摩耗性,そして良好な鋳造性および切削性を兼ね備えている片状黒鉛鋳鉄が用いられています.さらに,用途によって機能および経済性から上記両鋳鉄材の中間特性を有するCV黒鉛鋳鉄が使われる場合もあります。詳細な写真付実例は図書2)を参照ください .
1) 鋳鉄の材質 :(社)日本鋳物工業会編,コロナ社(1962)2
2) 新版「鋳鉄の材質」公益社団法人 日本鋳造工学会編,(2012)6,180
どうして,アルミニウムダイカストでは,ADC12が多用されるのでしょうか.
ダイカストの場合,その目的が ①大量生産 ②低価格(低コスト) を目的としております.それにより自動車,電気製品など大量消費財に多く利用されております.
①②を実現させるためには, a)大量一括生産・購入による低価格化(1kg材料を作るよりも1t作るほうがkg単位安くなりますね) b)単一生産ラインによる低価格化(複数の合金に対応するだけでも溶解炉・保持炉が複数必要になります.
合金の入れ替えだけでも時間・人などのコストがか かってきてしまいます.合金管理も煩雑になります) が生産上必要になります.使う側からしても非常に強度が必要な箇所や靭性を必要としているところは限られており,ある程度の強度があれば良いところが多く を占めています.
このようなところからある程度の強度,鋳造性をもった合金であるADC12合金が生産する上でも使う側からしても用いられるようになったと思います.当 然ADC12合金ではなく,ADC10合金でも良いわけですが,日本では大多数の自動車メーカーがADC12合金を採用していたため,いつのまにかすべて ADC12合金に統一されてしまったようです.
ダイカスト用のプランジャチップ潤滑剤にある種の粉体の潤滑剤を用いるとある種の油性の離型剤を用いた場合よりもADC12アルミニウム合金ダイカストの機械的特性と信頼性が優れる,という講演が3月10日名古屋で開催された「ダイカストの高品質化」シンポジウムでありました.粉体潤滑剤とはどのようなものか,もう少し詳しく教えて下さい.
3月10日名古屋での「ダイカストの高品質化」シンポジウムにご参加頂きまして有り難うございます.
簡単に申し上げますと,粉体潤滑剤(離型剤)とは,タ ルク(滑石),グラファイト(黒鉛),金属石けん,ワックス,珪藻土,h-BN,雲母などの粉末を混合したものです.
配合の比率によってチップの潤滑性能 と溶湯からスリーブへの熱伝達係数(熱の伝わり方)が変化します.たとえば市販品にはグラファイトとタルク,ワックスからなるものがあるはずですが,これ を1平方メートルあたり2グラム程度塗布しますと,ある種の油性の潤滑剤に比べて熱伝達係数が数分の1になることが測定の結果分かっています.スリーブの 温度を下げる効果もあります.
何社かのダイカスタやカーメーカは,この種の粉体潤滑剤を使用しています.国内では㈱アーレスティの青山氏がこの種の粉体離 型剤(チップ潤滑用ではなく金型キャビティ面塗布用)の開発において草分け的な存在です.青山氏は熱伝達係数の測定法も提案しており,私も青山氏の文献を 見て粉体が湯で押し流されないように多少改良をして熱伝達係数を測定しました.
しかし普及が限られている理由があります.個人的な見解ですが,例えば開発 セクションで良好な結果が得られても,量産時には粉体の吐出の安定性や,付き回りの均一性に問題が出たり,チップ潤滑性能が不足したりで現場泣かせになる ことがあるのでご注意下さい.
下記の文献などご参考に頂ければ幸いです.また当学会のダイカスト研究部会(神戸洋史部会長(日産自動車㈱))にご参加を頂 ければ幸甚です.
2000年の日本ダイカスト会議論文集JD00-11 Journal of Material Processing Technology, 130-131(2002),pp 289-293 青山俊三ら,鋳物, 64(1922),383
近年,高品質なダイカストを生産する技術として,「高真空ダイカスト」が適用されていますが,従来の「真空ダイカスト」との違いは何ですか.
従来の真空ダイカストは,キャビティ中のガスを積極的に逃がし,背圧をなくして湯流れを改善するねらいで使用されてきました.この方法では完全に空気の巻 込みを防ぐことができないため,溶体化を行うような熱処理や溶接ができず,また,機械的性質も合金そのものの性質より劣ることになります.
このような空気 を巻き込むことを回避するため,金型キャビティの空気を吸引し,真空度を上げるダイカストが登場し,従来のダイカストでは適用できなかった高い機械的特性 を要求される自動車のサスペンション部品や車体部品などに適用されるようになって来ました.この時の真空度は高ければ高いほど良いのですが,一般的には 5~10kPa以下であり,高真空ダイカストと呼ばれています.
金型キャビティを高真空に保つため,金型のパーティング面などにシールをしています.ま た,真空度を高く保つだけでなく,溶湯の脱ガスはもちろんのこと離型剤やチップ潤滑剤から発生するガスをできる限り少なくするような方策をとっています.
従来から用いられている真空ダイカストでも金型キャビティの空気を巻き込まないように吸引していますが,金型のシールがされていなかったりして,真空度は それほど高くは無く,熱処理や溶接はできません. 高真空ダイカスト技術は,ただ単に金型キャビティを高真空にするだけの技術ではなく,高品質を目指した総合的なダイカスト技術であると言えます.
ダイカストのエアーベントは厚いほどガス抜きの効果が高いと思いますが,どの程度まで厚くすることができるのでしょうか?
日本ダイカスト協会の『ダイカストの標準・金型編』には,「キャビティ内の空気やガスを金型外へ排出する方法としては,一般的にオーバーフローおよび 0.1~0.2mmで薄い板状のエアーベントが用いられている」と記載されています.
エアーベントは一般にこの厚みの範囲で用いられていますが,ダイカス トのガス抜きは厚みのみに規定されるのではなく,その位置が重要です.一般的には以下のように考えます. 1)溶湯が最後に充填される位置にする 2)湯口からなるべく遠い位置にする 3)溶湯が直接衝突する壁には付かない 4)鋳巣の多く出ている場所に付ける さらに大量のガス抜きを目的としたチルベントがあります.
チルベントはベントの形状が波状になっており,ベントの厚みは一般に0.4~0.6mm程度に設 定されています.チルベントブロックの材質や冷却の設置,溶湯の充てん速度,ベントの長さおよび巾の条件によっては,ベントの厚みをさらに厚く設定するこ とができます.
HPDCにてオーバーフローを設計する際の考え方はありますか?
オーバーフロー(以下,O/F)の機能には一般的に①溶湯充填時にガスや酸化物,介在物などを含んだ溶湯を製品部に残留させないよう排出する機能と,②金 型の特定部位の温度を上昇させるためのスポットヒーター機能とがあります.
まず,①の機能についてはO/Fの溶湯の入り口(O/Fゲート)が薄いと介在物が十分排出できないことがありますので除去方法と製品形状,肉厚が許容す る範囲でできるだけ厚くすることが望ましいです.ただ過剰に厚いと製品への欠け込みなどが発生しますので注意が必要です.またO/Fゲートの総断面積は ゲート断面積の50%程度を目安にするとよいと言われています.
配置については,基本的には大きなO/Fを少数設けるよりは小さいO/Fを多数設けた方が 良いとされています.詳細は(社)日本ダイカスト協会刊行の「ダイカストの標準 DCS-D1金型編」の記載内容をご参考ください.体積については狙うべ き溶湯の排出体積を製品から割り出し,まずはそれにならうことが良いと思います.
次に②ですが,これは比較的高度なテクニックです.ゲートから遠い製品端部などは型温も上昇しにくく,湯回りも悪化しがちです.型温を上昇させるには金 型にヒーターを入れるという手もありますが,設備等の費用がかかります.その場合,O/Fの熱量を利用することで比較的安価に改善することができます.
金型を暖めたい範囲に1つ若しくは複数のO/Fを配置すると良いでしょう.過剰な場合,型温の過熱による製品のひけ巣発生に注意が必要です.
O/Fへはエアベントを設置することがあります.その場合、O/Fに溶湯が充填完了直前までエアベントが開口し続けるようにエアベントの位置を工夫する のが良いでしょう.
AC4C等のアルミ鋳物の組織改良剤としてSr(ストロンチウム)がよく使われていますがこれは放射性物質と聞きました.人体に影響はないのでしょうか
ストロンチウムという元素は原子番号38の元素です.陽子が38個,中性子が46~53個,質量数(陽子数+中性子数)が84~91です.4つの安定同位 体(ストロンチウム84,86,87,88)と,3つの放射性同位体(ストロンチウム89,90,91)があります.
安定同位体のストロンチウムの存在比 はストロンチウム88が82.58%と最も多く,ついでストロンチウム86が9.86%,ストロンチウム87が7.0%で,ストロンチウム84は 0.56%とほんのわずかです.安定同位体は放射性物質ではありませんので,放射線を出しません.
放射性同位体のストロンチウムは,原子力発電の燃料であるウランが核分裂反応をする時にできる放射性物質です.ストロンチウム90は寿命が半分になる半減 期が約29年と長く,ベータ線を出してイットリウム90(放射性同位体)に変化します.これはさらに,ベータ線を出してジルコニウム90(安定同位体)に 変化します.
放射性同位体のストロンチウム90が危険なのは,半減期が約29年と長く,その間はベータ線などの放射線を出し続けることです.特に,カルシウムと似た性 質を持ち,体内に摂取されると骨の無機質部分に取り込まれ長く残留することです.放射性同位体は半減期が異なりますが,いずれも放射線を出しますので,体 内に摂取された場合には内部被爆という甚大な影響を受けることになります.
AC4C等のアルミ鋳物の組織改良剤として使われるストロンチウムは安定同位体ですので,ほとんどがストロンチウム88と思われます.従って,ベータ線な どの放射線を浴びることはなく,人体に影響はありません.
弊社では,アルミニウム合金低圧鋳造法を用いて,エンジン部品を生産しています.シェル中子を使用しており,中子砂排出のため焼鈍を実施しています.焼鈍工程を廃止した場合,素材の残留応力が問題になろうかと思いますが,製品として品質上悪影響が発生するでしょうか? また,残留応力を測定する方法として最適な方法はありますか? できれば非破壊検査方法があればありがたいのですが…….
御社が何度くらいで焼鈍をされていたのかわからないので,具体的な数値を挙げることはできませんが,焼鈍工程を廃止すると,鋳造時の凝固から離型において 発生する残留応力がそのまま維持されることが考えられます.
残留応力は,部品の形状や鋳造条件などにも影響されますし,また,製品内の部位によって異なり ます.そのために,残留応力が発生する部位と大きさを正確に把握する必要があります.引張残留応力は部品の実体強度や疲労強度を低下させると言われてお り,これらを考慮した部品設計が必要になります.
また,残留応力が発生しやすい部位には凝固時に温度差が大きくなる部位などがあり,例えば,厚肉部と薄肉部がつながっている部分では薄肉部に対する厚肉部 の凝固遅れにより応力が発生しやすくなります.従って,鋳造時に残留応力が発生しにくい形状設計も重要になります.
残留応力の測定には歪みゲージを使う方法が一般的ですが,破壊検査法であり,技能と時間を要するので工程能力を算出できるほどのデータが取れないことが多 く,測定対象とするサンプルの選定と測定部位の妥当性を考慮する必要があります.アルミニウム合金鋳物でも非破壊にて残留応力を測定する方法として,X線 や中性子ビームを用いる方法がありますが,コストが高く,また,設備も限られるため,一般的ではありません.
残留応力を含む鋳物の品質評価技術については,日本鋳造工学会編集委員会がまとめた「鋳物・ダイカストの品質評価技術ハンドブック-誰でもわかる事例とノ ウハウ-」が出版されていますので,参考にして下さい.
HPDCの真空弁にはどのような種類がありますか?
ダイカストの真空弁は,金型キャビティや射出スリーブ中の空気を吸引するために設置した真空配管を遮断して高速射出される溶湯の侵入を防止するために用い ます. 弁の動作はバネ,油圧,空圧や電磁力などのアクチュエータを用います.
真空弁は,動作を電気信号で操作するタイプと溶湯の圧力を利用して動作するタイプに 分類できます.電気信号で動作させるタイプには,マシンのシーケンサーを用いるもの,溶湯をキャビティ内で検知して電気信号を取り出すものがあります.溶 湯の圧力を利用するタイプには,弁が溶湯の圧力を直接受けるものとレバーを介して弁を閉じるものがあります.
どの真空弁も,弁に溶湯が侵入するトラブルが問題となり,その防止のために工夫が施されています.シーケンサーで動作する場合は,弁が閉じたことを検知し てから高速射出するインターロックで弁の詰まりを防止しています.いろいろな弁の違いは,弁の動作速度を早くする方法で主に特徴付けられています.
真空弁に連結するランナーの形状設計も重要なトラブル防止策であり,弁を用いる各社でそれぞれ工夫して使用しています. 特殊なものでは,チルベントを用いて溶湯を凝固させて,真空遮断するタイプの弁があります.
高品質ダイカストの種類の一つに層流充填ダイカストという方法がありますが,普通ダイカストとどのように違うのでしょうか?
一般ダイカスト法は寸法精度に優れた製品が成形できる反面,金型キャビティ内のガスが流動中に溶湯に巻き込まれやすく,製品の要求特性によってはこれが許 容されないレベルで製品内に鋳巣として残留している場合があります.層流ダイカスト法はそのような問題を解決するために考案された工法です.
この工法では,キャビティ内でガスを巻き込みにくくするため,溶湯を非常にゆっくりと充填します.ダイカストの一般的な充填時間は数十ms程度ですが,層 流充填ダイカストは数百ms~数秒です.ゲート速度も一般ダイカストでは数十m/sですが,層流充填法は早くても数m/s程度です.そのため,溶湯流動長 は一般ダイカストに比べて劣り,低速域でプランジャー速度のばらつきが少ないダイカストマシン,厚いゲート及びランナーの断面積,流動中の溶湯温度が下が りにくい断熱性離型剤やプランジャー潤滑剤などが必要です.
ゲートが厚いためプランジャーからの圧力伝播も向上し,凝固収縮巣も減少する傾向にありますが,専用の切断機が必要となります.
T7熱処理をすると,ワレが発生しました.対策はどのようなものがありますか?
例えば,シリンダヘッドのように,形状が複雑でクエンチ時に残留応力が生じやすいものなのか,原因はものによると思います.
まず,クエンチ時に残留応力が 発生すると考えて良いと思います.しかし,その時点では割れていないので,析出による寸法変化が鋳物の形状によって拘束され,引張応力を増長したのかもし れませんが,はっきりとしたことはわかりません.
また,析出によって硬さが増すと溶体化直後より延性が低下すると考えられるので,欠陥敏感性が高くなるこ とも考えられます.歪みゲージを貼って,逐次破断などで残留応力の状況をみつつ,FEM解析などでクエンチ時の応力解析を行い,安定化処理前の応力状態を みておくことが良いと思います.処方箋としては,割れ箇所が角部やコーナー部の場合,R処理が忘れられていないか? または適切なR処理がされているか? をチェックしてください.
形状変更が可能であるならば,Rを大きくしたりリブを追加したりすることで割れを抑えることが可能です.設計変更が難しいのな らば,クエンチをマイルドにする温水や油冷により冷却速度をおとすといったことが考えられます.これによりクエンチ時に発生する残留応力を緩和出来るかも 知れません.クエンチ時に部品の中に空気だまりがあって,焼き入れにムラがでていないかもチェックした方がよいかと思います.
時効硬化曲線の亜時効段階に,硬さ変化がおこらない停滞域が現れる理由は何ですか?
時効硬化は,時効析出相と転位との相互作用により転位の運動が阻害されておこる硬化現象です.時効硬化は一般に,亜時効,ピーク時効,過時効の段階に分け ることができ,亜時効では転位が析出相をせん断して通過し,過時効では析出相周りにループ(オローワンループ)を残して通過します.
このときに転位が受け る抵抗が硬化として現れるものであり,硬化挙動は析出相の形成挙動を直接反映します.Al-Cu系合金を例にとると,析出過程は,α→GP(1)ゾーン →GP(2)ゾーン(θ”)→θ’ →θ となります.ここで,θ相は安定相であり,GP(1)ゾーン,GP(2)ゾーン,θ’相は準安定相です.
Al-Cu系合金の場合,GP(1)ゾーンがまず 形成され,続いてGP(2)ゾーンが形成される間に停滞域が現れます.GP(1)ゾーンは形成されてすぐにGP(2)ゾーンに遷移するのではな く,GP(1)ゾーンとして一定の準安定状態(準安定溶解度線,一定体積率)を保ち得るからです.
別の言い方をすれば,GP(2)ゾーンに遷移するために はある障壁エネルギー(活性化エネルギー)を越える必要があり,このための潜伏期が停滞域でもある訳です.この関係は時効温度や合金組成によって変わり, たとえばソルバス温度(溶解度線温度)以上では時効初期からGP(2)ゾーンあるいはθ’相が形成されるため停滞域は見られなくなります.
他の合金系でも 複数の準安定相や構造変化がある場合に,同様に理解できます.
HPDCのスリーブに使われる材質にはどのようなものがありますか?
アルミニウム合金ダイカスト場合,射出スリーブには650~700℃の高温の溶湯が注湯されます.その際,給湯口の直下は,長期の使用によりアルミニウム 溶湯に侵食(溶損)されることから,アルミニウム合金ダイカストの射出スリーブは,一般的にはSKD61などの合金工具鋼が使用されます.
SKD61は, 0.32~0.42%C,4.80~5.50%Cr,1.00~1.50%Mo,0.80~1.15%Vを含む合金鋼で,高温硬さ,耐摩耗性,靭性に優れ ておりダイカスト金型の入れ子などに使用される熱間金型用材料です.さらに耐磨耗性を向上させる目的で、窒化などの表面処理したり、内面に耐溶損性,耐摩耗性に優れた合金を溶射したスリーブが使用されています.
そ の他,鋼に比較して熱伝導率が低く保温性に優れたサイアロンなどのセラミックスを射出スリーブに使用することもあります.これにより,射出スリーブ内での 溶湯の冷却・凝固を抑制し,ダイカストの機械的性質を低下させる破断チル層の生成量を低下させることができます.
また,プランジャーチップ(鋼製)と射出 スリーブの焼き付きを防止するためのチップ潤滑剤を低減でき,ガス欠陥を少なくすることも可能です.また,チタンにセラミックス粒子を均一に分散させた サーメット系の材料を使用することもあります.チタンは軽量で高耐蝕性,低熱伝導性であることからセラミックススリーブと同様な効果が期待されます.
JISには,なぜアルミ鋳物合金と, ダイカスト専用のダイカスト合金があるのですか?
アルミニウム合金の”一般的な鋳物”と”一般的なダイカスト”の製造法との間には,いくつかの大きな違いがあります.最も大きな違いは,鋳型への溶 湯(溶けた金属)の流し込み方です.鋳物では重力による流動を利用して,静かに流し込むのに対し,ダイカストでは,ダイカストマシンによる力で,高速高圧 で溶湯を流し込みます.
したがって,同じ金属製の鋳型(金型)を用いる場合でも,鋳物の場合は金型との反応によるトラブル(焼付きなど)はあまり心配する 必要はありませんが,ダイカストの場合には,金型だけではなく,溶湯側にも金型との反応を抑えるてだてを考えておく必要があります.このためダイカストに おいては,金型への溶湯の焼き付きを抑えるためにFe(鉄)が0.6~1.0%前後,有効成分として添加されています.一方の鋳物の場合には,Feをこの ように多く含むと,Feを含む大きな金属間化合物が発生し,機械的性質での”伸び値”(ねばり強さ)が
大幅に低下して,十分な特性を発揮できなくなります.したがって,Feは不純物として存在するため,0.5%前後以下に制限します.ダイカストでも Feを多く含むと同様の傾向が出てきますが,ダイカストの場合には金型による冷却速度が著しく速く,有害な金属間化合物は発生しにくいので,材料特性の低 下傾向は小さくてすみます.
このように鋳物とダイカストでは,主にFeの取扱を中心とした成分的な違いが大きいため,JISを含めた多くの規格で,鋳物用合金とダイカスト用合 金とを分けて規定しています.近年ではダイカストでの様々な技術の発展があり,溶湯の鋳型への充填を鋳物に近い低速とすることで,鋳物合金をそのままダイ カストに用いる例も見られます.
溶湯が充填する時に金型キャビティ内の背圧が問題となります.背圧を逃がすためのガス抜きの閾値はどの程度ですか?
ガス抜きは,材料(鋳鉄,アルミニウム合金),工法(ダイカスト,低圧鋳造法,重力鋳造法など)に限定されない鋳造という工法では共通して検討しな ければならない項目です.例えば,アルミニウム合金ダイカストでは,鋳物の高品質化に伴ってキャビティ内のガスを少なくするためにベントによるガス抜きを 行ったり,積極的にガスを抜く真空化,そして更なる高真空へと工法が進化してきています.
ガス抜きの無い単純な層流充填での鋳造を考えた場合,キャビティと同体積の空気(ガス)が溶湯の充填時に鋳造圧力で圧縮され,鋳造圧力と平衡状態 になると,それ以上の体積減少が無くなり圧縮されたガスはキャビティ内に残ります.キャビティ内に残ったガスが製品形状の表面部位なら欠肉(湯回り不 良),鋳物内ならガス欠陥(鋳巣)となり,どちらも欠陥となります.溶湯充填段階でガスが集中する部位にガス抜きがあれば,キャビティ内のガスを外に放出 できるのでガスが残らなくなり,ガス欠陥の無い鋳物を作ることが可能です.
実際の鋳造においては,単純な層流充填では無く,充填の先湯の乱れや溶湯の合流部位でガスを巻き込んだりして製品内にガスが残り欠陥となります. そのためキャビティ内に残るガスを可能な限り少なくし,ガス欠陥の防止につなげています.また,鋳物の凝固収縮段階では,鋳物内のガスがひけ巣の起点と なって,ガスとひけが混在した大きな鋳巣欠陥となることも多く見られます.
ガス抜きの閾値についてですが,キャビティ内にガスが残らないのが理想状態です.しかし理想状態と実際の鋳造にはギャップが必ずあり,閾値は部品 形状や部品に求められる要求性能によってさまざまであり,良品が必ず得られるという共通の値を設定することは不可能です.通常の生産では,試作段階でガス 欠陥の発生と背圧の関係を調査して個別に設定することで,最適な閾値を用いて生産をして行くのが一般的な方法になります.
HPDCのチップに使われる材質にはどのようなものがありますか?
ダイカストに使われるプランジャーチップの材質は,一般的にSKD61が使用されています.
SKD61のみで使用される場合もあれば,さらに耐摩耗性を上げるためにプランジャーチップ表面に溶射(金属系,セラミクス系など)をすることがありま す.ただし,闇雲に耐摩耗性を向上させることが良いことではなく,射出スリーブへの攻撃性なども考慮して表面処理を選ぶことが重要です(プランジャーチッ プよりも射出スリーブのほうが高価です).
海外ですとビスケットを早く固めることが目的で,熱伝導率の高いベリリウム銅を使ったプランジャーチップが利用されています.ベリリウム銅製のプラン ジャーチップは性能が高いのですが,高価であるため日本での使用は少ないようです.
最近では高真空ダイカスト専用(気密性を上げる)のチップ先端にバネ材 によるリングを付加しているプランジャーチップも使われています.
横型ダイカスト法でのセンターゲート方案の金型構造にはどのようなものがありますか?
センターゲートは,製品の内部にある穴や窓を利用してゲートを設けて溶湯を射出充填する方法です.溶湯を製品の中心部か ら放射状に均一に射出できるために円形の部品の寸法精度を高くすることができます.
古くはポーラック式ダイカストマシンに採用されていました.ポーラック 式ダイカストマシンは図1に示すように横型締め・縦射出のダイカストマシンで,加圧室内に上部の射出プランジャーと下部のカウンターピストンがあり,鋳造 合金が加圧室に注湯されると上部の射出プランジャーがカウンターピストンと一緒に降下して鋳造合金がノズルより金型キャビティに射出されます.その後カウ ンターピストンが上昇して,ビスケットをノズルから切り離し,金型が開いて製品を取り出します.
現在では,図2に例を示すように,固定あるいは可動の主型 が2枚の計3枚からなる3枚型が使用されます1).型開き時には固定型と中間型が開き,その位置で一旦停止してカットオフシリンダーでゲートを切断してランナーとビスケットを落下させた後にさらに可動型が開くものです.
1) 一般社団法人日本ダイカスト協会編:ダイカストの標準DCS D1<金型編>(2008)
図1 ポーラックダイカストマシン
図2 3枚型の例1)
展伸材が鋳物合金に混入して悪さをすることはありますか?
“あります”と考えるべきでしょう.以下に詳細を記します.
鋳物材(ダイカスト,鋳物を含めて)も展伸材も,大半の成分は同一と考えてよいので,特に区別する必要はないと思います.ただし,鋳物材の場合 は,”複雑形状を凝固過程で形成すること,鋳肌の大半をそのまま利用すること”が必要であるため,溶解,鋳造,凝固への悪影響がある成分は,極めて大きな 問題になります.
展伸材の場合はスラブやビレットが比較的単純な形状であり,また,鋳肌部分は除去するため,若干問題がある成分でも何とか対応できる場合がありま すが,鋳物では一般には複雑形状であり,また鋳肌をそのまま用いることが多いため,溶解・凝固時の挙動に対する影響が極めて大きく,問題になることが少な くありません.
凝固時の問題としては,Snなどのきわめて低融点の成分が多い場合に発生する割れが代表例でしょう.
また,溶解時の問題としては,航空機用材料などに用いられているLiが,硬い酸化被膜の形成や流動性の低下をごく微量でも発生させるので大きな問題になることがあります.
なお,Cdなどの法規制が問題になる成分もあります.展伸材の代表的な添加材であるTi-B系の結晶微細化材などは鋳物材にも有効に作用するので問題はありません.
幸いなことに,通常,大半の展伸材スクラップは一般的な配合調整だけで何とか使いこなせる状況ですが,問題になる材料が混入することが時々あるので,管理体制が重要です.
ダイカストで不具合が少ないエアベント構造とはどんなものですか?
エアベントの重要な機能は,キャビティから排出されるガスのみを通し溶湯を通さないことにあります.ダイカストのベント構造は大別してスリットベント,排気バルブがあります.
スリットベントの代表的不具合は,ベントに侵入した溶湯が張付き閉塞するもの,離型剤の残滓の堆積による断面積減少があります.前者には,溶湯侵入を防止 するためなるべく浅く幅広い形状が望ましいと考えます.後者には,ベント部への過剰な離型剤塗布を改善すること,定期的な清掃を行うこと,残滓の少ない離 型剤を用いることが良いと考えます.残滓は浅い形状にすると堆積しやすいので,可能な限り深い形状がよいと考えます.また,清掃しやすい構造とすることも 重要です.
排気バルブ式の場合,弁の閉動作の速度向上が重要です.弁体内に飛び込む粉状の凝固物を排出するエアブロー洗浄も,弁動作の再現性確保のために有効です. また,排気弁へ接続するランナー等には押出ピンなどの押出し機構を設置し,ショット毎の型からの排出を確実にする必要があります.押出し機構の設置はス リットベントに対しても有効な場合があります.
アルミニウム合金中の介在物の種類や成因を特定するのには,どのような分析法を用いるのが有効ですか?
アルミニウム合金中の介在物の分析法についてはPODFAという手法があります.溶融状態の合金をフィルタで濾すと,フィルタ上に介在物と晶出物が残りま す.
その介在物(必用に応じて化合物等の晶出物)をEPMA等で分析すると,生成原因について推定することが出来ます.炉や樋の耐火物か,溶湯表面で生成 したものか,もともとインゴットに入っていたものか,といったことを推定します.ダイカストの場合はチップ潤滑剤由来のもの,射出過程で溶湯が大気に触れ る間に生成した酸化物や離型剤由来のものも見つかる場合があるでしょう.
もっと容易に分析する方法としてKモールドの破面にあらわれた介在物を分析する手もあります.引張試験の破面にあらわれた介在物を分析することもありま す.ヨウ素とメチルアルコールの溶液で酸化物介在物を抽出する方法もあるようですが詳しくは存じません.どの程度の大きさの介在物を気にするかは,その鋳 物の使われ方,設計応力,疲労環境かどうか,などによるでしょう.
溶湯の品質評価を行ったときに出た介在物を外部委託で分析すると,アルミニウムカーバイドが検出されました.この物質の混入経路として疑われるものは何でしょうか?
アルミニウム合金溶解炉や保持炉のドロスやフラックス処理をした残灰のバケット,使用済みの黒鉛るつぼの近くでは,カーバイド臭がします.アルミニウムカーバイドはアルミニウム合金の溶解過程で生成します.
黒鉛系部材はアルミニウム合金溶湯と反応しにくく,濡れにくいため,よく現場で使われていますが,黒鉛と溶湯とが反応し,アルミニウムカーバイド(Al4C3)を生成します(1式).セラミックスとしての黒鉛はアルミニウム溶湯とは濡れにくいのですが,反応しやすいことが知られております.
また,耐久性が高いため,一般的に使われるカーボンボンド黒鉛るつぼには,炭化けい素(SiC)が含まれ,SiCも溶湯と反応し,Al4C3を生成します(2式).溶解温度が高い程,保持時間が長い程,Al4C3の生成反応が進み,生成量が多くなります.炭素の供給源としては,リターン材に付着した油や塗料などの種々の有機化合物もあります.
密度は2.36 g/cm3(室温)と溶湯密度に近いため,他の部材表面に生成し,炉壁や炉底にあったものが,フラックス処理や炉内の清掃などによって溶湯を撹拌したときに溶湯に巻き込まれ,介在物として出た可能性があります.
4Al+3C=Al4C3 (1)
4Al+3SiC=Al4C3+3Si (2)
アルミニウム合金ダイカストで可能な最小肉厚は?
アルミニウム合金ダイカストは,重力金型鋳造や低圧鋳造のような他の鋳造法に比べて薄肉化が可能なことが特徴です.G.Liebyは,ダイカストの大きさ及び合金種によって表1に示すような最小肉厚を提案しています.
表1 ダイカストの最小肉厚
しかし,最近では薄肉化への要求は高く,アルミニウム合金ダイカストではノートパソコン程度の大きさでも1mm以下の肉厚が求められています.薄い 製品をダイカストするためには,ある時間内に金型キャビティを充填完了する必要があり,この時間を充填時間といいます.F.C.Bennettや J.F.Wallaceなどにより様々な式が提案されています.最も簡便な式は,G.Ulmerによって提案された式(1)があります.元々の式 は,Fourierの熱伝導方程式と解いて厳密に計算したものですが,最終的には式(1)に簡略化されています.
t =0.033x2
ここで,tは充填時間(s),xは肉厚(mm)を示す.
仮に肉厚0.5mmを充填するためには,式(1)から8ms(0.008s)以内に充填を完了させる必要があることがわかります.理屈の上では,式 (1)の充填時間以内に充填が完了できる高速射出ができるダイカストマシンを用いれば,いくらでも薄肉化は可能ですが,現在のダイカストマシンの能力では 射出速度が8~10m/sが限界であり,薄肉化はダイカストマシンの能力に大きく依存します.もちろん,鋳造温度や金型温度などにも影響を受けます.現在 の薄肉化の実績では200×200mm程度の製品で0.45mm, 600×600mm程度で2.0mm程度が限界のようです.
また,ダイカストの機械的性質は,製品肉厚が薄くなるほど高くなる傾向にあります.これは,肉厚が薄いと冷却速度が大きくなりミクロ組織が微細に なることと,内部にひけ欠陥が発生しにくくなるためです.しかし,逆にある程度薄くなると湯流れ性が悪くなるため,湯じわや湯境などの湯流れ欠陥や割れ欠 陥が発生して強度が低下するので注意が必要です.また,肉厚が薄くなると製品全体の剛性は低くなるので,剛性が必要な製品の薄肉化にはリブ構造をうまく利 用する必要があります.薄肉化にあたってはこれらのことを配慮した上で取り組む必要があります.
近年,大型のダイカスト製品を鋳造するためにダイカストマシンも大型になってきているようです.世界最大のダイカストマシンのサイズはどの程度なのですか?
V6エンジンのシリンダブロックやストラットハウジング,センターピラーのような大型の車体部品を一体で鋳造するため に,大型のダイカストマシンが開発されてきています.ダイカストマシンのサイズは金型の型締力で表されることが多く,その値が大きいほど大型の製品を鋳造 することができます.
世界的に見ても大型のダイカストマシンを製造しているメーカはあまり多くありません.一般に市販されているダイカストマシンで最大のものは型締力52,000kNのもののようです.40,000kNクラスのマシンはいろいろなマシンメーカが製造しています.
大型の製品を製造するためには確かに大型のマシンが必要となりますが,マシンや金型のコストや維持,管理のためのコストもかかってしまいますの で,鋳造圧力を下げたり鋳造条件を検討したりして小さなマシンで鋳造できるような開発も行われています.現在のマシン以上の大型ダイカストマシンは今後も 出てくる可能性はあまりないと考えられます.
ダイカストのプランジャーチップ潤滑剤にはどんなものがあるのでしょうか?
プランジャーチップ潤滑剤の目的は摩擦抵抗の低減ですが,断熱による溶湯温度の低下防止を目的にする場合もあります.ダイカストには必要不可欠なものですが,潤滑剤からのガス発生によるダイカストの品質低下や射出部周辺の汚れなどのデメリットもあります.
大別すると,油性,水溶性,ペレット,粉体の4タイプがあります.潤滑成分である油脂分で構成された油性とその油脂分を乳化して水に分散させた水 溶性が一般的に使用され,それぞれに固体潤滑剤である黒鉛を添加したタイプがあります. 射出時の摺動が過酷な大型マシンでは油性が主流で黒鉛入りが多く 使用され,水溶性は小型マシンに使われることが多いようです.
ペレットタイプはワックスや低融点樹脂を主成分にした顆粒状で,給湯口からスリーブ内に投 入されるため,射出部周辺の汚れが少なく,近年の使用が増えてきています.
粉体はタルク,雲母などの無機粉と潤滑成分とから構成された微粉状で,スリー ブ内面に吹き付けて使用され,無機粉の断熱性と無機粉間に内包された空気層の構造的断熱性とで溶湯の温度低下,破断チル層の発生を抑制する効果がありま す.同様な効果を狙って無機粉を添加分散させた水溶性もあります.
これらの潤滑剤を目的,使用環境などにより最適に使い分けることが重要です.
熱ボリュームが少ない,中子ピンや駒は,焼きつきやすく,離型剤が乾燥せずに水残りが出やすいですが,良い対応方法はないでしょうか
細い中子ピンなどは,熱ボリュームが少ないため加熱されやすく,冷やされやすい.そのため溶湯充填時に,中子ピン温度が高くなりすぎ,表面で鉄とア ルミの反応をともなう焼付きが発生することがあります.また離型剤のスプレーにより冷やされすぎ,表面に付着した離型剤の水分が残ることがあります.
これが溶湯と反応すると水残り不良となります.さらに離型剤が乾燥しないために離型皮膜が形成されず,離型時の摩擦抵抗が高くなり,アルミが一部中子ピン表面 に残る,反応をともなわない焼付きが発生することもあります.このように細い中子ピンの使用には,焼付きや水残りなどの不具合が生じやすい問題がありま す.
この問題を無くすには,中子ピン温度が高くなりすぎないように,かつ冷えすぎないように中子ピンを冷却管理する必要があります.そのためには,市 販の冷却制御装置を使用するのが有効です.この装置を使えば例えば冷却孔がφ2で冷却パイプがφ1.2と細いものも冷却できます.
細い冷却パイプでも通水 できるように冷却水圧を高くし,冷えすぎを防ぐために冷却水をエアーパージする制御を行ないます.通水タイミング,エアーパージタイミングが遅れるのを防 ぐために,制御弁を金型近くに設置する工夫がされています.
このような冷却管理をしても離型剤の塗布により水残りが発生する場合があります.ミストを細かくして離型剤の跳ね返りを減らし,適切な量を塗布す る管理が必要です.最近では水を使わない油性少量スプレー法が実用化されています.この方法では,内冷強化した金型が必要になりますが,細い中子ピンの水 残り防止には効果的です.
最近の鋳造機は射出波形が見られるようになっていますが,波形はどのように活用したらよいのでしょうか
ダイカストマシンに表示される波形により,普段見ることのできない鋳造中のスリーブ・金型内の様子を確認することができます.この金型内部の様子 は,異常がない時は特に使用しませんが,不良が起きた際に何故不良になったかの原因やプロセスを見つける時に活用できます.下図に射出波形の一例を表しま す.
図の波形は高速からの波形で,射出速度・鋳造圧力・設定波形が描かれています.この波形で注目したいのが丸で囲った充填直後の圧力波形です.本来 であれば,設定波形のようにすぐ昇圧するところ,しばらく10MPa辺りで低迷し設定より75msも遅れて昇圧しています.
この状態ですと溶湯が凝固して から設定圧に到達する可能性が高く鋳造圧力は製品全体に届きません.その結果,鋳巣が大量に残ってしまい不良となります.また,更に詳しく波形を見ると圧 力が低迷していると同時に射出速度が上がっていることから二次充填を起こし,それが昇圧遅れの原因ということがわかります.
このように問題のメカニズムが解れば対策を講じることができます.この例では,鋳ばり対策やオーバーフローを減らすなどの対策により鋳巣を改善できることが予測できます.ここで射出波形が無いとどうなるでしょうか.
製品だけで確認すると内部品質が悪くなったという情報しか得られず何故悪くなったのかを特定できません.そのためどのような対策を取ればいいのか 解らず見当違いな方法を取る可能性もあります(例:内部品質が悪いと鋳造圧力を上げがち.
しかし今回の場合は昇圧時間が問題であり,鋳造圧力を上げても解 決できないどころか金型負担を増やし型寿命が短くなってしまう).これ以外にも射出速度が設定よりも低くなる原因や,理論的にではなく実鋳造時の高速切替 位置がゲート前・後どちらなのかも射出波形で確認できます.
このように不良対策のための原因究明には無くてはならない,それが射出波形です.
チップ,スリーブの寿命はどのように判定するのでしょうか?
プランジャーチップ,スリーブが摺動によって磨耗すると,増大した隙間にバリが差し込むことで,射出動作時の速度変動(速度の乱れ)や,バックフ ラッシュといった不具合が発生し,最悪の場合スタックに至ってしまいます.これが交換寿命を迎える最大の理由でしょう.
したがって,こういった不具合が生 じる隙間量に至る前に,各々の磨耗量の管理限界値を設けて交換基準とすることが必要になります.磨耗量の管理限界は,部材の形,冷却条件,鋳造条件などに よって異なりますので,使用環境に応じて設定します.
磨耗量を管理するには,
- 定期的にチップ外径,スリーブ内径を測定する.
- ショット数と磨耗量の関係を算出して,ショット数から磨耗量を推定する.
といった方法があります.
また,射出速度変動や抵抗油圧を直接監視するのも有効です.計測モニターで射出波形を確認したり,低速変動度と呼ばれるような演算値を確認したりし て,設定した管理限界値で交換するような基準を設ける方法です.この時注意が必要なのは,チップ,スリーブのどちらを交換すべきか,です.
まだ寿命に至っ ていない方を交換してしまうと無駄なコストが発生してしまいますので,チップ外径,スリーブ内径を測定し,磨耗の進行を確認した上で交換する部材を決める ことが重要です.
金型にはいろんな表面処理がありますが,選定に困っています.どのように処理方法を選定したら良いのでしょうか
金型の表面処理には,大きく分けて「拡散処理」と「表面被覆(コーティング)処理」があります.拡散処理は窒化に代表され,窒素,炭素などの原子を 金型内に拡散浸透させて型材成分である鉄,クロムなどとの窒化物,炭化物などの化合物を生成させて金型内側に硬化層を形成する方法です.表面被覆処理は金 型表面に皮膜物質を蒸着,反応創成する方法でPVD,CVD,プラズマCVD法があります.
表面処理の選定では目的,使用部位で使い分けることが最も重要となります. 窒化でもヒートクラック抑制には表面に化合物層がなく浅い拡散層の処 理が有効ですが,焼付き・溶損抑制はまったく逆で表面に化合物層を形成し拡散層が厚い処理が良いので,注意が必要です.一
般的には,長寿命を要望される キャビティ型はヒートクラック抑制がメインなのでガス窒化やガス浸硫窒化などが使用され,小型の入子や鋳抜きピンなどは定期交換が可能で焼付き・溶損抑制 がメインなので,塩浴窒化,塩浴浸硫窒化,TRDおよび表面被覆処理が使用されます.
表面被覆処理は拡散処理と違って,型材とまったく違った組成のアルミ溶湯と反応しない皮膜を形成できるので焼付き・溶損に効果が高くなります.目 的,使用部位を明確にして,窒化では化合物層の有無と拡散層の深さ,表面被覆では皮膜組成と厚さをどうするかを表面処理メーカーと相談しながら,処理方 法,処理条件を選定することが重要です.
金型が欠けた場合の補修方法はどのように行うのが良いでしょうか?
ダイカスト金型においては,主にSKD61やそれ相当の材料を用いていることから,補修方法としては溶接復元での補修が一般的に行われています.
先ず溶接材としては,マルエージング鋼が一般的です.その理由は,施工後の硬度が低く靱性に富む為,比較的溶接がしやすい事と溶接後の加工が容易な点が挙げられます.
一般的なTIG溶接施工の場合,洗浄→開先加工→予熱→溶接→後熱→加工→完成検査の順で行われます.
洗浄工程では施工部周囲の油脂・溶湯・ゴミ・さび等の溶接欠陥の元となる不純物を除去,開先加工工程では割れや亀裂を完全に除去し同時に鋭角部や極端なへこみ等も削り取り,溶接しやすい形状にします.
予熱工程では,低温割れ予防,変形抑制,残留応力の抑制の為,溶接部付近の温度を200~250℃,金型端部を100℃以上の目安とし,ガスバー ナーで金型全体を暖めたあとに溶接します.溶接終了後は,再度,ガスバーナーにて後熱を施し,急冷防止の為に断熱材で金型を養生,時間をかけて金型を冷却 します.
溶接部位の形状復元には,直彫り加工など適切な方法を選択して行い,加工完了後は修正部位の形状測定や探傷検査などを経て補修が完了します.
ダイカスト金型の冷却孔からワレが発生した場合に,冷却を止めて,外冷で鋳造することが有りますが,冷却孔が割れた場合の良い対処方法はないでしょうか?
冷却孔から金型表面に割れができてしまっている場合,の対処の仕方ですが,緊急で対処する場合では,下記が考えられます.
1)質問者のように外冷で対処する
2)ロジックシールなど吸引負圧による冷却を行う
3)溶接で塞ぐ
ただし,上記の場合には永久的な対処方法ではないので,金型の割れが広がる恐れがあります.出来るのであれば,金型を下ろして割れ近辺を切り取り,入れ子にするのが良いと思います.
ダイカストの焼付きはなぜ発生するのですか?
アルミニウム合金ダイカストでは,アルミニウム合金が金型に付着して,金型表面上に残る現象を焼付きと呼んでいます.
しかしダイカストには二種類の焼付きが存在します.一つは金型に付着したアルミニウム合金を苛性ソーダなどで溶解除去したとき金型面にアルミと反応した痕が残る場合です.もう一つはきれいにアルミニウム合金がなくなり,平滑な元の金型表面状態に戻る場合です.この二種類の焼付きは,その生成原因が異なるので対策する上で注意が必要です.
前者の焼付きは,金型とアルミの合金反応が原因です.ダイカスト時のアルミニウム合金と金型の界面温度が高温となり金型面にAl-Si-Feの金属 間化合物層を形成しアルミが金型に付着する現象です.反応が起きる温度は,金型の材質や,アルミニウム合金の成分,離型剤の種類とその付着状況,表面処理 などによって異なります.ADC12合金で,離型剤がない条件下でのSKD61との反応温度Tは,次の式によって求めることができます.
T=847-13.5ln(t) ;ここで,tは保持時間である.
後者の焼付きは,金型とアルミニウム合金との反応を伴わないものです.アルミニウム合金の強度よりアルミニウム合金と金型間の摩擦力が上まわったときに起きます.式に表すと
σ(アルミニウム合金の強度)<F(摩擦力)=μN
;ここでμは静止摩擦係数,Nは押付力
生産現場で摩擦力が大きくなるのは,離型剤の付着が一番大きく影響します.離型剤が適切に付着すると,摩擦係数は0.2程度と低く,アルミニウム合 金の強度より摩擦力が大きくなることはありません.しかし離型剤の付着が無い場合は,摩擦係数は1.0以上になります.アルミニウム合金は金型の中で凝固 し収縮します.円筒形状のような鋳物では,アルミが収縮して押付ける力が内側の金型に作用します.この押し付け力によりアルミニウム合金と金型面に摩擦力 が働きます.離型剤の付着が少ない場合,摩擦力はアルミニウム合金の強度より大きくなる場合には,アルミニウム合金が破壊して金型面上に残ります.
生産現場では,前者の焼付きに注目しがちです.しかし後者の焼付きが起きている場合,対策が裏目にでる場合があります.金型温度が冷えすぎて,離型 剤皮膜が形成できずに摩擦力が大きくなっている場合に,離型剤をさらに増やして金型を冷却しても焼付きはなくなりません.この種の焼付きでは金型温度を離 型剤が良く付着する140℃~240℃の範囲にする対策が有効です.
ダイカスト製品取り出し後の水冷にはどのような意味があるのでしょうか?
製品を型から取出した後の水冷にはいくつかの目的があります.一般的なダイカストにおいて行われる水冷は,通常,できるだけ早く製品を冷やしてゲートの切 断やバリ取りを行うことを目的としています.
早く冷却することで,短いサイクルタイムでの生産を可能にします.T5処理を行う製品では,材料に含まれる銅 やマグネシウムを過飽和に固溶させて機械的強度を向上させます.重力鋳造や低圧鋳造の鋳物において行われる取出し後の水冷は,ほとんどの場合,T5処理に おける機械的性質の向上を目的としています.
いずれの鋳造法においても,できるだけ高い温度から冷却することによってT5処理後の強度を高くすることができますが,安定した強度を得るためには,水 没時の鋳物の温度と水温を一定にすることが重要です.
逆に水冷するときの水温や浸漬のさせ方によっては,ひずみ,変形あるいは鋳ぐるみ材のはがれなどを生 じさせることがあるので注意が必要です.あまり実施例は多くないかもしれませんが,T5処理を行わない製品でも自然時効による強度向上を狙って意図的に水 冷を行う場合もあります.
特殊な例としては,アブレーション鋳造のように,水流で砂型を除去するのと同時に鋳物も急冷し,ミクロ組織の微細化や固溶量の増大による高強度化を図る 鋳造法もあります.
ダイカストにおいて製品の一部が金型に残るトラブルが発生しています.そのたびに鋳造を止めて溶解除去していますが,何か良い防止方法はありますか?
このような現象は,金型内に残っている部分の離型抵抗が押出し力や製品の破損した部分の強度よりも高い場合に発生すると考えられます.
一般的に離型抵抗よりも押出し力が高くなるように金型は設計されますが,離型抵抗は金型の形状や表面状態,使用している離型剤等に大きく影響され ます.まず,製品形状で押出し方向に対しアンダーカットが無いこと,次に,製品が残る部分の金型表面状態にて焼き付きなどが発生していないか,焼き付きが あれば対象部への離型剤等が塗布されているかを確認してください.
また,製品離型時に製品が押出し方向に対し斜めになっていないことも重要です.製品が破損する部分は表面状態に異常は見られないが,他の部分で製品が引っ掛かり,離型時に製品が斜めに押し出されるため,結果としてアンダーカットになってしまう場合もあります.
最後に,対象部位の抱きつき力を検討し,最適な押出し力や押出しピンの数を設定する事を推奨いたします.
アルミニウムダイカスト製品に肉が厚い部分があり,圧漏れ不良が発生しており,困っています. 良い対策方法はありませんか?
圧漏れ不良は鋳肌もしくはその加工面(外部)と内部との相互貫通によって発生します.
したがって該当する漏れ部位の①鋳肌もしくは②加工面の状態,③内部品質のどれかが健全であれば,圧漏れを防ぐことができます.
1)鋳肌品質の向上に対しては鋳造欠陥である湯境いや凝固割れ,製品形状や型表面の状態,ダイカストマシンなどが要因であるかじり,冷間亀裂の発生対策が有効です.
2)加工面の品質については,加工代をチェックしてみてください.ダイカストの表面には非常に健全な急冷組織(チル層)が0.5㎜前後形成されま す. 加工代はこの範囲を大きく超えないことが理想です.過大な加工代は健全層を除去し,内部欠陥を表面に露出させる危険があります.
3)内部については,この場合引け巣がみられると思います.当該部の断面を切断・研磨し観察したうえで同定すべきでしょう.対策としては,適切な肉 盗みによる最終凝固部の極小化,金型の内部冷却強化による引け巣の分散,局部加圧による引け巣への溶湯補給が挙げられます.製品の外周部に厚肉部が存在し ている場合,方案や製品レイアウトを変更しゲートからの圧力伝搬を向上させる手段も有効と思われます.
ダイカストのプランジャーチップ潤滑剤の塗布で注意しなければいけない点を教えてください.
ダイカストでは高速高圧で充填するプランジャーチップ,スリーブには大きな摺動抵抗が掛かるため,それを低減する潤滑剤の役目は重要である.
種類を 大別すると水溶性,油性,ペレットの3種類がある.大型マシンはチップ表面積も広く,荷重も高いので,より潤滑性が高い油性の採用が多い.しかし,油は気 温による粘性変化が大きく夏冬での吐出量が変化したり,溶湯に巻き込まれてガス化して鋳巣や湯回り不良になったり,火災の危険性などの問題もあるので,負 荷が少ない小型マシンの場合は扱いやすい水溶性が採用されている.ペレットは新しいタイプで小型~中型に使われ始めており,顆粒状の樹脂などで構成される ので,油よりガス化しにくく潤滑性もやや高く油性と水溶性の中間的なメリットがある.
その他には,スリーブ内での溶湯凝固を少なくするため,断熱性の高 い無機粉と粉状の樹脂やワックスを混合した粉体潤滑剤が使われることもある.各種類には,高温潤滑性を強化するため,黒鉛,二硫化モリブデン,テフロンな どの個体潤滑を添加したものがある.
塗布方法にも違いがあり,ガス化しやすい油性ではスリーブ外部に出たチップ上端に滴下して溶湯への混入を避けるが,水溶性,ペレットタイプは給湯口 からスリーブ内にスプレー,投入する方法が取られる.そのため,射出部周囲の汚れは,油性は多いが給湯口内に入れる水溶性,ペレットは少ないなど,環境面 から選択される場合もある.
亜鉛合金ダイカストの経年寸法変化はよく知られているのですが,アルミニウム合金ダイカストの経年寸法変化は起きるのでしょうか
亜鉛合金ダイカストの経年寸法変化は,粒間腐食により寸法変化が起こり比較的大きいため,よく知られております.
アルミニウム合金ダイカストの場 合,粒間腐食が起こることはないので経年寸法変化は亜鉛ダイカストに比べればごく小さいですので,一般的には寸法変化は起こらないとされております.しか しながら,一般的に用いられるADC12合金(またはADC10合金)は,銅やマグネシウムが含まれている時効析出型の合金であるため,時効により微小に 変化します.
そのため,寸法が安定化するまで放置してから使用するか(自然時効),200℃程度でT5処理をし過時効させること(人工時効)で,寸法の安 定化を図るのが良いと思います.求められる精度や使用される環境によって放置時間や熱処理時間を変えることが望ましいと思います.比較的高温環境で使用さ れるのであれば,銅やマグネシウムを含まないADC1合金などを用いるのもいいかと思います.
また,ダイカストの場合には,残留応力が残っていますので経年寸法変化と言うよりは形状変化が起こります.その場合にも,200℃程度のT5熱処理を行うことで寸法を安定化させることが出来ます.
「アルミニウム合金ダイカストで,ゲート断面積やオーバーフロー断面積の厚みと幅で理想的な比率はあるのでしょうか?
まず,湯口ゲートについて考えます.湯口ゲートの形状に要求されるのは,充填時のゲート速度を適正にするための断面積を設定することと,充填完了後になる べく長い圧力伝播時間を確保することです.
断面積を小さくすればゲート速度を速くできますが,凝固完了が早いために圧力伝播時間が短くなります.つまり, このバランスで断面積を決定することになります.その上で,同じ断面積において,厚さと幅の比率で凝固時間がなるべく長くなる形状を考えると,理想は 「幅=厚さ」ということになります.
これは,充填中のゲート抵抗を最小限にするという観点からも同じ結果が導かれます.しかしながら,ゲート厚さが近傍の 製品肉厚以上になると,ゲート切断,堰折りといった工程で,最脆弱部が製品部になってしまうことから,製品の歪みやクラックなどの問題が生じる可能性が高 まります.
また,そもそも,薄肉が特徴のダイカスト製品に,極端に厚いゲートを設置できる場所を見つけるのは困難でしょう.これらを総合的に考えて,幅と 厚さの比率を決めるのではなく,「設置できる最大の厚さ」を設定し,「必要なゲート断面積を考慮して幅を決定する」,という手順が良いと考えられます.
オーバーフローは,ガスや不純物を含んだ先湯の排出が主目的です.この目的に対しては,必要な体積を確保すれば,厚さと幅の比率は問題にはなりません.し かし,同じ体積のオーバーフローを考えたとき,薄すぎると,投影面積が増えて,充填時の型開き力が増加してしまいます.逆に厚さを大きくとると,金型から 抜けにくくなり,押し出しピンの設置の必要性などの弊害が生じます.
また,薄くて広いオーバーフローは,広範囲の金型温度を少し上昇させ,厚くて狭い場合 は,局部的に大きく上昇させます.こちらも,幅と厚さの比率を定義するのではなく,状況と目的に合った形状を設計する必要があります.
ダイフリッパーでの型合わせでは平衡がきちんと出ているのに,鋳造時にいつも同じ位置からバリ吹きしてしまいますが何が原因でしょうか.どう対策すればよいでしょうか.
バリ吹きの箇所にもよりますが,湯口よりも遠いところでバリ吹きが発生する場合は,湯口部が熱膨張し型合わせの当たりが部分的に強くなることが考えられま す.冷却経路,冷却条件,クリアランス等をチェックすると良いと思います.
また,キャビティ表面から入熱した熱が奪いきれずに型の裏面まで加熱され金型の 蓄熱分布の温度差が大きくなることで見切り面の平面度がバラつくことがあり,キャビティ近傍以外の金型蓄熱部への冷却回路設置する対策が有効になります.
入子と主型のクリアランスにより入子の熱が主型へ伝熱するか断熱するかが決まってきます.熱伝達の差を均一にするクリアランス管理も重要です.型合わせ確 認を実鋳造機と異なる設備で確認した場合,実鋳造機の摩耗等,例えばダイカストのトグルピンの劣化,プラテンの摩耗なども考えられます.
テストブロック型 等で調査し調整・修復が推奨されます.いずれにしても平行度が保たれないまま繰り返し鋳造することで型や設備への劣化が著しくなるため早目のケアが必要で す.
アルミニウム合金の再生塊にはどんな材料(スクラップ)が使われているのでしょうか?
アルミニウムが主成分であれば,ほとんどが原料(スクラップ)として使用できます.一度,製品として使用され,不要になりリサイクルされるスクラッ プ.例えば,自動車関係ではエンジンブロック,シリンダーヘッド等,建築関係では,アルミサッシ,道路の標識等,その他にも,アルミ缶,アルミ鍋等もあり ます.
また,アルミ製品の製造工程で発生する切り粉(ダライ粉)も原料として使用します.加工方法の分類では,圧延品,鍛造品,電線,鋳物,ダイカスト, 粉末冶金等で作られた製品も原料として使用できます.
原料としての使用可否は成分分析をして判断します.例えば,Liの含有量が高い場合は使用しない.成分分析の結果より規格に適合するようにスクラッ プの種類と量を調整します.よって規格が違えば配合するスクラップの種類,量が変わります.
例えば,ダイカスト用アルミニウム合金のAD12.1であれ ば,FeやCuの規格が緩く,多種多様なスクラップを使用できます.鋳物用のAC4C.1の場合,AD12.1と比較して,FeやCuの規格が厳しい分, 使えるスクラップの種類が少なくなります.
アルミニウム合金ダイカストADC12は,なぜアルマイトが難しいのでしょうか.
アルマイト(陽極酸化)処理は,硫酸,しゅう酸などの溶液中で金属を+極にして電流を流すことにより発生する発生期の酸素と金属イオンを直接結合し て金属の表面に酸化アルミニウム皮膜を多孔質状に形成させることです.そのため,被処理材料の化学組成の影響を強く影響します.
アルミニウム合金ダイカストのADC12は,流動性向上のためにけい素が9.6~12.0%と多量に含まれています.このけい素は半導体であるこ とから,金属組織中に微細に形成される共晶のけい素が陽極酸化処理の際に酸化しない,または成長量が少ないために,非処理材料の表面に酸化アルミニウム皮 膜が均一に生成しにくくなります.また,表面の色も灰黒色となってしまいます.
一部のメーカーでは前処理工程(ダイカスト表面層のけい素を取り除く)を工夫して陽極酸化を行っているところもあります.
中国からのREが入手困難になり昨年末は騒ぎが大きくなりました.今年に入り一段落ついたようですが,鋳鉄用黒鉛球状化材におけるREの役割について改めて教えて下さい.
REとは
REはRARE EARTH の略.希土類 と訳されています.
希土類元素は,周期表3(A)族であるスカンジウム(Sc),イットリウム(Y)およびランタノイド15元素を合わせた17元素です.ランタノイドにはLa,Ceなどがあります.
REが鋳鉄の黒鉛球状化材に使われた経緯
現在アルカリ土類金属のMg,Caなどが入った球状化材を使った黒鉛球状化処理が一般的に普及しています.
球状黒鉛鋳鉄が開発された当初,鋳鉄中のS(硫 黄)やO(酸素)と親和力が強い元素としてMg,Caが単独で使われていましたが,鋳鉄の片状黒鉛の形状とは異なる黒鉛形状を呈した白銑から熱処理で作る 可鍛鋳鉄(今ではあまりなじみがなくなりました)に比べて熱処理時間が短く,延性に優れている点で工業化技術が急速に進み,球状化処理用の合金の開発に伴 う鋳放し球状黒鉛鋳鉄が使途を広めていきました.
REを含むミッシュメタルは鉄鋼では強力な脱酸効果があるということで使用されていました.一方,純Mgを使ったコンバーター法でも球状化処理に併用されていました.なお,REと言ってもCeが全体の約50%,Laは約30%またほかの元素も約20%含まれています.
Mg合金におけるREの役割
通常使われている球状化処理材には45%SiをベースにMg3%から7%,RE1%から2%,Ca2%,Al0.5から1%などが含まれています.
まずメインのMgによって脱酸,脱硫されます.その結果Mgと酸素や硫黄との化合物が黒鉛の核となると言われています.Mg自体は鉄にほとんど溶け込みま せんので蒸発し,時間とともに効果が斬減 (フェーディング)すると言われています.
Ca,Alはどちらかというと必然的に含有している元素で意図的な添加によるものではありません.Caは1%か ら2%含まれていますが,Mgの酸化物や硫化物に比して沸点が高いため,反応の激しさを抑えることができます.一方多くなるとノロが増えます.
Alは脱酸材として広く知られていますが上記同様1%から2%含まれ,低めに抑えたものはノロが発生しにくくなります. さてREは酸素,硫黄との反応性(親和力)が高く,添加によって鋳鉄溶湯の脱酸,脱硫が行われます.
Mgのフェーディングをカバーして球状化不良を抑制します.また,今般スクラップ材料に含まれている球状化阻害作用を持つ元素を中和する作用もあるとも言われています.
REの役割としては
球状黒鉛鋳鉄を製造するには球状化材にREが含まれたものを使った方が簡易で安定した品質が得られると言えるでしょう.ところが,これは肉厚が30mm以 下の小物中物製品を対象にした話です.
大物の200kg,500kg,1トン,10トンの製品になるとREが逆にチャンキー黒鉛の原因になる場合もあり, 鋳造品の肉厚による凝固速度の相違の問題になります.これに関しては別途解説をしていきます.
実体鋳物では,急冷組織にしても思うように材料特性が上がらないのはなぜでしょうか?
鋳物の凝固組織は通常デンドライト組織を有し,凝固組織すなわちデンドライト組織は冷却速度に依存します.
また,材料特性である機械的性質はこのデンドラ イト2次アーム間隔に依存性があり,一般的に,急冷組織(組織を細かくすること)にすることにより材料特性を向上させることが出来ます.逆に鋳物において 材料特性を低下させる要因の一つは材料内外に欠陥となるものを含むことであり,その代表例としては,外部欠陥の湯境,内部欠陥の引け巣,介在物,ガスの巻 き込み巣,ダイカストであれば,破断チル層などです.
実体鋳物では前述した欠陥を皆無にすることが難しいため,急冷しても上記欠陥により思うような材料特 性が得られない場合があります.また,急冷組織を作るために金型が冷えすぎていて湯境欠陥が増えていたり,凝固バランスが崩れて溶湯補給が不十分になり引 け巣が発生したりなど欠陥を増やしてしまうこともあります.材料特性を向上させるには急冷することばかりでなく,鋳造方案の見直しや製品形状の見直しなど も必要になってくると思います.
指向性凝固とは、どういうことですが? 定量的に表現する指標はどんなものがありますか?
一般的に鋳物を全体的に同時期に凝固させることよりも,一定方向に順次凝固させたいことが多くあります.この後者の凝固形態を指向性凝固といいます.
金属 溶湯は凝固する時に体積収縮、つまり凝固収縮が発生します。そのため、鋳物や鋳塊を外周部から凝固させると、鋳物の中心部などは凝固収縮による溶湯不足で 引け巣などの鋳造欠陥が発生しやすくなります。これを防止するために凝固形態を指向性凝固にする方法があり,その具体的な方法として砂型鋳物などに冷し金 や押し湯を用いることがあります.なお、単結晶タービンブレードなどを製造する特殊な一方向凝固法も含まれる場合もあります。
指向性凝固を実現させるためには、最初に凝固させたい押し湯側とは逆の部分に冷し金を用いて冷却を速くし、押し湯部分に向かって徐々に凝固が進行するよ うにします。この時、鋳物の断面形状や鋳型の熱伝導、また湯流れを工夫したり、押し湯部分を保温したりします。そして、押し湯部分が最後に固まり、そこに 引け巣などの鋳造欠陥が集中するようにします。
凝固の指向性が十分かどうかの定量的な指標として,(1)凝固時間の順序(凝固時間が端部または冷し金の位置から押湯に向けて単調に変化するかどう か),(2)凝固時の温度勾配,(3)凝固時の温度勾配と固液界面の移動速度との比などがあげられます.このような指標の推定は、鋳物や鋳塊の形状、鋳造 金属(純金属か合金か共晶合金かの違い)により種々様々であり,短く単純形状の鋳物では,それほど複雑ではありませんが、長尺で複雑形状の鋳物では様々な 工夫が施されているため、推定が難しいと思います。
なお最近では、凝固シミュレーションソフトにより個々の鋳物形状に適した押し湯や冷し金位置などを予め 設計することができるようになってきています.
シミュレーションの上手な使い方,限界について教えてください.
鋳造CAEにおけるシミュレーションと言っても,湯流れシミュレーション,伝熱・凝固シミュレーション,熱応力シミュレーションなど多種があります.
開発 と適用の歴史から,伝熱・凝固シミュレーションと湯流れシミュレーションもほぼ実用域に到達していると推測できます.熱応力シミュレーションやその他の造 型シミュレーション,マイクロシミュレーションなどはもう少し時間が掛かるでしょうか.
では,何をもって実用的か否か判断しているのでしょうか.色々な考え方があるかと思いますが,ある程度のCPU計算時間で,ある程度の(欠陥予測の)精 度,を得ることができるか,に尽きると思います.この「ある程度」が微妙で,使っている計算機PCの処理速度&メモリに依存しますが,2時間後に結果が欲 しいとか,終業前に計算を開始して翌日の始業時間に終わって欲しいとすれば,10時間ほどになるでしょうか.このように限られた時間内に,如何にほしい精 度レベルをもった計算結果を得ることができるかが重要です.
これに大きな影響を与える要因の一つがメッシュの大きさと総数です.メッシュを小さく分割する と基本的に精度が上がり小さな欠陥も予測できますが,逆に計算時間が長くなり大容量のメモリも必要となります.大きなメッシュでは計算時間は短いですが予 測できる欠陥レベルもおおざっぱです.また解析精度には,物性値をはじめとするパラメータの精度,時間や温度の依存性なども影響を与えます.これらを踏ま えて,各ユーザは自分に適したデフォルトの解析条件を見つけることが,上手な使い方の一歩だと思います.
もう一つのシミュレーションの限界ですが,理論的には「ない」と思います.ただし,計算機の能力とソフトウェアの機能を考えれば実用上の制限はあると思い ます.前述のとおり,時間を限定すれば計算(予測)できる内容や精度には限界があります.また,シミュレーションソフトに所望の理論解析が組み込まれてい るか,理論と実現象との検証は十分なされているかの問題もあり,この意味でも限界があるでしょう.
ただし,これらはマシン性能の向上,また検証実験や結果 比較が進むことで順次改善されていくものと推測されます.
EPMAとはどういう分析方法なのでしょうか.
EPMAとは,Electron Probe(X-ray) Micro Analyzer:X線マイクロアナライザの頭文字をとったものである.材料の表面形態を観察する顕微鏡の一つであるSEM(Scanning Electron Microscope:走査型電子顕微鏡)に波長分散形X線検出機(WDXあるいはWDS:wavelength-dispersive X-ray spectrometer)を取り付けて,試料表面の元素の同定や定量分析をする装置のことである.
EPMAは集束レンズ,対物レンズ等の電子レンズで電 子線を絞り試料表面に照射する際に,電子線が通過する経路にある走査コイルで電子線を任意に操作して,自由に試料上を動かしながら,試料から発生する電子 [反射電子・吸収電子・2次電子など]と電磁波[X線や光など]などの信号を電子検出機とX線検出器で検出する.この時に,試料に含まれる各元素から発生 するそれぞれの特性X線をWDXで測定することで,精密な元素分析や,X線スペクトル解析による試料の状態分析ができる.
EPMAと類似の分析装置として,高分解能のSEMにエネルギー分散形X線検出器(EDXあるいはEDS:Energy dispersive X-ray spectrometer)をつけたSEM-EDXもよく知られている.最近の技術の進歩も著しく一概には言えないが,高い分析精度を求められる場合には EPMA,高分解能が要求される場合はSEM-EDXを選択するなどの使い分けもされている.
介在物と結晶核との違い,境目は何でしょうか?
金属中の介在物とは,溶湯または固体状態において素材とは違う固体物質で,元々素材に含まれていない異種物質を言います.耐火物や溶解用機材が破損し,溶解時に混入したものや溶湯酸化によって混入した酸化物も介在物です.介在物は鋳造品の特性に悪影響を与えるものです.
金属の凝固過程で,溶湯から最初に結晶の種である核ができます.核に金属原子が規則正しい構造になるように付着していき,やがて大きな結晶に成長 します.凝固するときに核が沢山できると結晶が微細化します.また,溶湯に結晶の核となりうる異種物質が多く存在すると,その周りに原子が付着し,成長し ていき,微細な結晶になります.
異種物質が結晶の核となるためには溶湯と濡れやすく,それぞれの特定の結晶面が上手く重なる条件が必要です.濡れやすいと溶湯から直接に核を生成 するよりも低いエネルギーで異種物質の表面に金属原子が付着するため,結晶が成長しやすくなります.
アルミニウム合金では,チタンやほう素が凝固時にAl3TiやAlB2のような核物質となる元素であり,鋳鉄では接種剤が溶湯の酸素や硫黄と反応し,黒鉛の核物質となることが知られています.
客先で加工して鋳巣不良で返品されて困っています.納入前に選別する方法はありますか.
鋳物実体内部の傷を探すには,超音波探傷試験(UT)と放射線探傷試験(RT)があります.試験箇所が決まっているならば,UTを用いることができ ますが,複雑形状で探触子を当てられなかったり形状と傷が干渉したりする場合は,良い試験結果が得られないこともあります.
全体を透過してみたいなら ば,RTを使うことをお奨めします.試験方法はJISH0522(アルミニウム鋳物の放射線透過試験方法及び透過写真の等級分類方法)を参照されると良い でしょう.一般に,RTでは放射線を遮蔽できる部屋と資格認証を有する技術員が必要になります.
出典;第161回(2012.10.盛岡.講演No.117
今日では,コンピュータ断層撮影(CT)技術が進歩して鮮明で精度が良く,かつ立体で内部観察ができる装置が市販されています.内部傷がそのまま立体で観察でき,今まで出来なかった傷の深さもわかります.
X線CT技術については,装置取り扱い企業の専門技術者に問い合わせください
木型の改造はコスト管理上,どの業者さんも普通に行っている事とは思いますが,改造するにあたって気をつけなければアドバイスをいただけると非常に助かります.
自硬性法で生産される小ロット品においては,設計変更等での木型改造は避けて通ることが出来ない対応だと思います.一方で,部品供給等でエンドユー ザーから設計変更前の素材供給を求められることもありますので,各社ともご苦労をされておられることと思います.
そのような木型改造の各社共通的なガイド ラインは無いように思いますが,弊社での対応を紹介することで回答に替えさせていただきます.
弊社でも,貴社と同じように,設計変更による木型改造対応は日常的に発生しています.また,一つの木型で設計変更に伴う複数図番へ対応するという 兼用木型を多数有しております.設計変更による木型改造の必要性があった場合,まず,「入子」による兼用化を検討します.これは,木型費の削減を目的して 必要最小限の部分交換方式による兼用化を図るものです.
入子化における具体的な木型製作方法(例えば,アリによる入子固定等々)は,木型業者さんがプロと してご承知でしょうから,木型業者さんに相談されることが早道であろうと思います.その際,最も重要なことは,兼用木型における入子間違いをどのように防 ぐかです.
弊社では,木型本体に入子位置と図番を明記し,更に兼用木型一つ一つに改造来歴を記録したカルテを作成し,図面と共に保管しております.兼用木 型の注文を頂いた場合には,木型管理者が受注伝票の図番を確認し,カルテと照合しながら入子を準備するという仕組みを作っております.また,木型倉庫から 造型場に木型を搬入する際に,木型管理者と造型責任者が図番と入子の照合をするというダブルチェックをしております.
いずれにしても木型改造による木型兼用化においては,改造の手法よりも兼用化による図番と木型形状の間違いをどのように回避するかという仕組みづくりが大切だと考えます.ご参考になれば幸いです.
外びけと内びけの関係を教えてください.
凝固は外から始まります.鋳物は鋳型内壁との接触部から個体になり内部に液体が残ります.
内引け巣は,内部に残る溶液の液体収縮と凝固収縮によって引き起こされると考えて良く,鋳鉄は,溶湯に含有されている炭素が晶出(黒鉛)する分ので膨張が あります.総収縮量>膨張量の時に引け巣が発生します.実用的に鋳造加工されている金属・合金は,収縮だけで膨張がなく自然に冷却凝固させると内引け巣が 発生します.
一般に物質の液体でも個体でも密度(単位,g/cc)は,温度が高いほど低くなります.空気や水が温かいと上昇し,冷たいと下降するのは,温度に よる密度差です.高気圧も低気圧も温度による密度差です.高気圧は冷たくて重く,低気圧は温かく軽いので上昇気流となります.同じ重さでも温度が高いほど 膨張し体積が増えます.即ち密度が下がり軽くなるのです.
次に外引け巣について,外側に作られる殻が強固なものなら内引け巣が,殻の一部に弱い所があれば,内部残液の収縮に引きずられて凹みができます.これが外引けの原因です.発生する場所は上方面が一般的で,常に湯圧が掛かっている下型面には出ません.
現場で湯流れを簡単に調べる方法にはどんな方法がありますか?
湯流れ性を評価するには様々な方法があります.まず,合金特性としての湯流れ性は,渦巻き試験鋳型や直線状試験鋳型,真空流動性試験鋳型を用いて 「流動長さ」を測定して評価されます.
渦巻き試験鋳型は,蚊取り線香のような渦巻き状の狭い溝を設けた鋳型の中に溶湯を一定の条件で鋳込み,流れが止まる までの長さを測定して評価します.直線状鋳型は,溝が直線状に設けられたものです.また,真空流動性試験鋳型は,真空にした(厳密には減圧した)金属のパ イプの中に溶湯を吸い上げてどの程度の長さまで吸い上げることができるかで,流動性を評価するものです.
そもそも,流流れ性が良いとか悪いとかは合金成分や組成だけで決まるものではなく,表面張力や表面の酸化状態など溶湯と雰囲気との関係や,鋳込み 温度や鋳型温度あるいは鋳込み速度,ガスの抜けやすさといった鋳造条件によっても大きく変わります.したがって,先のような試験方法によって求められた 「流動長さ」はあくまでも参考程度になります.実際に製造現場で,湯流れ性が問題となるのは,未充填,湯境,湯じわなどがほとんどです.
ダイカストでは,しばしば湯流れの状態を評価する方法としてショートショット方を用いる.ショートショットとは,実際に射出・充填する量より少な い溶湯を射出スリーブ内に注湯して,射出・充填することで,充填途中の湯流れ状態などを確認する方法です.この方法で,金型キャビティでの溶湯の充填順序 の確認や,未充填,湯じわなどの湯流れ欠陥の発生箇所の確認などが可能です.
以前は,射出ピストンの前に加熱して柔らかくしたビスケットを挟んでピストンが分流子に直接衝突することを防止するなどの工夫が必要でした.しか し,今日のダイカストマシンは,射出制御技術が進歩してきており,射出を途中で止めることができるので,ショートショットはかなりやりやすくなっていま す.
ちなみに,射出成形では,ショートショットは成形品の一部が欠けや不完全な形状の成形品を生ずる現象のこと,つまり充填不足のことをいうそうです.